高い自動化率で多品種のエンジンを一気に製造するヤンマーのマザー工場「びわ工場」の中を見てきました
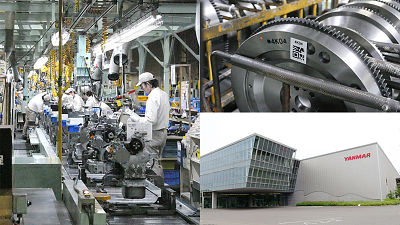
農業機械をはじめ、建設機械や船舶、さらには発電装置などのエネルギーシステムというふうに、ヤンマーはさまざまな機械や装置を開発して世に送り出しています。今回は滋賀県長浜市にある「ヤンマーミュージアム」に加え、ヤンマーの主力エンジン工場のひとつで最新設備が投入されているという「びわ工場」(一般非公開)の中に入れることになったので、一体どんな風にエンジンが作られているのか見てくることにしました。
ヤンマー
https://www.yanmar.com/jp/
ヤンマー・びわ工場に到着。工場は滋賀県長浜市の琵琶湖のほとりに位置しています。
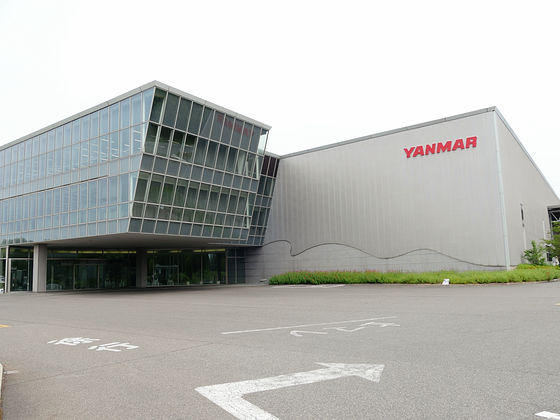
エントランスを入ると、工場で生産されているエンジンが展示されていました。びわ工場はヤンマーグループにおける立形水冷ディーゼルエンジンのマザー工場として位置づけられており、1995年に操業を開始。生産ラインの自働化率を高め、顧客のニーズにきめ細かく応えるための多品種・少量生産技術が磨かれてきたとのことで、この工場で培われてきた生産技術が他の工場にも活かされることから「マザー工場」と呼ばれているそうです。
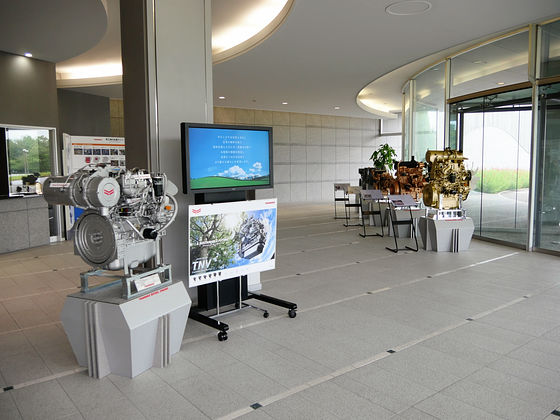
この工場で生産されている最新の環境規制に適合した産業用ディーゼルエンジンの「TNV型」。「Tier 4」と呼ばれる環境規制をクリアした最新型のディーゼルエンジンで、コモンレール式の燃料噴射装置や電子制御、排ガスに含まれるススなどの粒子状物質(PM)を回収するDPF(ディーゼル・パティキュレート・フィルタ)と呼ばれる装置を搭載することで、吸った空気よりもクリーンな排ガスを出すことすら可能なエンジンとなっているとのこと。
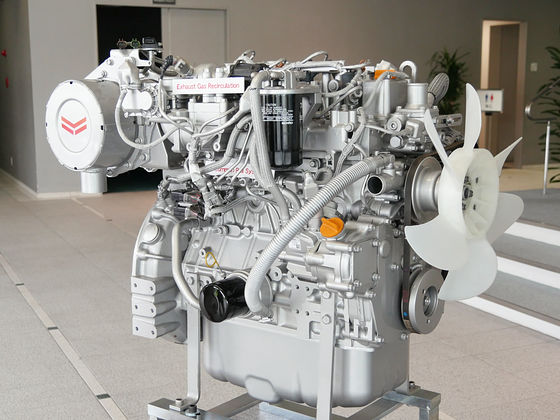
過去に生産されていたモデルも展示されています。このエンジンは、びわ工場で初めて生産された「TNE型」エンジンの初号機。びわ工場では、操業開始から20年にあたる2015年8月に小形産業用ディーゼルエンジンの生産累計が500万台を突破したそうです。
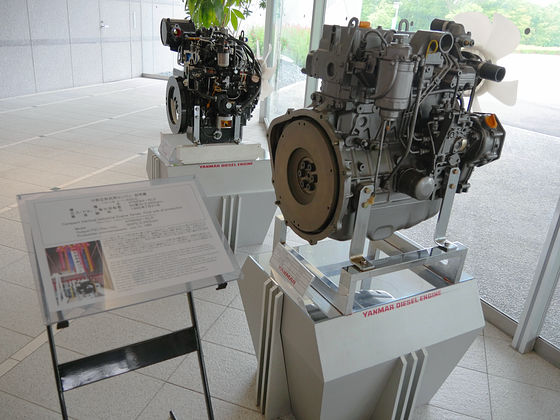
びわ工場はエンジンを生産する専用の工場となっており、年間40万台のエンジン生産能力を備えています。生産されているエンジンは農業機械のディーゼルはもちろん、建機用のディーゼルエンジンやエネルギー(発電)用のディーゼルエンジン及びガスエンジンなども生産されているとのこと。また、ヤンマーでは他社向けにエンジンを生産する事業も行っており、誰でも聞いたことがあるような大手建機メーカーの車両にヤンマーのエンジンが用いられていることも多いそうです。
工場内に入ると、びわ工場の概要などをまとめ、工場全体の改善活動にも使われるコーナーが設置されていました。内部は工場特有の熱気と、油の匂いが感じられます。
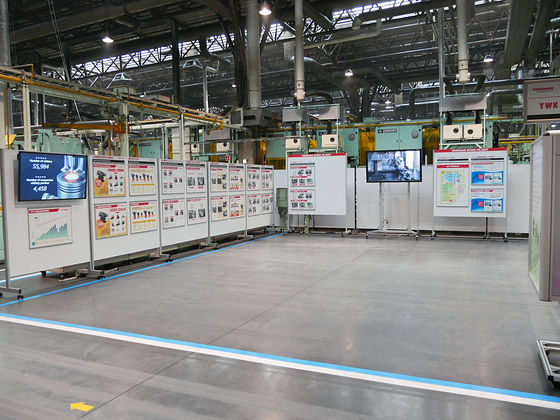
びわ工場では「平準化生産」と呼ばれる考え方を取り入れ、さまざまな品種のエンジンを同じ生産ラインで組み立てることに対応。これにより、多岐にわたる顧客からの受注にも柔軟に対応することを可能にしています。
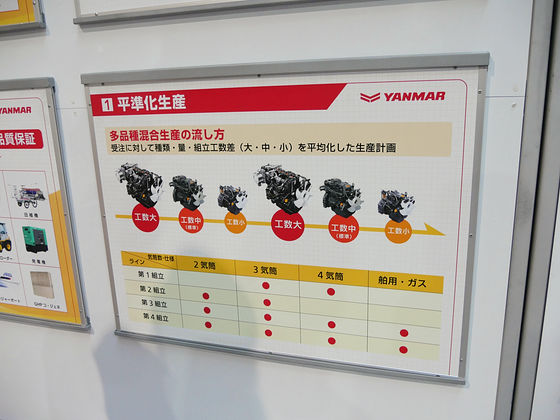
エンジンが変われば取り付ける部品の大きさや数が異なることになりますが、この工場の生産ラインは独自の生産管理システムを取り入れて対応。具体的には、全ての部品をバーコードやIDタグで管理することで生産を管理するほか、生産履歴の管理にも役立てられているとのこと。
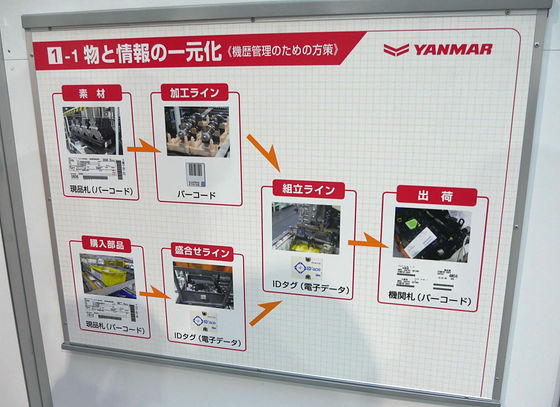
また、この多機種生産への対応が、自動組み立てラインでも実現されているというのも興味深いところ。先述のIDタグなどによる管理を取り入れることで、個別の仕様に応じた自動組立が行われているとのこと。このシステムの開発はヤンマーが独自に開発しているとのことで、ヤンマーと協力体制にあるトヨタがシステムの視察に訪れることもあるほどだそうです。
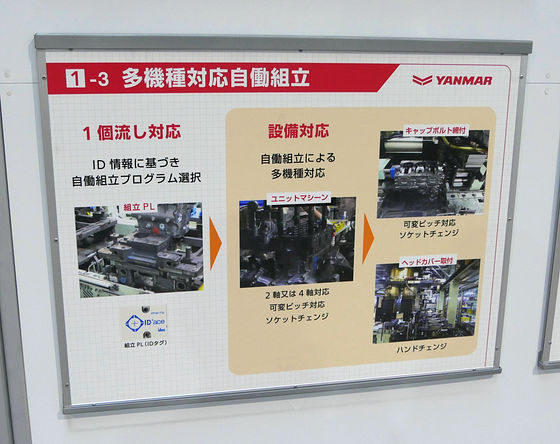
また、生産効率向上のためのカイゼン活動も活発に行われている模様。パネルには、各工程から挙げられた改善提案とその結果がビッシリと貼り出されています。ここでは生産に関する詳細な提案のほかにも、「風が当たりすぎるので空調の風向きを変えたい→改善され、作業を行いやすくなった」という小さな取り組みまでもが含まれており、生産現場で行われる小さなカイゼンが集まって、大きな効率アップが実現されていることを実感。
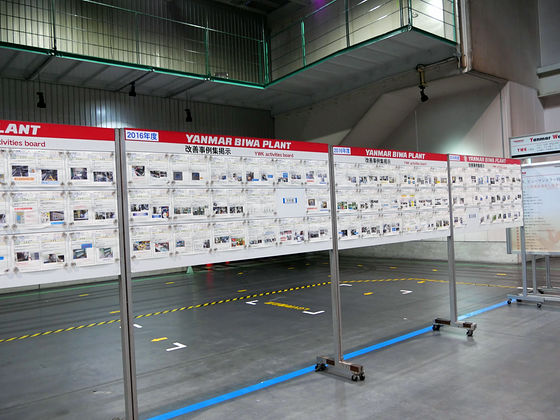
スタッフに必要な考え方や目標などがハッキリと「見える化」されています。
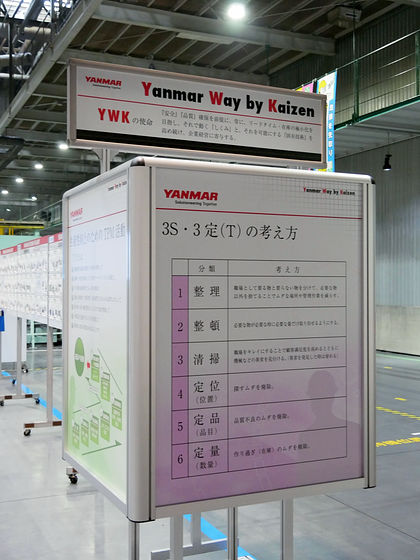
◆生産ラインに潜入
実際の生産ラインを見せてもらいました。まずは、エンジンの素材となるパーツを管理するための「素材ラック」。
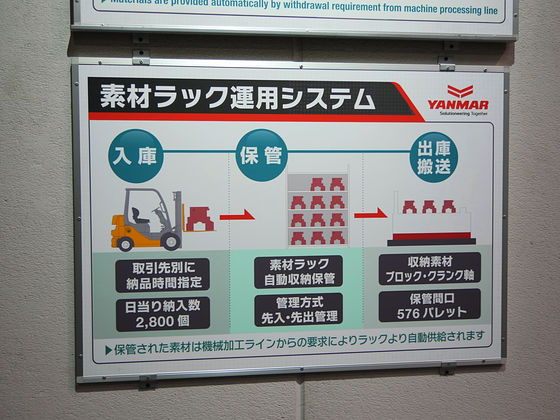
高さ10メートルはありそうなスペースには、サプライヤーから納入されたエンジンの部品を管理するための素材ラックが組まれています。
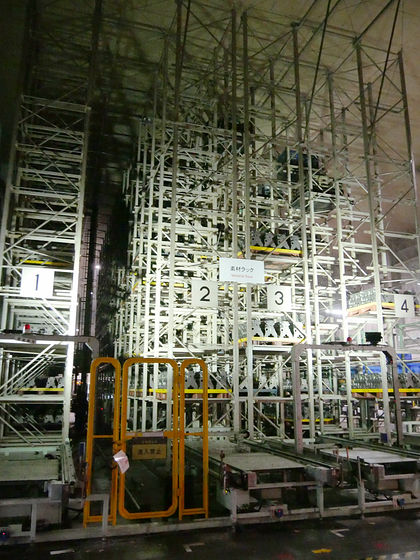
ここでの在庫管理やパーツの搬送は全て自動化・機械化されています。生産を管理するサーバからの指令を受けると、白く見えている素材ラックの隙間をリフトが動き、決められた棚から自動でパーツを取り出してきます。
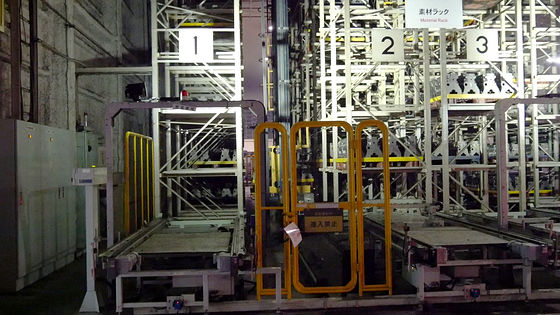
パレットごと棚から取り出してきたパーツは、手前にあるエリアに置かれ……
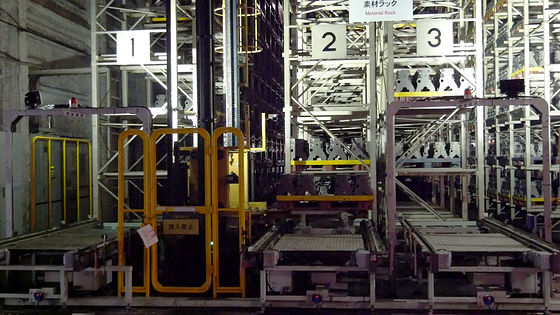
無人で動く搬送車「LGV(Laser Guided Vehicle)」へと乗せられます。LGVの動きもサーバによって管理されているとのこと。
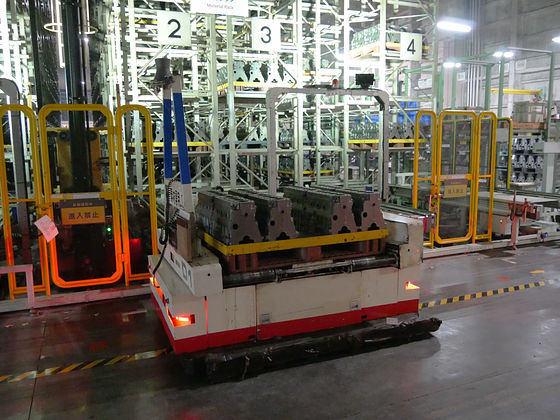
パーツを乗せたLGVは、「ルパン三世のテーマ」などの曲を奏でながら構内を走り回って必要なパーツを届けます。LGVの上部には回転式のレーザー装置が取り付けられており、工場内に取り付けられた専用のミラーからの反射で自車の位置を常に確認しているとのこと。Googleの自動運転車にも一部似たシステムが用いられていますが、ヤンマーではこのシステムを20年以上前に導入済みとのこと。
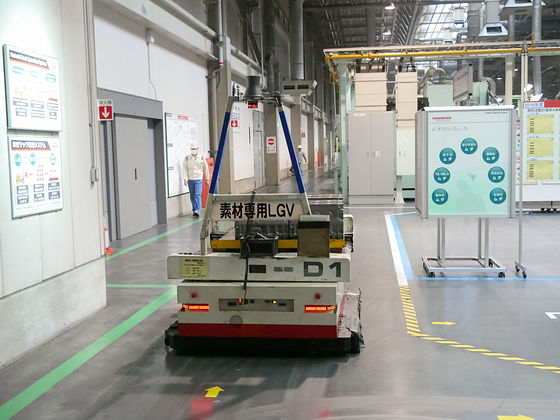
このようにして運ばれたパーツ「シリンダーブロック」が、加工ラインへと投入されます。
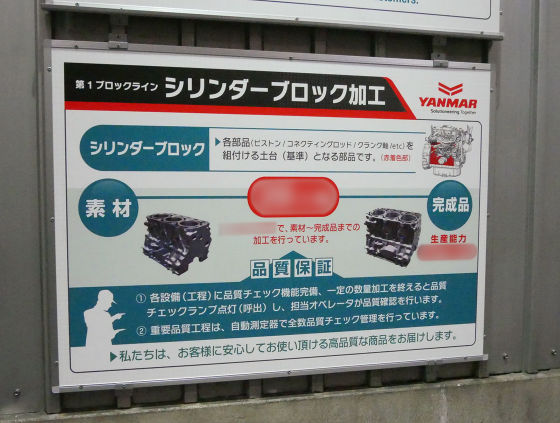
ズラッと並んだ加工機の数々。この加工機の中をパーツが搬送され、それぞれの機械で別々の加工が行われます。なお、ラインには片方から入ってもう一方に出るものと、ラインの端でUターンして最初の側に戻ってくる2つの種類がありますが、どちらの場合でも完成品が出てくる場所は、次の工程に備えて同じ側に揃えられているそうです。
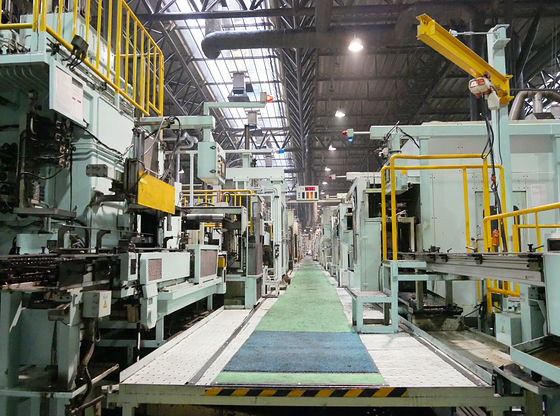
ラインの中ではロボットアームがせっせと動き、加工する素材を機械にセットアップ。ここでは金属を削る切削加工が主に行われていますが、あまり騒音は聞こえず、想像していたよりも静かな工場内でした。
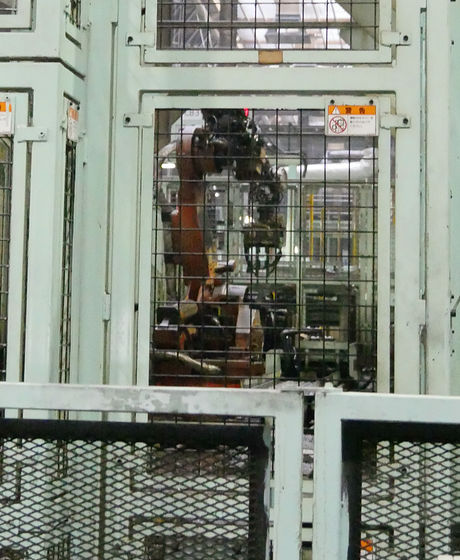
ずらりと並んだシリンダーブロックの完成品。このあと、組み立てラインに運ばれてエンジンの完成形になるのを待っているところ。
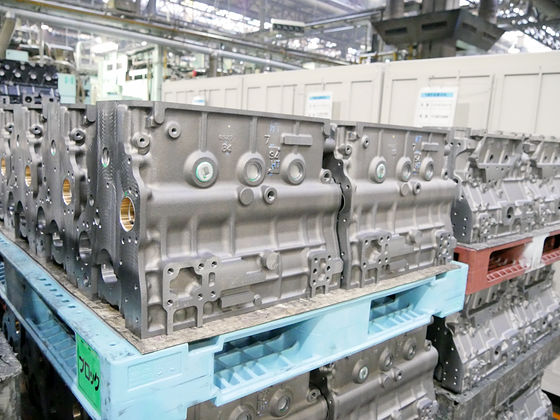
エンジンの回転を安定させる「フライホイル」も、シリンダーブロックと同じくサプライヤーからの納入を受けるパーツ。その受け入れ体制にも、生産効率を高めるための細かな工夫が取り入れられています。
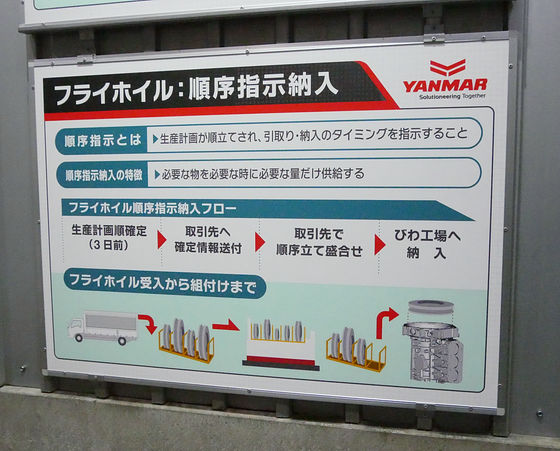
例えばこの光景。一見すると数々のフライホイルがカゴに並べられているだけに見えますが、実際にはこれらは全て工場の生産予定に沿ってあらかじめ並べられている状態。生産の数日前には工場からサプライヤーに生産計画が提示され、サプライヤーはその順序に沿ってフライホイルを並べた状態にして、びわ工場に納入するようになっています。これぞ、まさに日本が生みだした「カンバン方式」のなせる技で、生産に携わっている人には当たり前の光景ですが、実際の工場ではこのような細かな工夫がいくつも積み重ねられているというわけです。
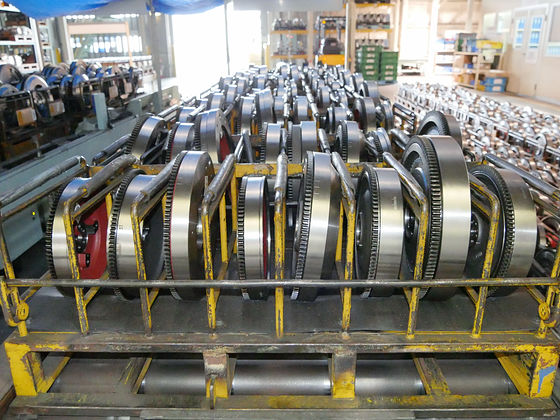
次はエンジン内部で使われる「コネクティングロッド(ロッド)」の加工を行うライン。ロボットが次々とロッドの素材を加工機にセットアップして加工が行われます。ここでも多くの工程が自動化されており、均一な品質で生産が行われるようになっています。
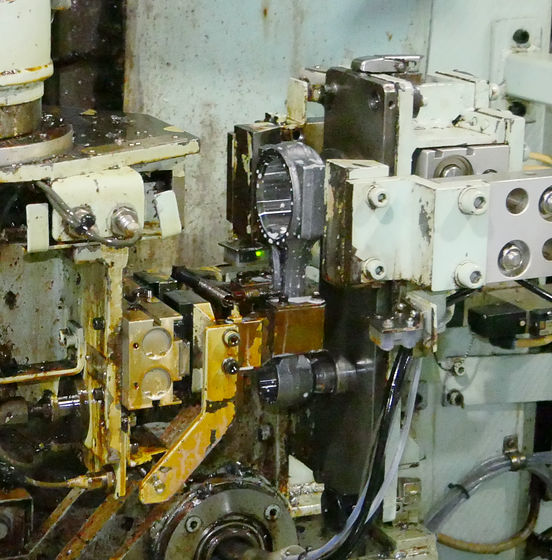
場内を歩いていると、先ほども登場したLGVがひっきりなしにパーツの運搬を行っています。レーザーによる自車位置の把握に加え、近接センサーによる人や障害物との接触を防止する装置も組み込まれていますが、かなり際どいところまで攻めて(近寄って)くるので最初は少しビックリしました。
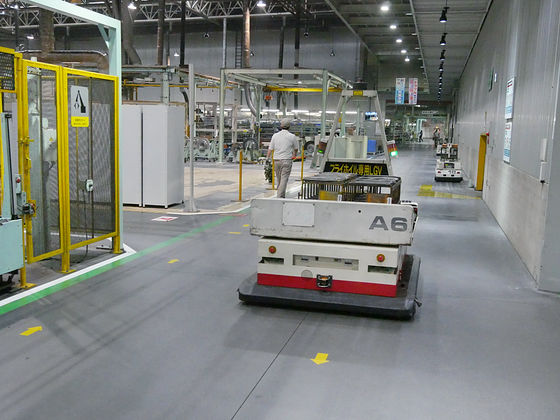
エンジンの主要部品以外の細かなパーツをサプライヤーから受け入れ、管理するためのラック。納入されたパーツは、まず向こう側にあるラックに在庫され、必要に応じて自動で手前のローラーに送られてくるようになっています。
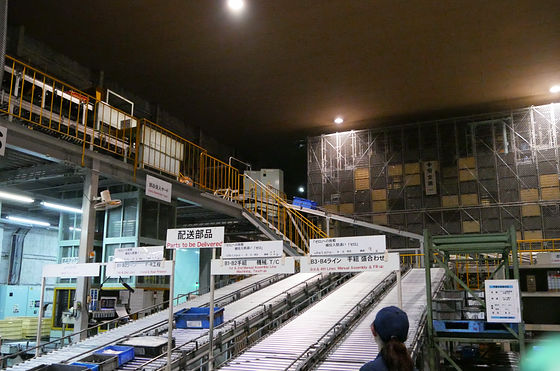
別の場所では、エンジンの仕様ごとに必要なパーツを集める「部品盛合せ」が行われています。ラインの中央には盛り合わせた部品を乗せて運ぶための搬送車がゆっくりと動いています。
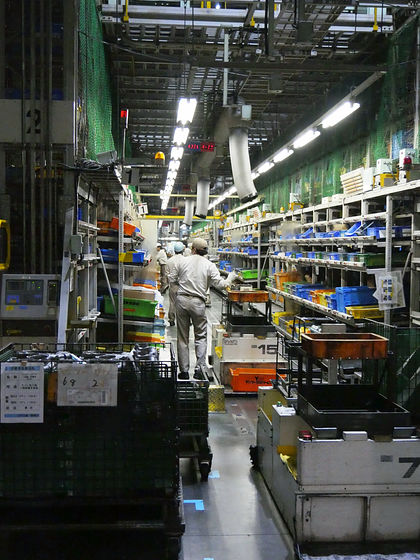
棚にギッシリと並べられたカゴには全て異なる部品が入っています。作業スタッフは、赤いランプが光るカゴから必要なパーツを取り出して、通路を流れる搬送車に載せていくようになっているのですが、その様子はさながらAmazonの巨大倉庫のよう。これも多品種を一括して製造する工場ならではの部品管理システムで、ランプで必要な部品を明確に示すことで、部品の取り間違いを防ぐシステムが取り入れられています。
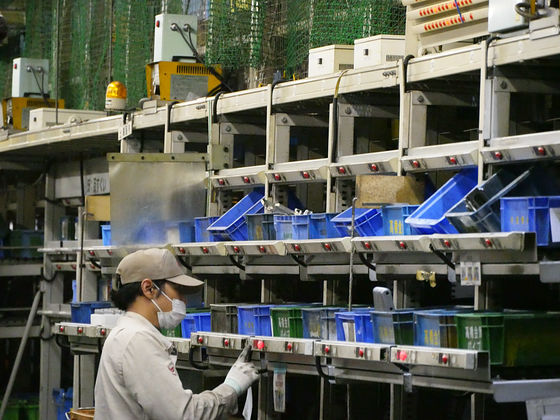
盛合せ用の部品が積み上げられているラック。膨大な種類の部品が使われており、確かにこれを全て人間が管理するのは難しいどころか、非効率の極みということになりそう。やはり、ロボットと人間がお互いに得意な仕事を担当することが、効率的で正確な生産には欠かせないようです。
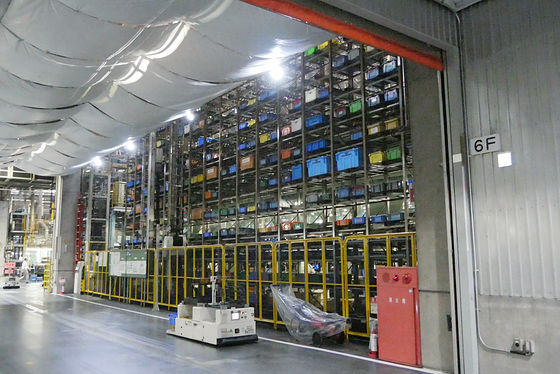
機械だらけの工場ですが、空きスペースにはこんな植物が置かれていたりも。プラントに置かれたプラント……。
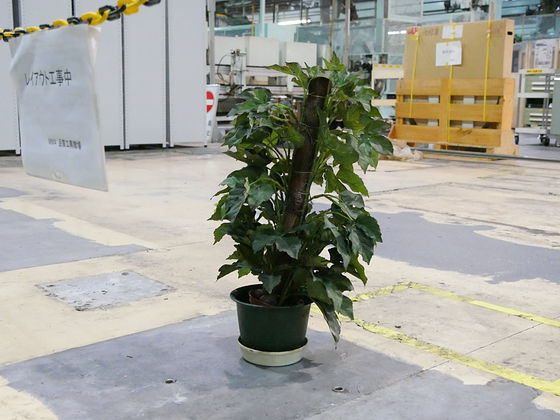
さて、こちらが実際のエンジン組み立てが自動で行われているライン。詳細は撮影できませんが、多くの機械が並び、その中でロボットアームが忙しく動いている様子がわかります。
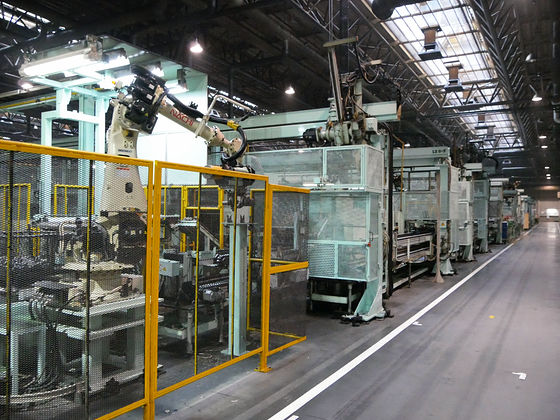
このラインでは、エンジンの性能を大きく左右する「バルブクリアランス」の調整が自動で行われています。現在でも専門の職人によって細かな調整を行うこともあるバルブクリアランスの調整ですが、ヤンマーのようにこれだけの機種を自動で行っているというのは、ほかでもあまり例がないとのこと。
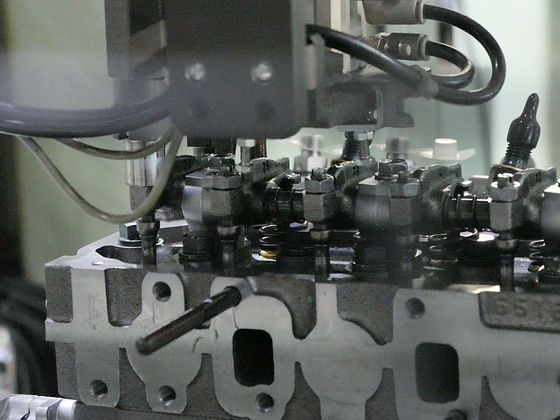
この自動化ラインで大きな役目を果たしているのが、IDタグによる部品管理システムです。エンジン本体ごとや、部品が載せられたカゴごとにタグ用のチップが装着され、固有のIDが割り当てられています。
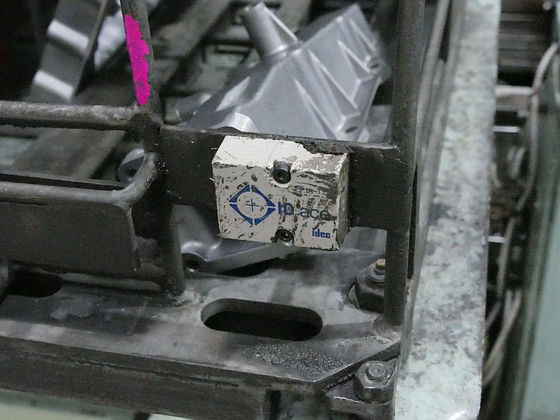
ラインには、そのチップを読み取るためのセンサーが無数に置かれています。このセンサーで生産管理を行うことで、機種に応じた加工・作業と、生産履歴の管理が行われています。
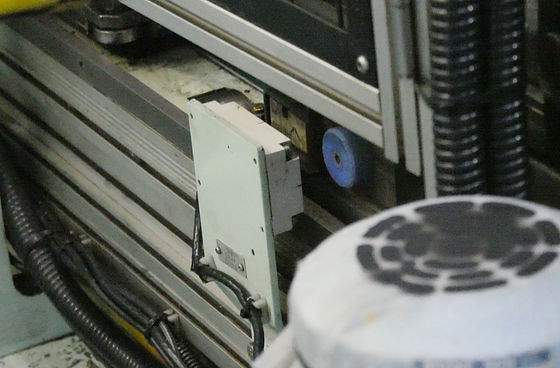
サプライヤーから納入されたフライホイルにも、識別用の2次元バーコードが貼り付けられていました。
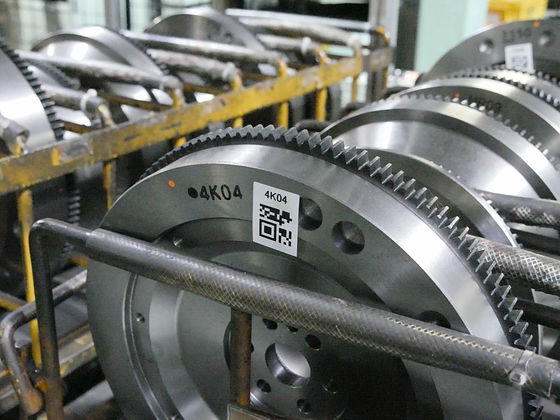
ヤンマーのびわ工場では、このような自動化システムの導入が高い次元で進められており、製造工程全体における自動化の比率は35%にも達するとのこと。これは、2000種類にも及ぶ仕様のエンジンが生産される工場ラインの数値としては非常に高いものになっているそうです。
このようにして自動で組み立てられるエンジンですが、人間の手で組み立てられる部分も残されています。
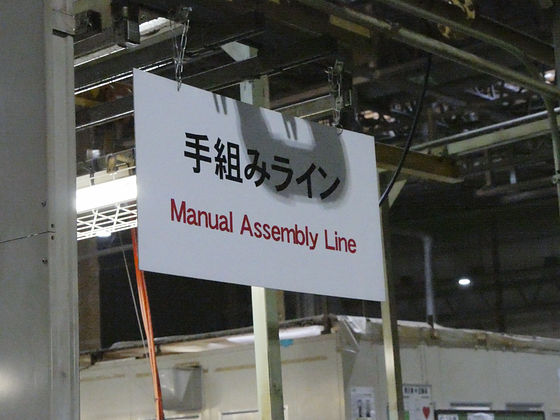
ゆっくりと流れるラインの上を、さまざまな種類のエンジンが流れています。
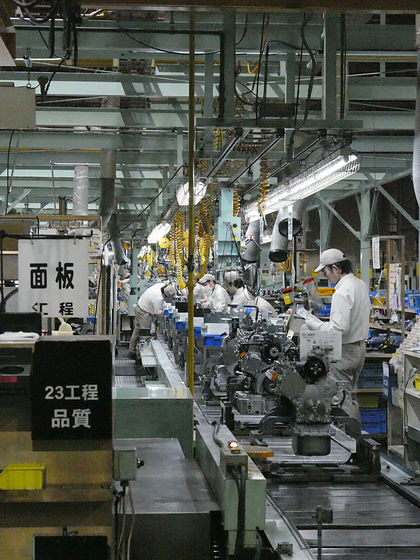
ここでも、さまざまな種類のエンジンがごちゃ混ぜで流されています。このラインは写真の右から左に流れているのですが、まずは部品を載せたカゴ、そして後に組み立て途中のエンジンという順番で流れて行きます。
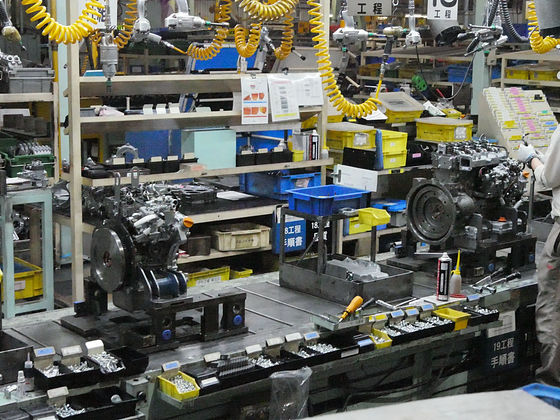
女性が組み立てを行っている様子も。
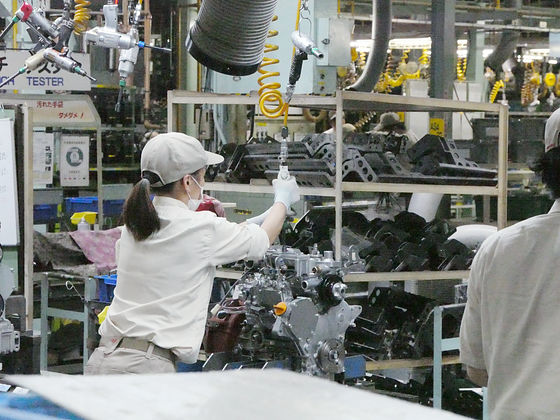
組み上げられたエンジンは全数が検査機にかけられ、1台あたり5分程度の性能チェックが行われます。
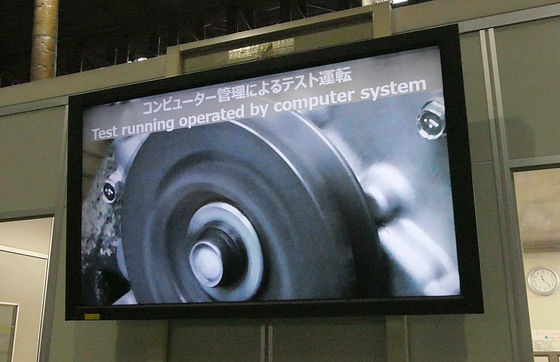
チェックが完了したエンジンは、出荷に向けた塗装やタッチアップ作業、そして最終チェックが行われます。
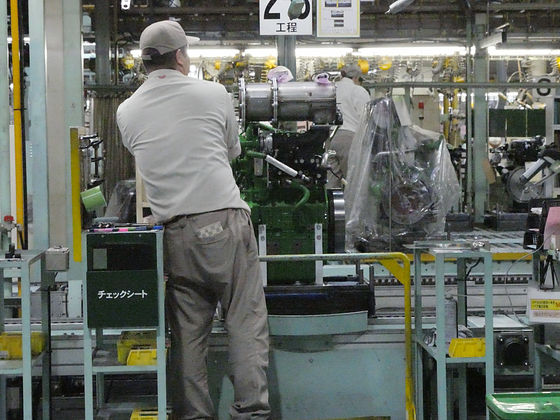
最終チェックを担当する女性スタッフの姿。この工場では約2000種類・常時800種類の仕様のエンジンが生産されており、1台ごとに違う仕様のエンジンをチェックしています。
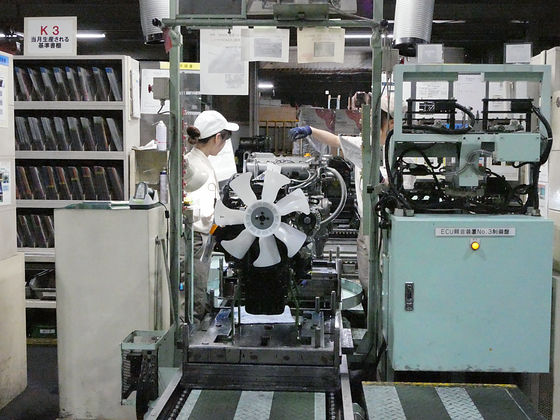
チェックが終わり、完成したエンジンがズラッと並べられたスペース。非常に大きなスペースに多くの製品が置かれていますが、ここにあるものは全て1週間以内に出荷されてしまうそうです。
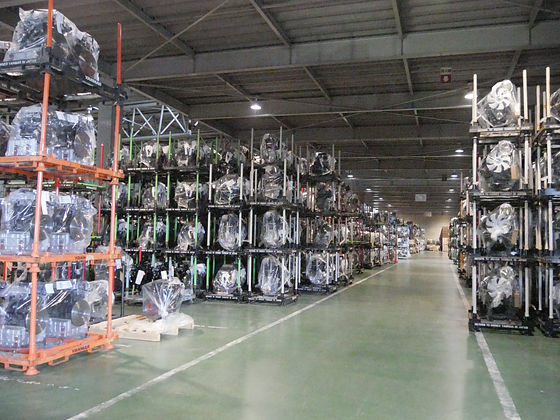
出荷スペースもこの広さ。海外向けに出荷するコンテナに製品を詰め込み、コンテナを封印する「バニング(バン詰め)」までを行える体制がとられているとのことでした。
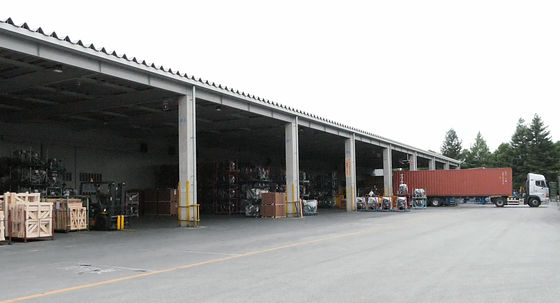
こんな様子で、ヤンマーのびわ工場では最新の設備による自動化ラインを使いながらディーゼルエンジンが組み立てられており、機械好き・工場好きにはたまらないものになっていました。聞くところによると、ヤンマーの産業エンジン事業はここ長浜市に拠点を置いて展開されているとのこと。長浜市はヤンマー創業者である山岡孫吉氏の生誕の地であり、いわば文字どおり「ヤンマーが生まれた場所」とも言えるわけで、地元に還元したいということからこの地に拠点が置かれるようになったそうです。
・関連記事
トラクターや建機、ボートに屋上のメダカなど多くの体験ができる「ヤンマーミュージアム」に行ってきました - GIGAZINE
豚肉禁止のみにあらず、食器の使い分けや調理時間帯まで徹底した「ムスリムフレンドリー」な社員食堂がヤンマー本社で始まったので行ってみました - GIGAZINE
天気予報でおなじみのヤン坊マー坊が生誕50周年、オフィシャルブックを出版へ - GIGAZINE
・関連コンテンツ
in 取材, ハードウェア, 乗り物, Posted by darkhorse_log
You can read the machine translated English article I saw the inside of Yanmar's mother fact….