VAIOのモンスターPC製造現場を徹底取材して見えてきたMADE IN JAPANのすさまじいものづくりとは?
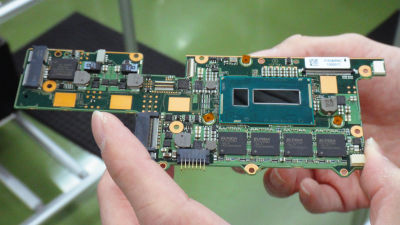
ソニーから独立して「小さなPCメーカー」になったVAIO株式会社が「モンスター」と称する2種類の高性能PCを発表して新生VAIOの方向性を明らかにしました。そこで、モンスターPCの秘密を探るべく、VAIO株式会社の総本山である長野県の安曇野(あずみの)工場を訪問して製造現場を取材すると、スペックシートからは見えてこない徹底したこだわりだらけの「MADE IN AZUMINO JAPAN」のものづくりが実践されていました。
VAIO | クオリティ | 安曇野FINISH
http://vaio.com/quality/azumino_finish/
長野県安曇野市にあるVAIO株式会社の本社に到着。
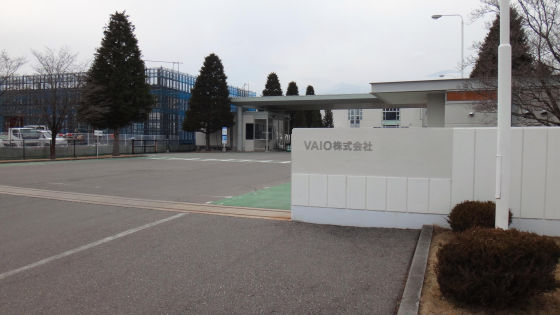
正門前には「VAIOの里」のモニュメント。
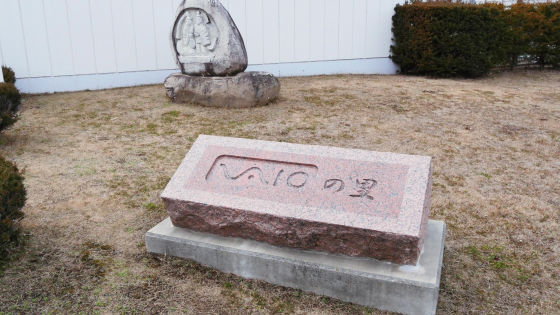
建物には「VAIO」のロゴ。
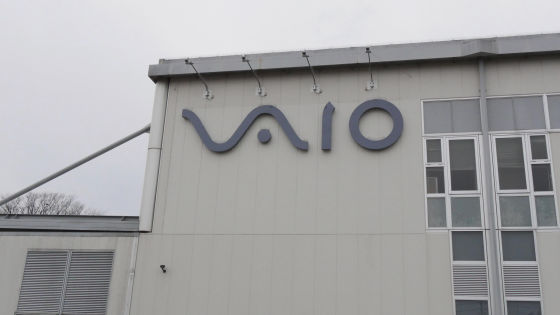
その後ろには日本アルプス。自然豊かな環境の中、モンスターPC「VAIO Z」は製造されています。
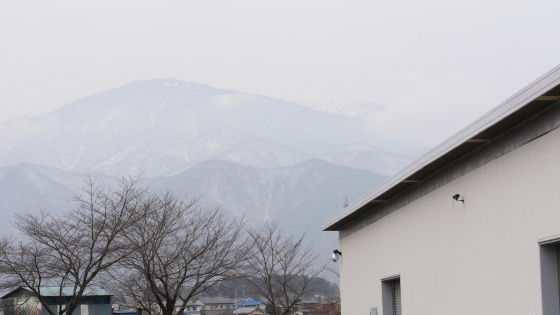
さっそく潜入開始。
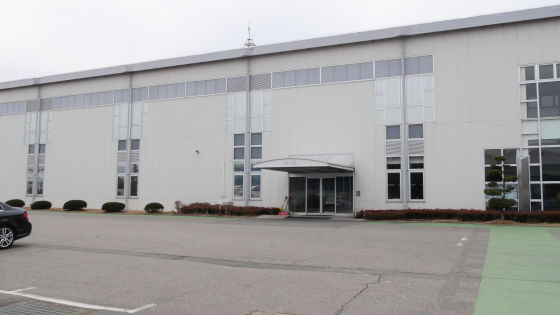
ロビーの横には……
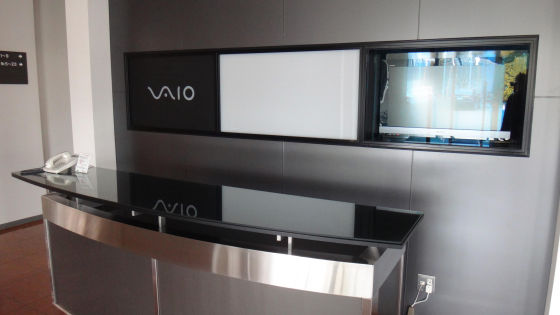
展示コーナー。
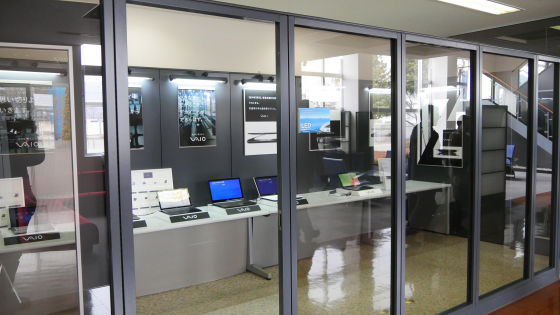
VAIOの現行モデルがずらりと展示されていました。
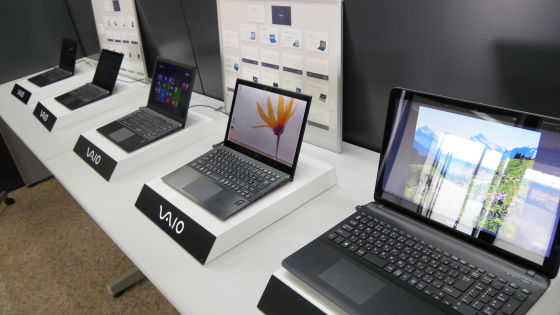
力強いポスター。
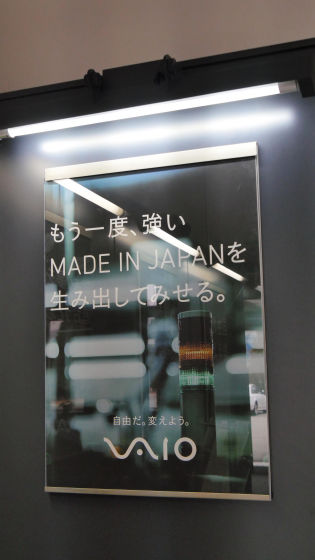
今日は、このやりすぎてしまったモデル「VAIO Z」の製造現場をチェックします。
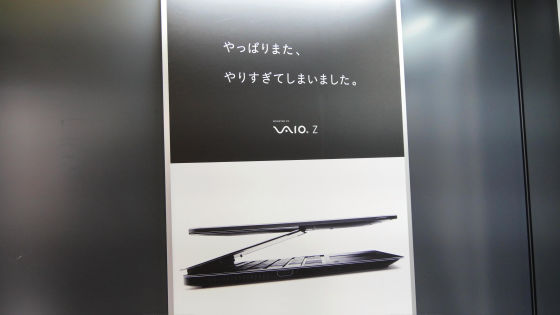
工場見学の前に、着替えていざ出陣。
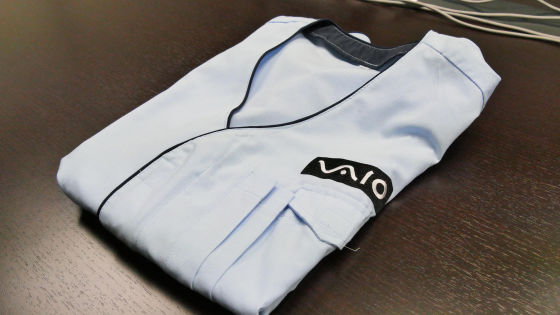
まず最初に通るのはエアシャワー。
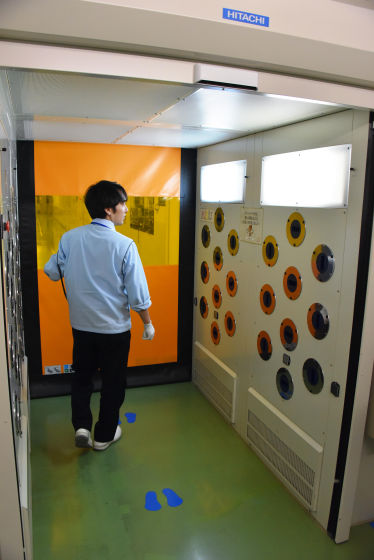
製造現場ではゴミは厳禁。こうしてエアシャワーでほこりなどを落とすことが必要です。
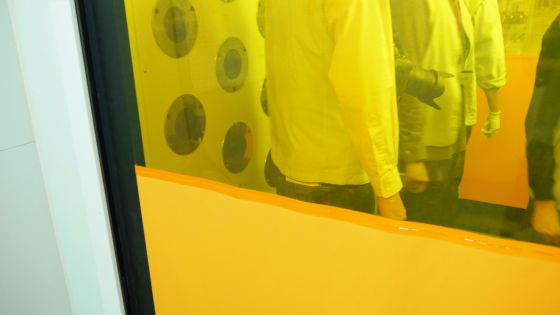
また、製造ラインに足を踏み入れる前に、静電気を除去することが冬場は特に大切。
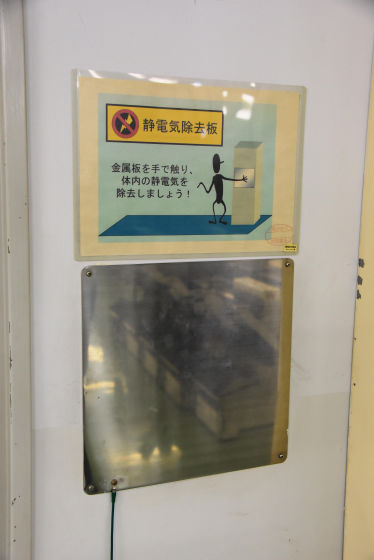
「いらっしゃいませ GIGAZINE様」となかなか心憎い表示。
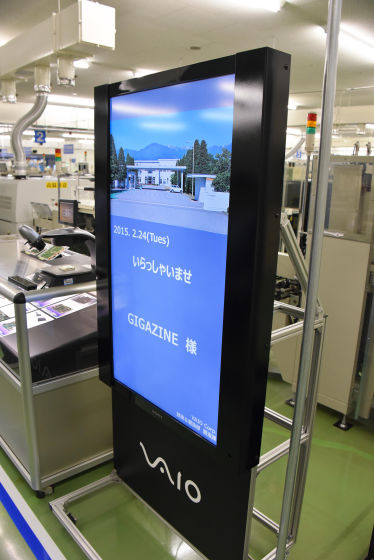
まずはメイン基板(マザーボード)に各種部品を載せていく「実装」ラインから。歴代VAIOのマザーボードが展示されたケースの上に顕微鏡のようなマシン。
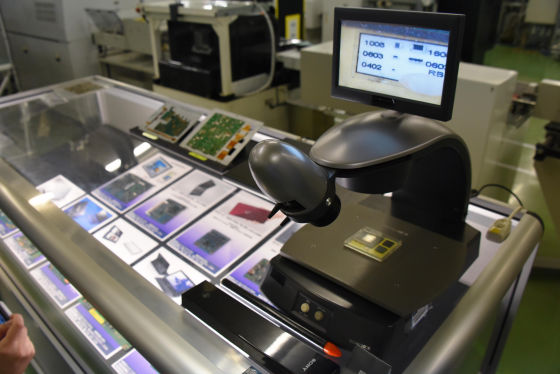
カメラで写しているのはこのケース内のパーツ。
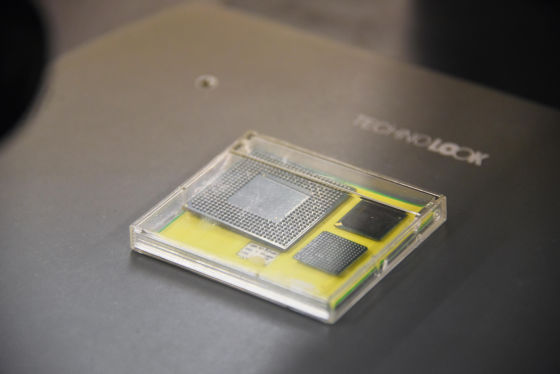
これはVAIO Zで採用している「0603」、つまり、0.6mm×0.3mmの部品のサイズを示すデモンストレーション。ディスプレイに映る米粒の大きさと比較すると、0603部品の小ささが分かります。なお、「0402」は0.4mm×0.2mmサイズのさらに小さな部品で、VAIO安曇野工場には0402のはんだ付けを修正できる「匠」がいるそうです。
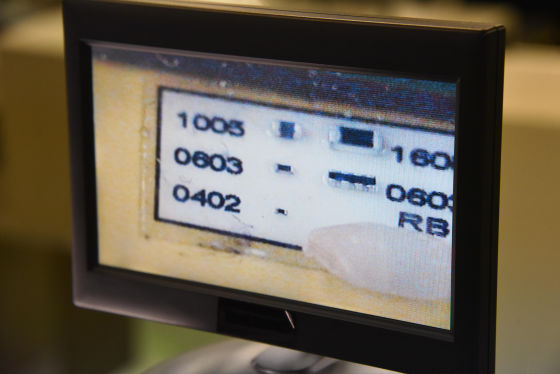
マザーボードは金属キャリアに載せて部品の実装作業を行います。キャリアあたり2枚のマザーボードで、表面・裏面でマスキングの形状が異なります。基板にはいつ製造したのか分かるように2次元バーコードをレーザー刻印することで、品質管理に役立てているとのこと。
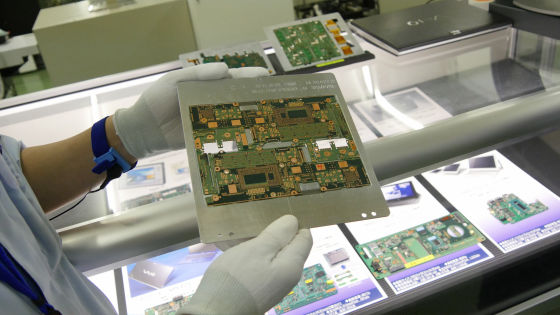
これはマザーボードにクリームはんだを印刷する機械の「はんだ印刷機」。なお、はんだが適切な場所・適当な量で印刷されているかどうかは直後の「はんだ印刷検査機」で全自動チェックしています。
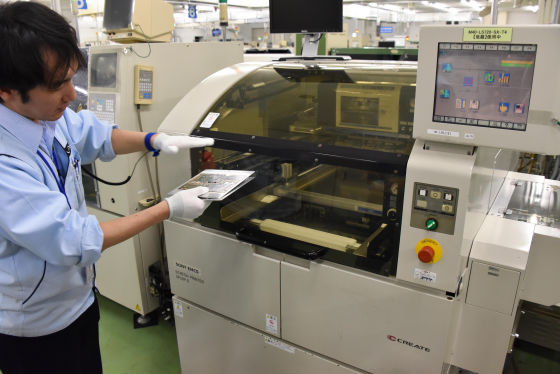
はんだ印刷の次の工程は「モジュラー型高速装着機」での部品の実装。極小部品0603を装着するマシンです。
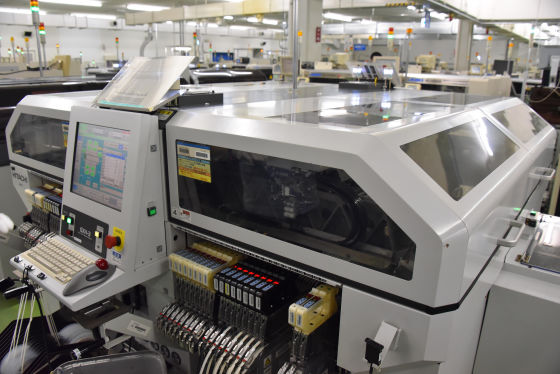
このテープ上の0603を巻き取りつつ実装していきます。
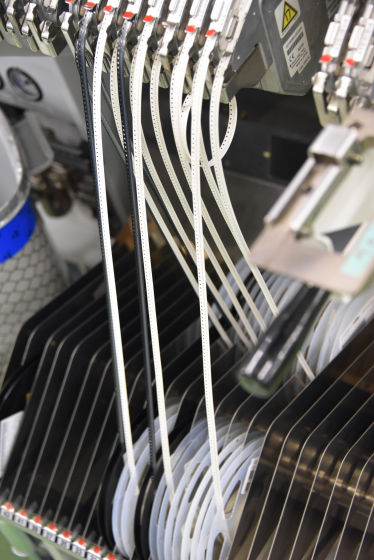
なお、テープの丸い穴の横にあるゴミのような「点」が0603。モジュラー型高速装着機はこの小さな部品を最大で0.03秒で1個置く能力をもつとのこと。
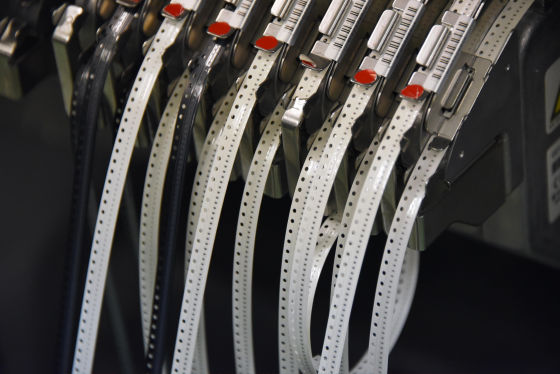
装置は2つの通路にまたがるくらいの巨大サイズ。マザーボードが機械の中を往復しつつ、両サイドで部品を実装します。
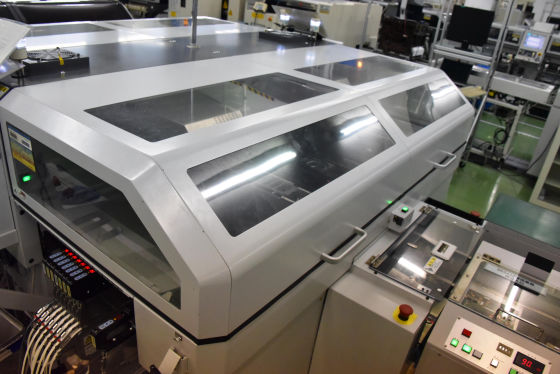
操作はキーボードとトラックボールで行う模様。
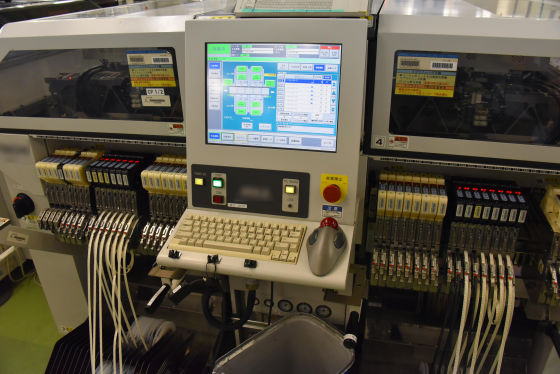
これはコネクタ類を実装する「多機能装着機」という機械。なお、一部の強度の必要な部分は、はんだに加えてボンドで補強するとのこと。
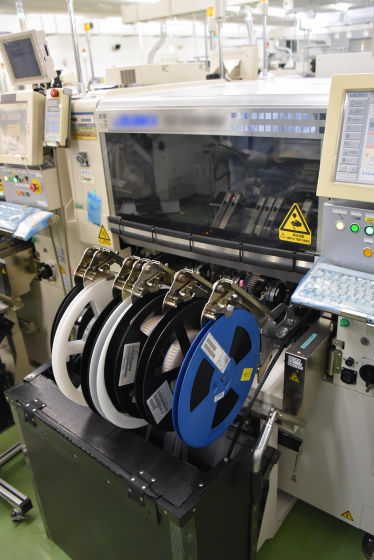
部品は0603に比べると大きめ。
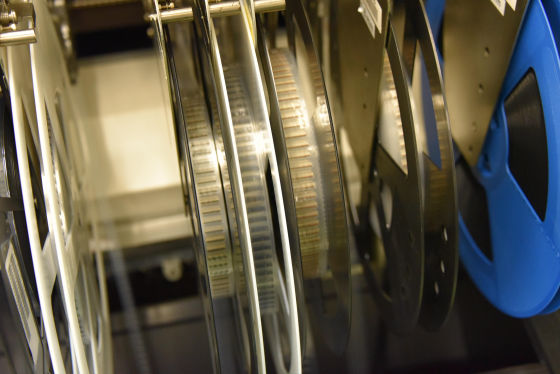
その後、CPUなども実装。
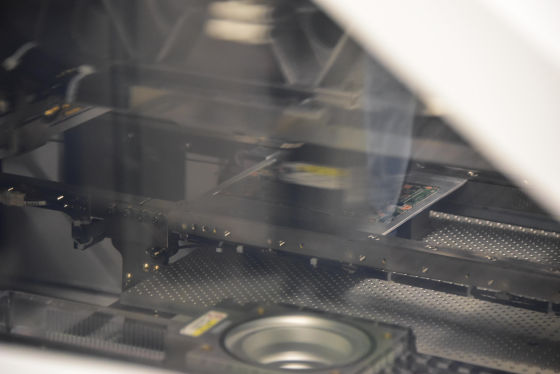
載せた部品が正しい位置に置かれているかどうかのチェックを、基板を乾燥させる前にもう一度行います。なお、正確さの基準となるのは「神の手を持つ」と言われる匠の配置例とのこと。
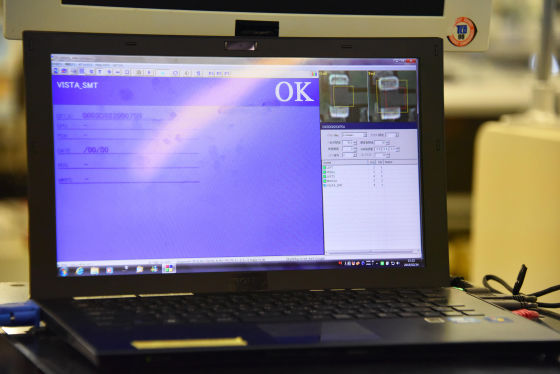
次に、実装した部品を完全にくっつけるための「リフロー炉」を通過させる工程。200度を超える高温の炉の中を基板がゆっくり通過することでフラックスが飛び、最後に冷却してはんだを固めます。
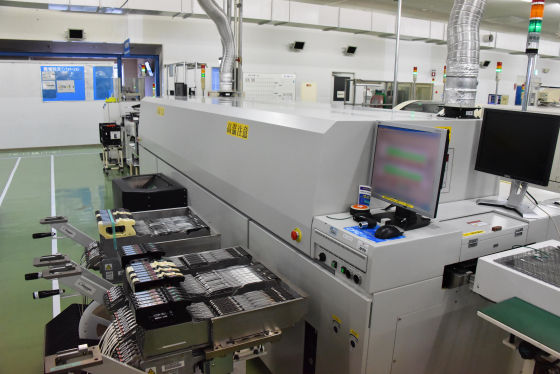
なお、CPU用のリフロー炉は5メートルはあろうかという箱の中を窒素で充填して酸化を防ぐとのこと。
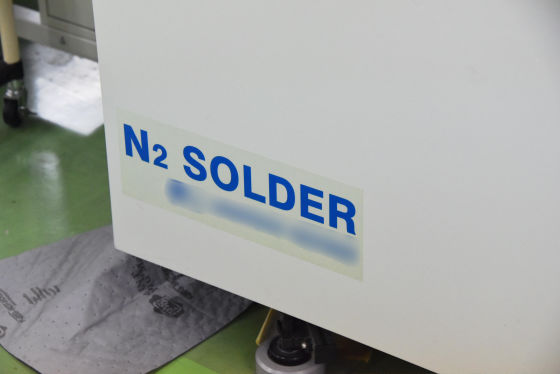
基板がリフロー炉から出てきました。
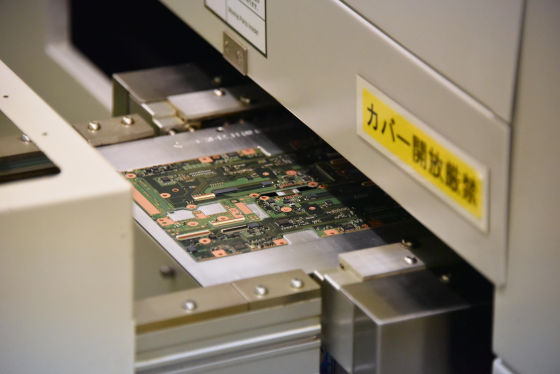
さらに部品のマッチング検査。ディスプレイ右上の黄色い枠が検査中のパーツ。
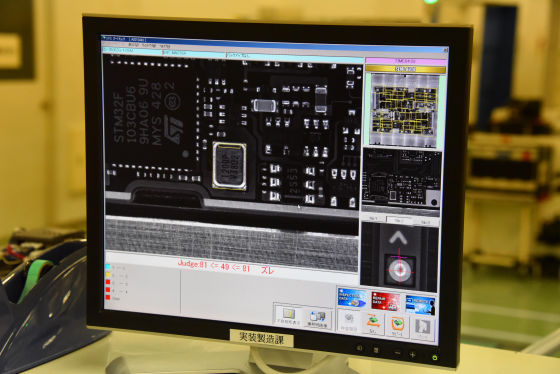
コネクタまですべて自動で検査。
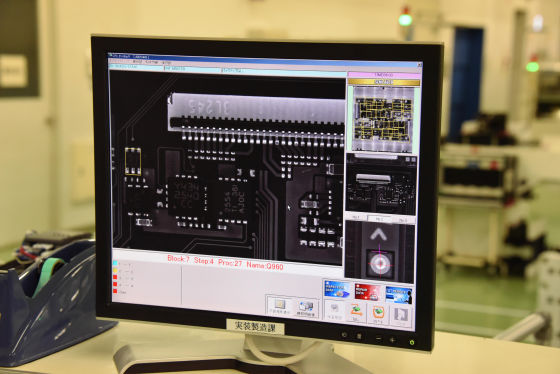
なお、機械検査の後には人間によるチェックが行われ、何重もの検査を行うことで高い品質を維持しているとのこと。

数々の検査に合格した基板は、専用トレーに載せて次のアッセンブリ工程へ搬送されます。なお、マザーボードは受注当日にオーダーに応じて部品を実装するというオーダーメード方式だそうです。
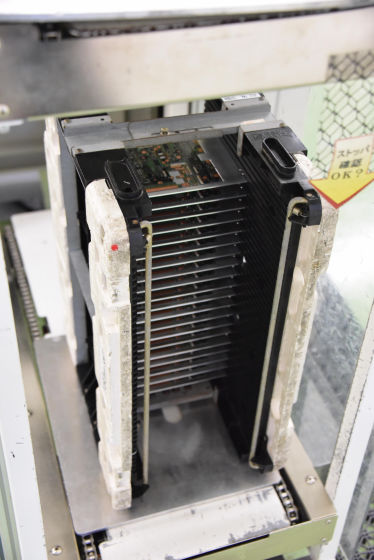
そしてフロアが変わってマザーボード以外の外装やキーボードなどを製造して組み合わせるアッセンブリ工程。これはキーボードまわりのフレームパーツ。
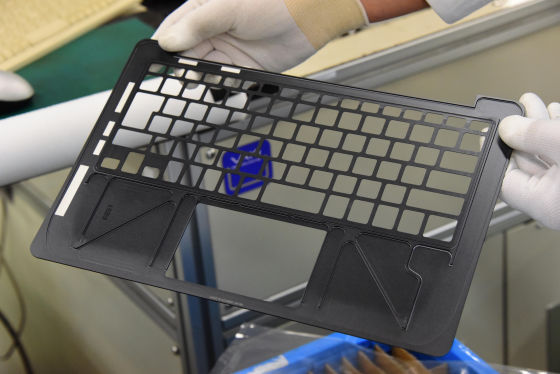
よく見ると「MADE IN AZUMINO JAPAN」のレーザー刻印が施されています。
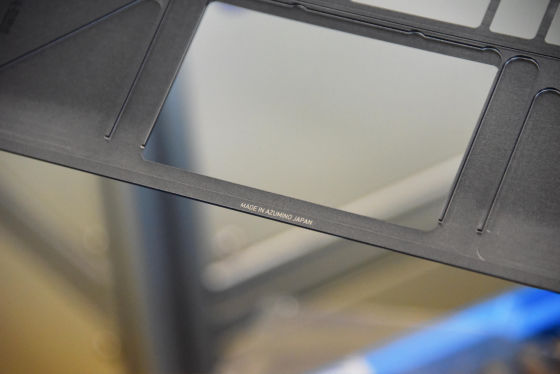
レーザー加工はこの機械で行います。
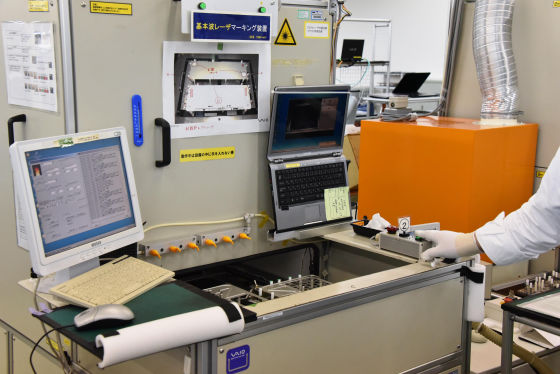
パーツを中に入れてレーザーを照射。
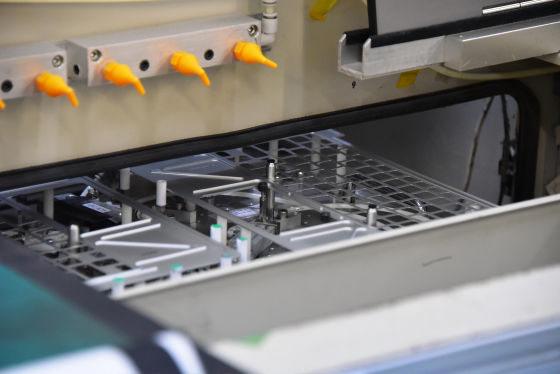
内部はカメラで確認可能。この緑色のレーザーは……
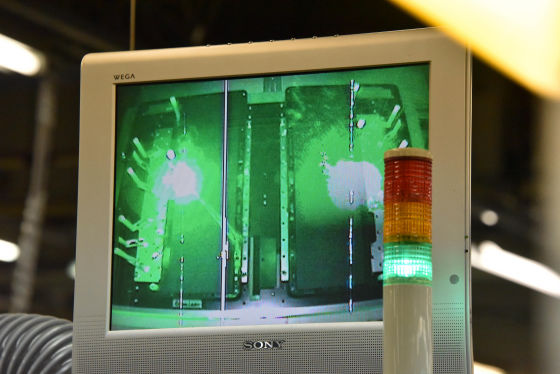
こんな小さな表記も刻印可能。印刷とはひと味違う質感と耐久性を実現しているというわけです。
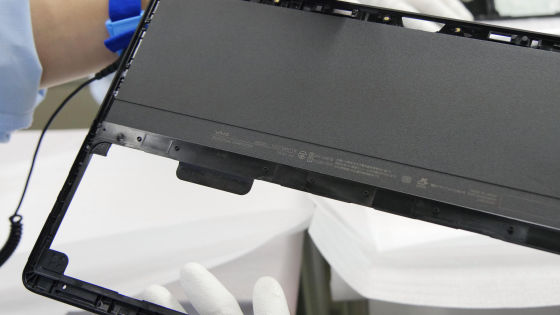
パームレストなどの「接着」技術も安曇野クオリティ。
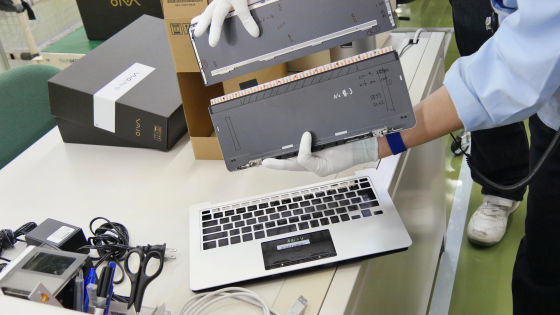
VAIO Zでは「剛性感」を非常に大切にしているとのこと。同じ部品(素材)を両面テープと接着剤を使って貼り合わせて比べてみると、触ったときの剛性感は雲泥の差。接着剤を使うVAIO Zの工法は強い力をかけてもほとんどたわみません。剛性感の圧倒的な差は、手に取って比べると一発で分かるレベル。

キーボードまわりのアルミフレームにもこの接着技術が採用されています。当然、両面テープではなく接着剤を使うことで圧倒的な「薄さ」も実現できるというわけです。
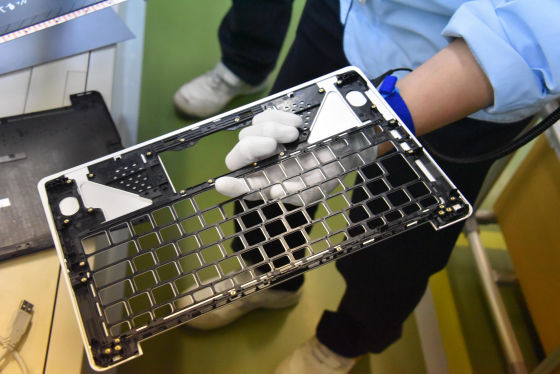
接着剤をどこにどれだけ使えば高い剛性感を出せるのか、というのはノウハウの塊。もちろん部品ごとに最適な場所・量は変わります。
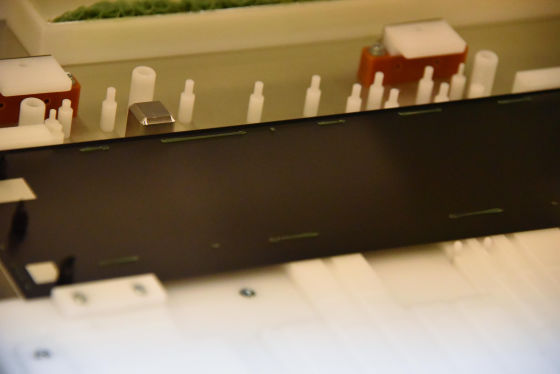
適切な量を正確な場所に塗り塗り。なお、このパーツの接着剤がいつ塗られたものなのかもすべてバーコードで管理されているとのこと。
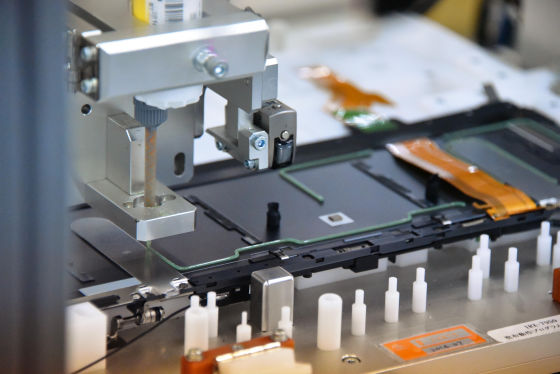
その後、部品同士を貼り合わせます。接着剤の塗布から部品同士を貼り合わせるまでの時間管理も徹底しているそうです。これはキーボード周りのフレームパーツ。キーボードやタッチパッドの穴同士を、ぴったりと貼り合わせる必要があり、この精度がキーボードの打鍵感にも影響するため、非常に高い接着精度が求められます。
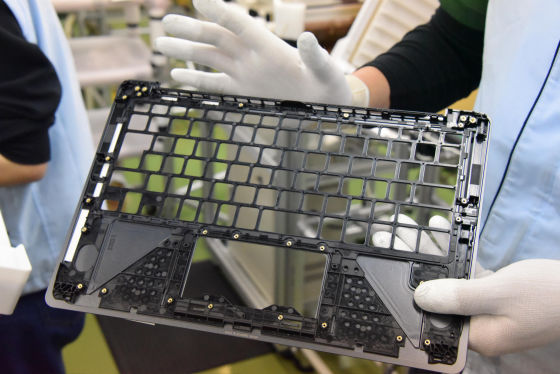
さらにプレスして接着剤を固めます。
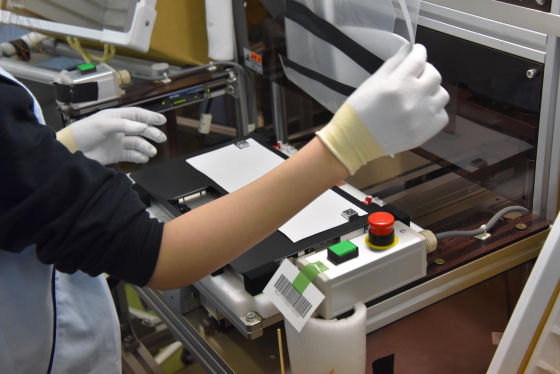
接着剤が固まるまでは両面テープでサポート。
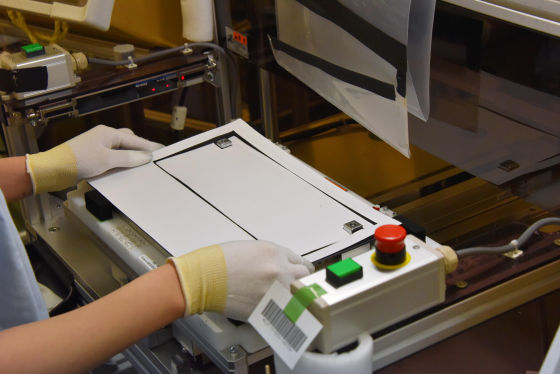
こんな専用治具を用いてパーツ同士を押しつけます。
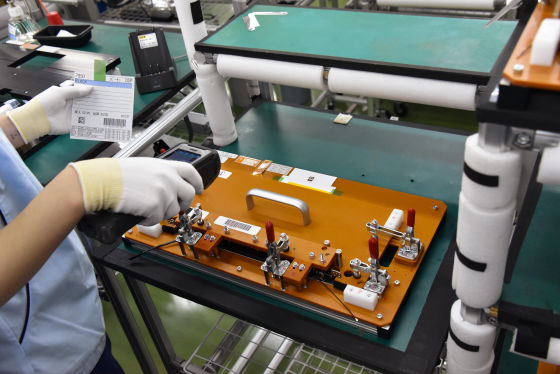
固定は手作業。ここでの固定方法が品質を大きく左右するので高い技術が要求されるとのこと。
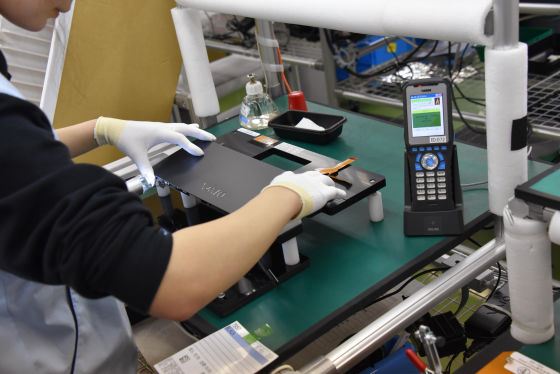
さらに目視できない接着面は、横からカメラで撮影してチェック。狙いは「隙間ゼロ」
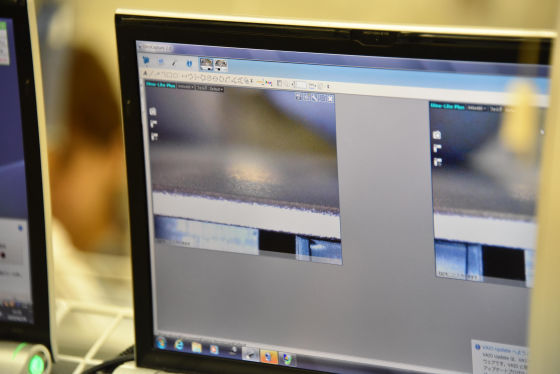
なお、写真の黒い「ツメ」のかかり量はわずか0.4mmしかないとのこと。パーツの接着精度がどれくらいシビアなのかがうかがい知れます。
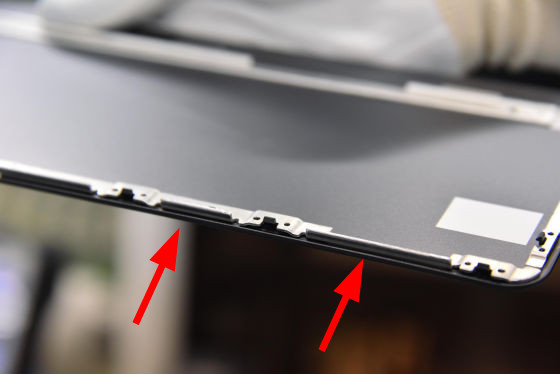
これは15時間以上の連続駆動時間を実現するVAIO Zのキモとなるバッテリー。
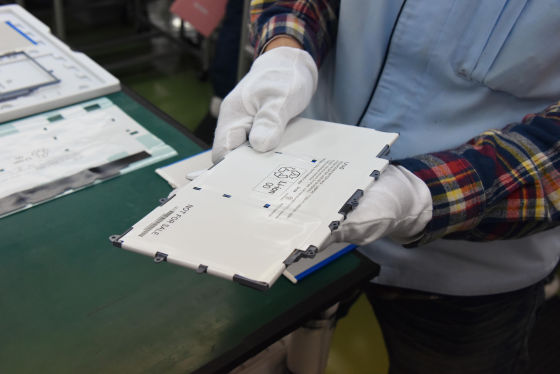
既製品を買ってきて装着するというわけではなく、安曇野工場ではバッテリーも内製。写真の3つのパーツがバッテリーセル。なお、薄さ追求のために一般的なバッテリーと違ってケースはありません。
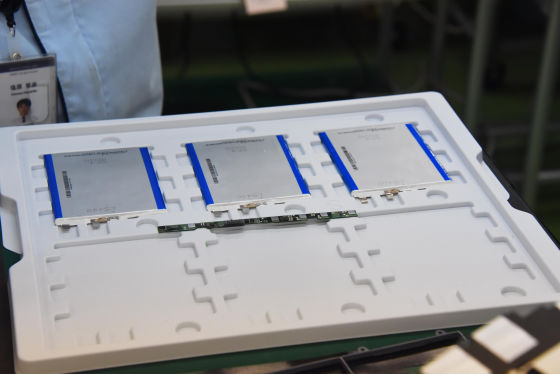
吸引ポンプ付きの専用治具で3つのセルを一気に移動させます。
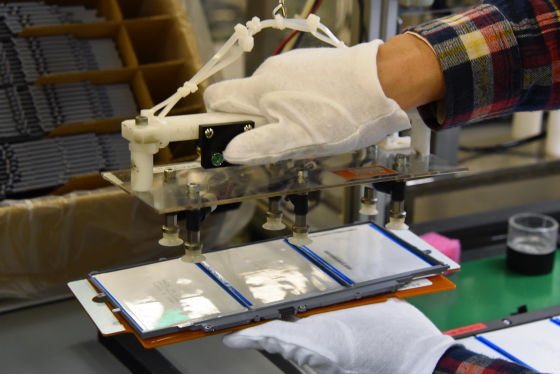
ブロアーでゴミを吹き飛ばして……
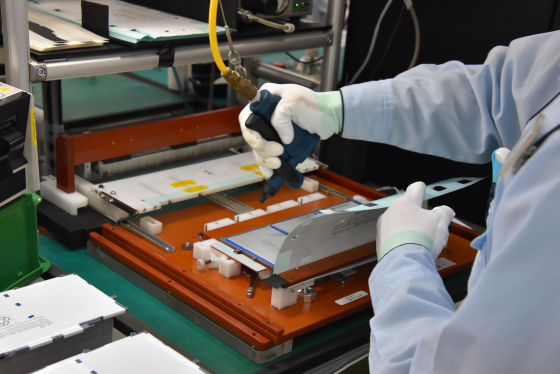
ケースの代わりを務める外装シールの貼り合わせ。
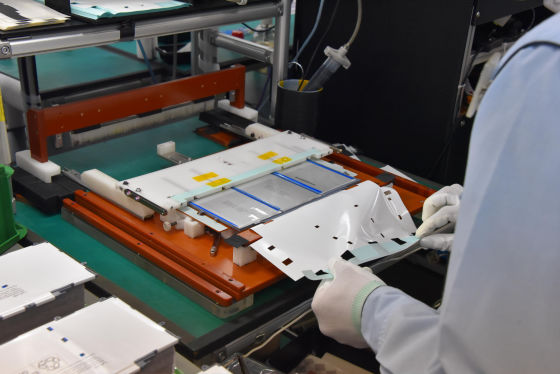
見ている方が緊張するような作業……。
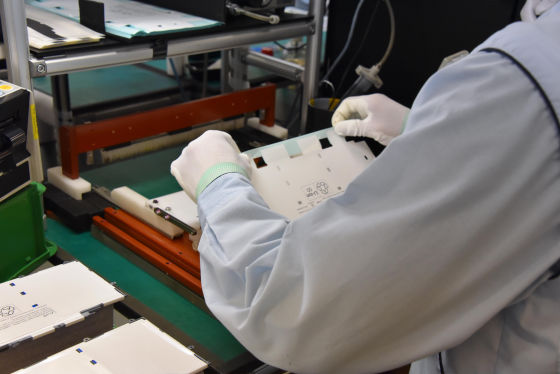
当然のように一発で決めました。
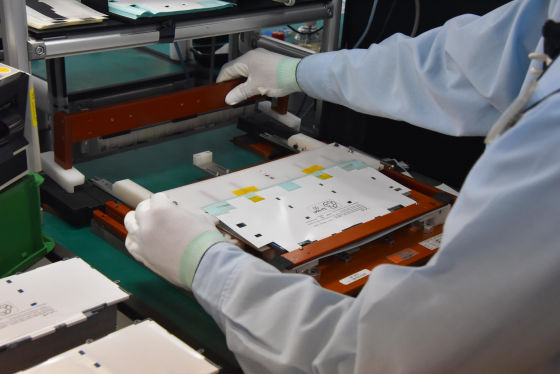
最後にシールを外からしっかり押しつけて完了。しわや気泡があると極限の薄さを実現できないとのこと。
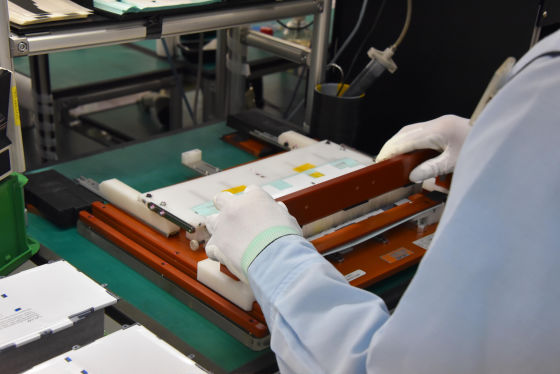
こんな風にして、VAIO Zの特徴的な薄型大容量バッテリーは手作業で製造されていました。
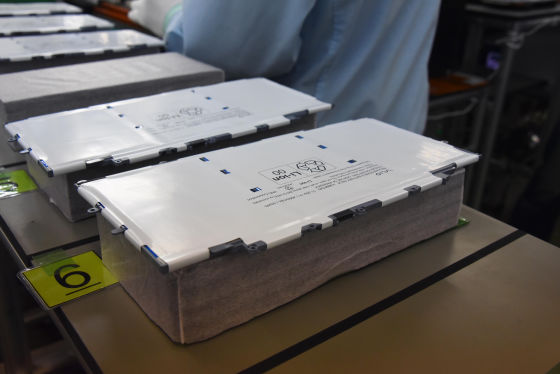
この部品はVAIO Zのタッチパッドで、フェイスシート(表面材)の下には雲母片岩(マイカ)という部品。たわみのない固い表面を追求した結果、1mm厚のマイカが採用されているとのこと。
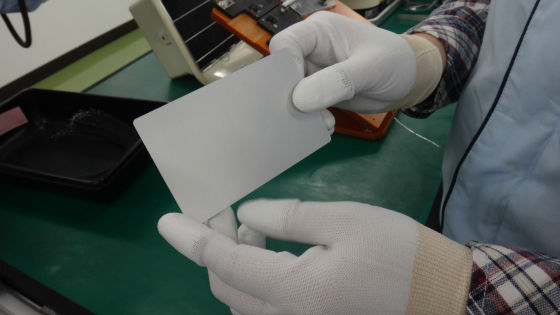
裏面はモジュール。フェイスシート・マイカ・モジュールの3枚を正確に貼り合わせています。
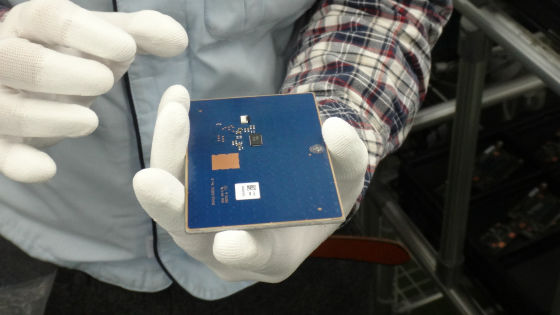
当然、貼り合わせ精度はクリック感に直結するため、専用治具で正確な貼り合わせ作業が不可欠。
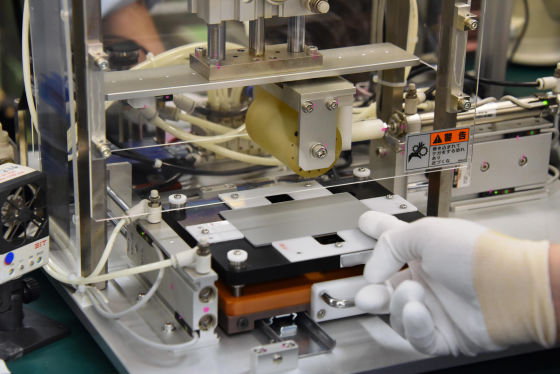
キーボードへの取りつけ作業。
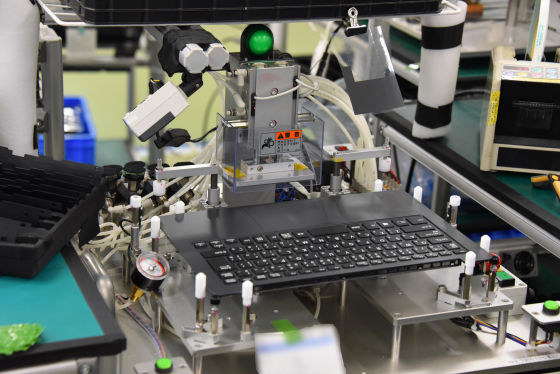
なんと管理ツールにはPSPを利用。
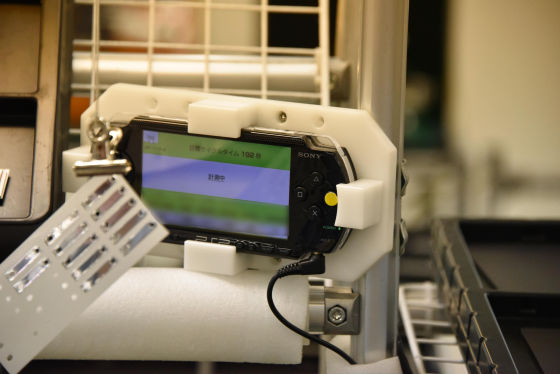
真上から正確に押しつけるように組み込みます。
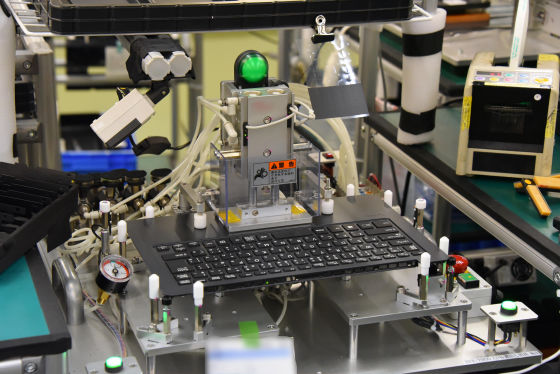
無事、取り付け完了。
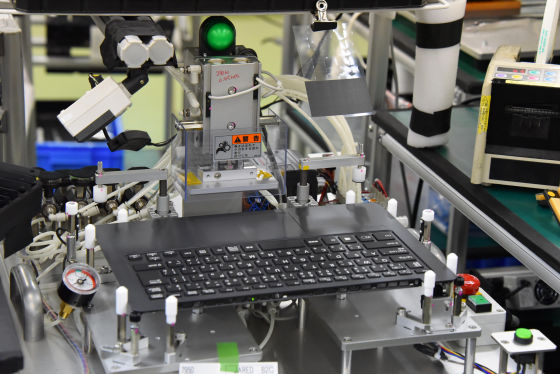
基板の検査は組み込み前にも行われます。
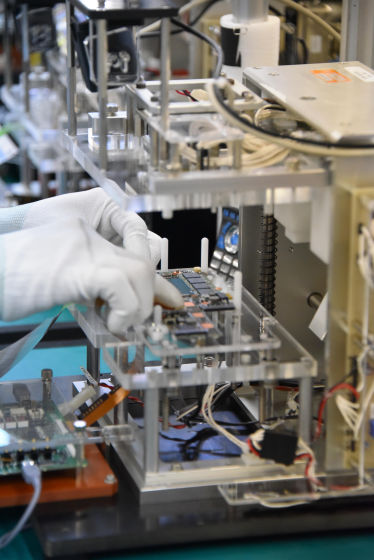
仮にUSB端子に供給される電圧が想定の数値より上下に振れている場合でも、デバイスそのものは機能します。しかし、電圧のわずかな高低によりバッテリー駆動時間が減ったり、デバイスの認識不良が起こったりといった不具合が生じ得るとのこと。そのため、VAIO Zの製造工程では、基板のすべてのポートの電圧を一つ一つチェックして合格したものだけが、次の組み込み工程に進められるというルールが適用されています。単に使用できる状態というのでは不十分で、最大限の性能を引き出せることがVAIO Zの基板には求められるというわけです。
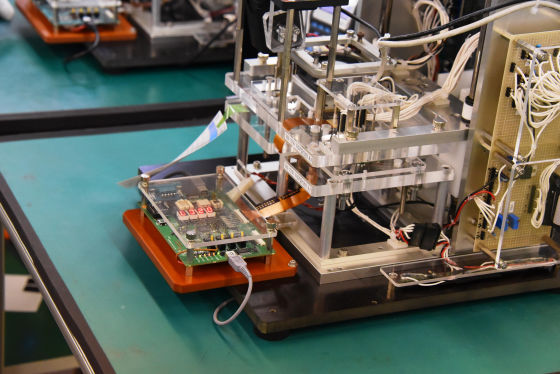
これは、フジクラと共同開発のヒートパイプ。VAIO Zは独自の冷却システム「Z ENGINE」によって、極薄筐体に収められたCore i7+Iris Graphics 6100という高性能CPUとGPUを冷却します。
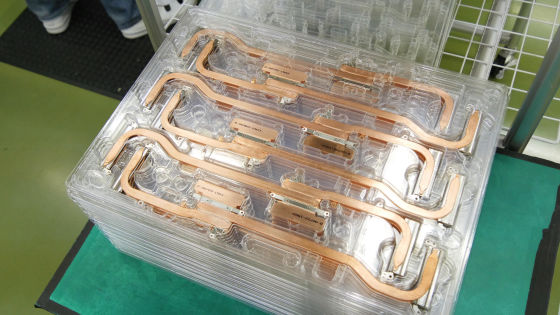
CPUとヒートパイプの間に塗る熱伝導グリスも、適切な場所に適当な厚みで正確に塗ることで冷却性能を最大限に引き出すことが可能。そのためグリスを塗る専用治具も用意されています。
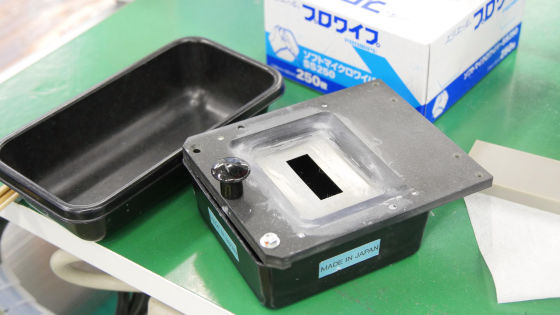
治具をはめてグリスをささっと塗り塗り。
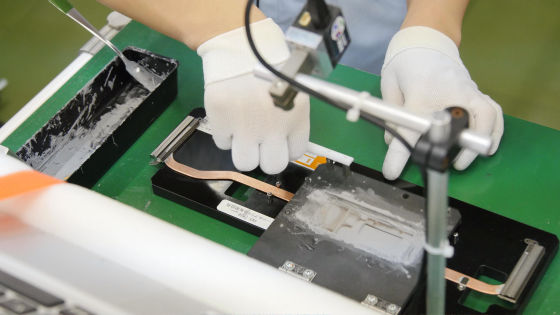
治具を取り外すとCPUダイの形に正確な量のグリスが塗りつけられました。従来の機種ではサーマルシートを使用していたものの、厳しい放熱性能基準を満たしつつ厚みを極限まで抑えるためにVAIO Zではグリスが採用されたとのこと。
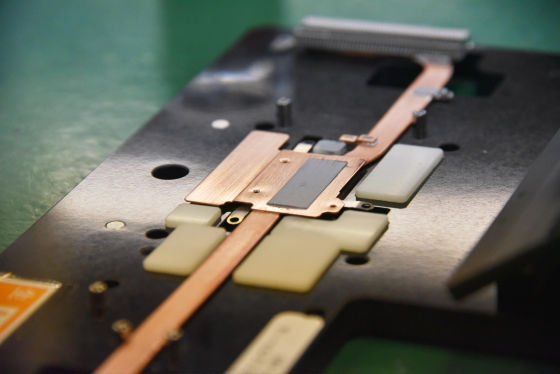
さらにグリスの塗布作業はすべてカメラで記録。
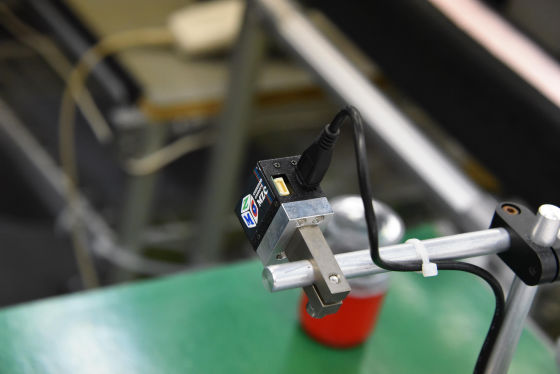
製品ひとつひとつの基板のグリスがどのような状態で塗られていたのかまで追跡できるようにすることで、高いクオリティを担保しているというわけです。
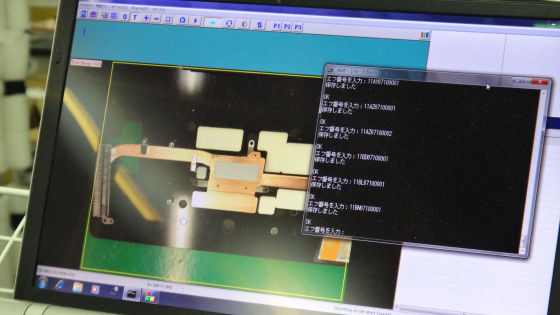
専用の治具でヒートパイプや冷却用ファンを固定してネジ止めすればCPU周りは完成。
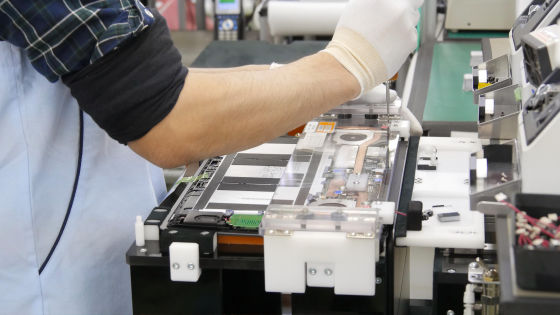
すべての部品を組み上げて完成したVAIO Zは、この「自動検査機」に入れられ全機能が正しく動作するかチェックされます。
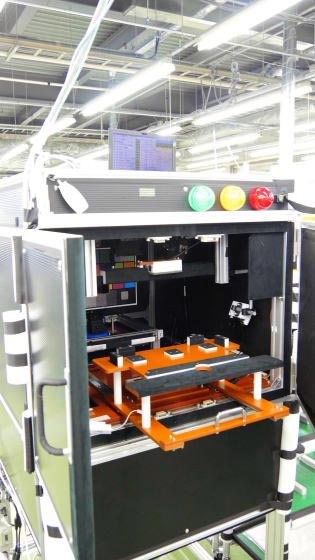
こんな風に組み立て済みのVAIO Zを箱の中に設置して……
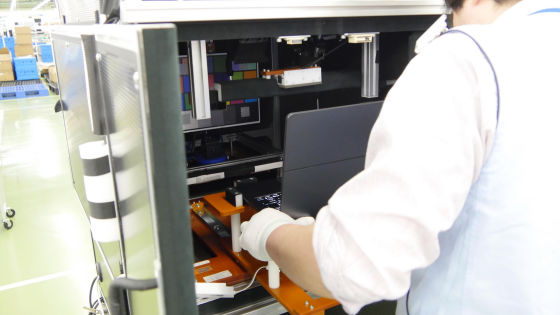
扉を閉じてスイッチON。
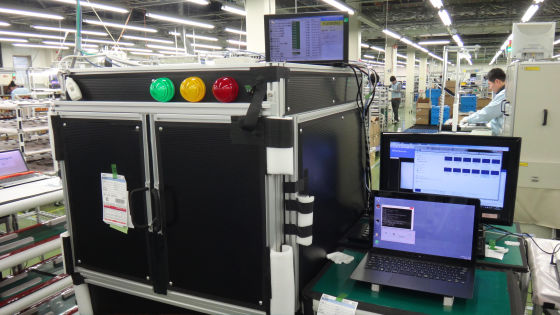
数十種類の検査をすべて自動で実行します。
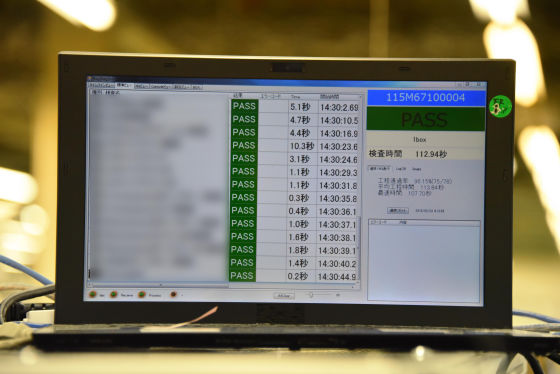
自動検査機のテストを通過して、ずらりと並べられたVAIO Z。ここでは、最後のファンクション検査として各種機能の最終テストが行われます。バッテリーの充放電テスト、SSDの速度チェック、長時間フルパワーで稼動させる負荷テストなどをみっちり行った上で、合格した機体にはOSやソフトウェアのインストールが行われます。なお、この工程はほぼ自動とのこと。
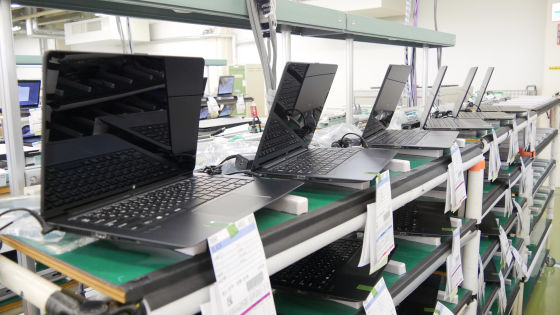
機械によるチェックをクリアした後に待ち構える最後の関門が、人間による外観チェック。人が使うものである以上、最後は人間の厳しいチェックをくぐり抜ける必要があるというわけです。
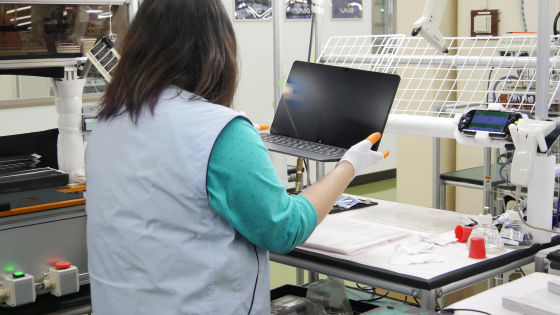
外観検査認定証を持つ「気づき」のプロのみが最終チェックすることを許されており、チェックポイントは全部で100項目以上とのこと。キーボードの打鍵感や筐体の隙間など、チェックのプロが見て触って「質感」を徹底的に検査します。
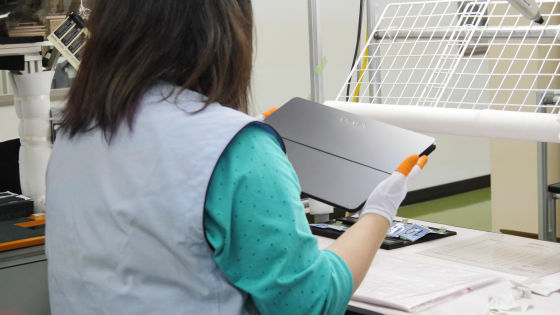
なお、パームレストに貼り付けられたラベルの有無・位置についてはカメラによる自動検査も並行して行われます。こうしてすべての検査をクリアしたVAIO Zには安曇野フィニッシュの認定カードが同封されて、ユーザーのもとへと出荷されるというわけです。
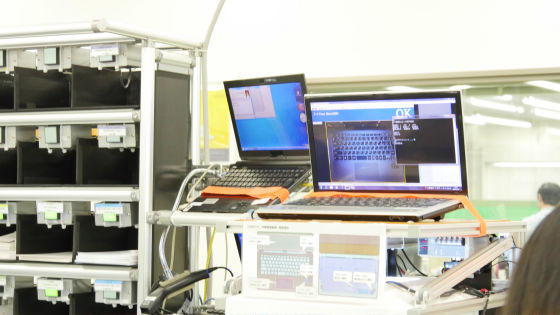
・おまけ
VAIO Zが生み出されるエリアの外に、なにやら怪しげな作業場がありました。
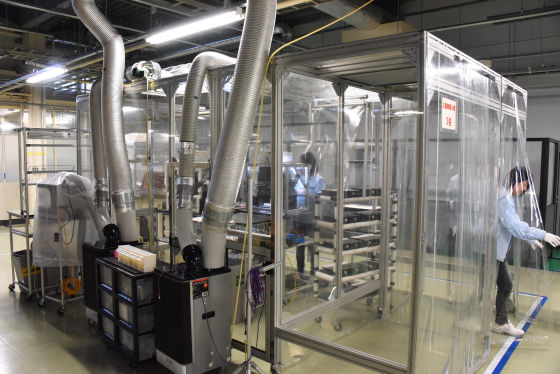
ガラス張りの中はさながらクリーンルーム。これは、保護フィルムの貼り付けを行うブース。
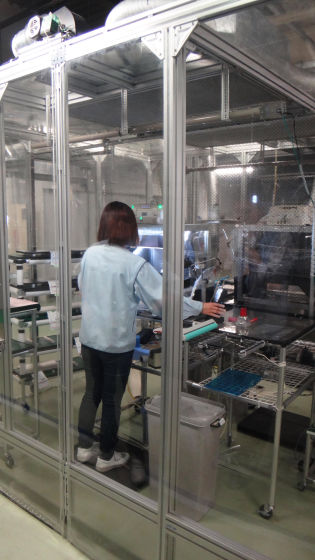
ホコリやゴミが入ってないか確認しやすい専用のLED照明が使われているとのこと。
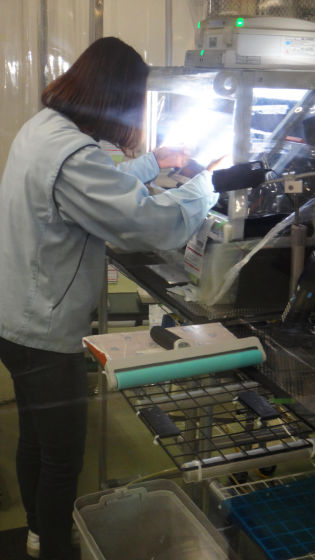
貼り付けられた保護フィルムは、2人がかりでチェック。
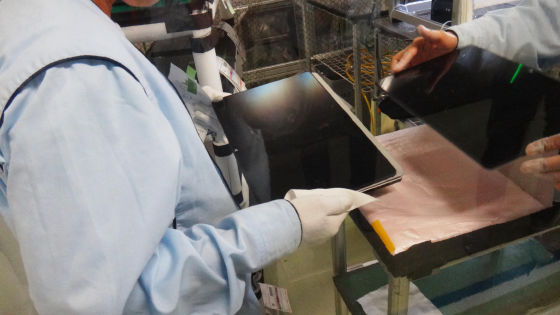
貼り付けた状態を確認させてもらうと、後から貼り付けたとは分からない仕上がりで、気泡やゴミの混入は一切なし。スマートフォンと違って大画面のVAIO Zのディスプレイにユーザーが手作業で保護フィルムをこのクオリティで貼り付けるのは至難の業。ということで、VAIO Zを注文するかなりの割合の人が保護フィルム貼り付けオプションを指定するそうです。
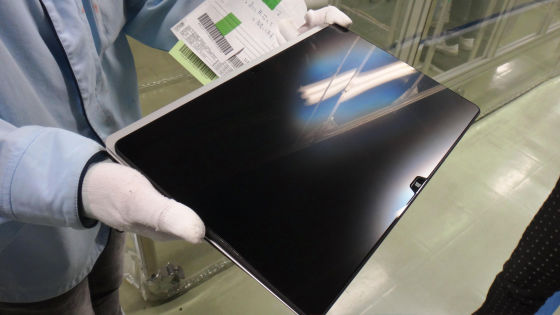
VAIO Zを生み出す安曇野工場では、薄さ・軽さ・強さというスペック上の性能に加えて「使っていて気持ちいい感触」を生み出す「質感」にまで徹底的にこだわって、組み立てに専用の治具を使いまくり職人の手で組み上げるという製造工程が採用されていました。想像していたよりもはるかに「人間の手」の介在する部分が多い製造現場によって「モンスターPC」は生み出されているようです。
・関連記事
新生VAIOが「モンスター」と呼ぶ、圧倒的性能を見せつける2in1端末「VAIO Z」レビュー - GIGAZINE
新生「VAIO」が初の新製品発表会、一体何が飛び出すのか? - GIGAZINE
新生VAIOが「究極の道具」と語るフリップ機構採用の高性能ノートPC「VAIO Z」速攻レビュー - GIGAZINE
ソニーのVAIOブランドから転じた「VAIO株式会社」が誕生、新モデル3機種も発表 - GIGAZINE
「うん。欲しい」とクリエイターをうならせるVAIOのモンスタータブレットPC「VAIO Z Canvas」でお絵かきするとこうなる - GIGAZINE
2560×1704ピクセルのプロユース仕様タブレットPC「VAIO Z Canvas」速攻フォト&ムービーレビュー - GIGAZINE
・関連コンテンツ
in 取材, ハードウェア, Posted by darkhorse_log
You can read the machine translated English article What is MADE IN JAPAN 's tremendous thin….