なぜパナソニックは「Made in Japan」にこだわるのか、レッツノート神戸工場見学レポート
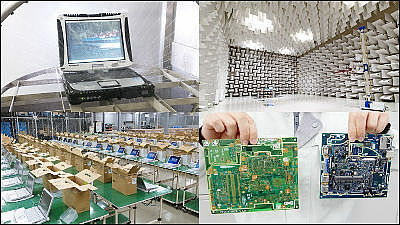
軽量・長時間駆動・高性能・頑丈という4つの特徴を兼ね備え、国内モバイルPC市場で約4割のシェアを獲得したのがパナソニックの「レッツノート」です。2014年には2in1モデルで世界最軽量の10.1型液晶搭載モバイルノートPC「RZシリーズ」が発表されたレッツノートシリーズは、全て国内の神戸工場で生産されています。神戸工場ではレッツノート以外にも「タフブック」を生産していますが、パナソニックがなぜここまで「Made in Japan」にこだわるのか、その謎に迫るべくレッツノートを生産している神戸工場を見学してきました。
神戸工場案内 | Made in japan | Panasonic
http://panasonic.biz/pc/news/madeinjapan/kobe.html
兵庫県神戸市西区にあるパナソニックの神戸工場にやって来ました。神戸工場はパナソニックの技術・営業・サービス部門がある守口市から自動車で1時間という連携が取りやすい距離にあります。
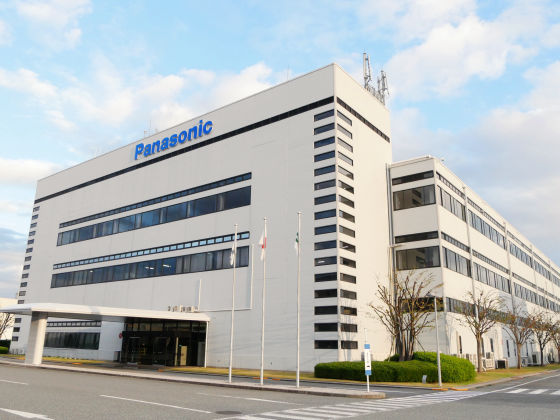
入口を抜けるとレッツノートおよびタフブックなどの製品が展示されたショーケースのお出迎え。
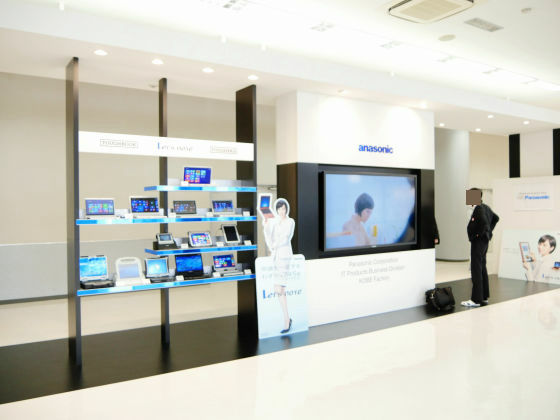
過去に発売されたモデルが並んでいます。
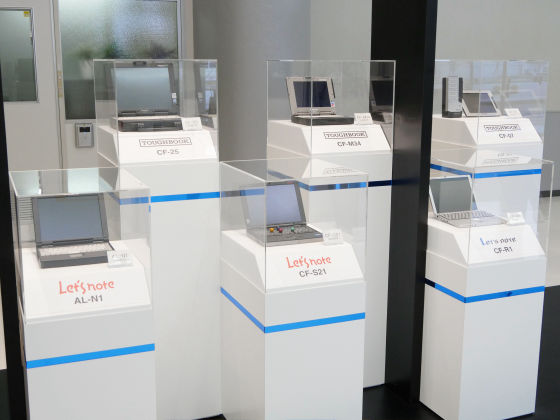
こちらはモバイルPCという言葉が存在しなかった1996年に販売が開始された初代レッツノート「AL-N1」です。当時のノートPCは重量が軽くても約2kgありましたが、AL-N1は重さが1.5kg以下に抑えられ、モバイルPCの先駆者のような存在。
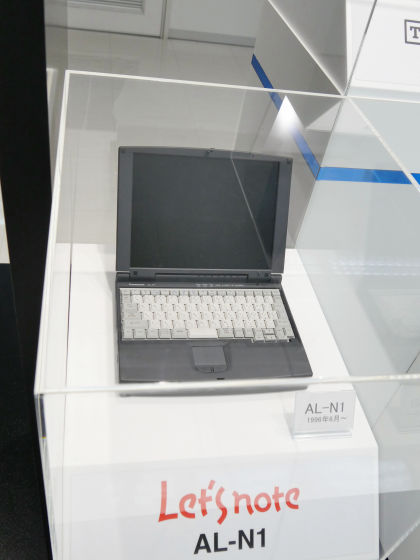
ベストバランスノートとして1998年6月に登場したのが標準5時間駆動・トラックボール搭載の「CF-S21」
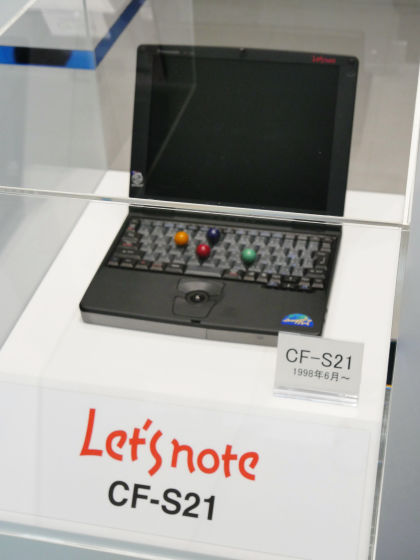
約960gで約6時間駆動という軽量・長時間駆動を実現し人気を博した「CF-R1」は2002年に発売されたビジネスモバイルPCです。
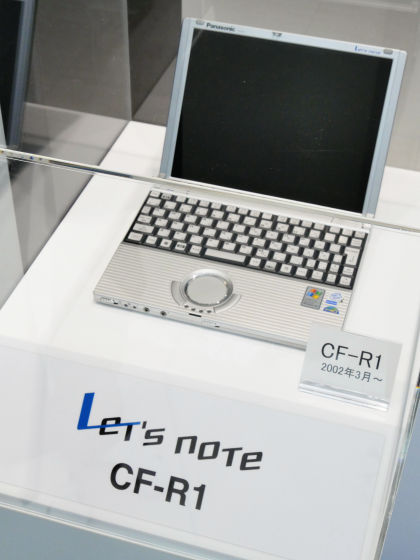
こちらには現行シリーズがズラリ。

1m20cmの高さから落としても壊れないタフブックの「CF-31」と、医療の現場などで活躍する「CF-H2」
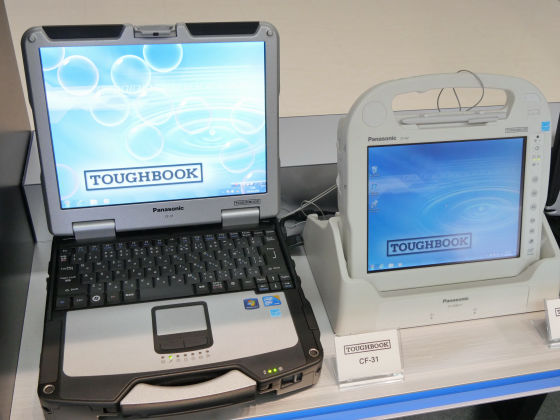
4KのIPSα液晶パネルを搭載し、3840×2560の高解像度を実現した「タフパッド 4K」は医療現場でレントゲンを見たり、机を囲んでの打合せを可能にしたりなど、さまざまなシチュエーションで活躍しています。
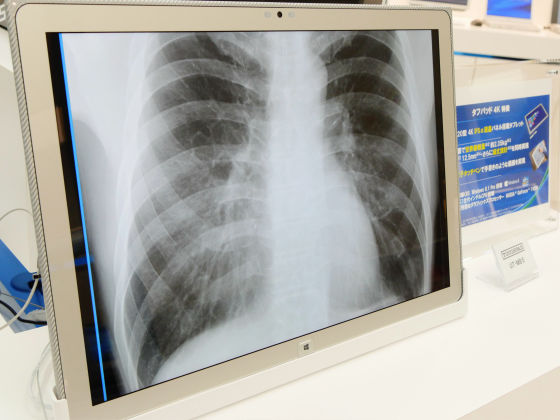
ショーケースには誰しもが見たことのある「ハンディターミナル」や「カード決済端末」なども展示されていました。
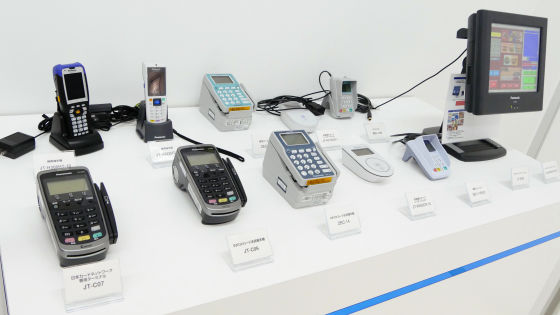
タフブックやレッツノートにはさまざまなモデルがありますが、パナソニックがこだわっているのは「どんなシチュエーションにも対応できる万能モデル」ではなく、「それぞれの分野やユーザーのニーズに特化したモデル」です。そのため、ユーザーのフィードバックを反映した製品作りに強く取り組んでいて、例えば、タフブックを使用していたアメリカの警察から「ハードディスクだけを取り出せるようにして欲しい」という要望があった際には、それだけのためにハードディスクを取り出せるモデルを開発したとのこと。なお、アメリカの警察がハードディスクを取り出したかった理由は「パトカーの車内に取り付けられているタフブックを放置したままコーヒーを買いに出かけられないから、ハードディスクだけでも持っていきたい」というものでした。
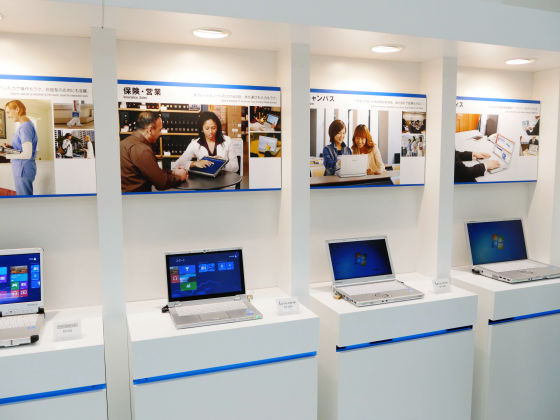
タフブックやレッツノートの過去・現行モデルをタップリと見させてもらった後は、いよいよ工場内部の見学スタート。最初に案内されたのは、製品の品質確保のために開発機を専用の試験設備で評価・検証を行う環境試験室です。
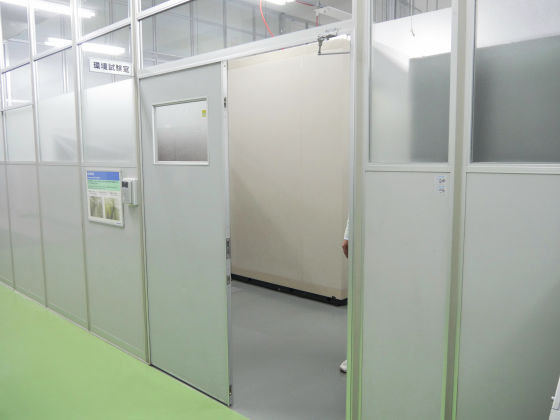
環境試験室の一部には見たことのない大きな設備が並んでいました。
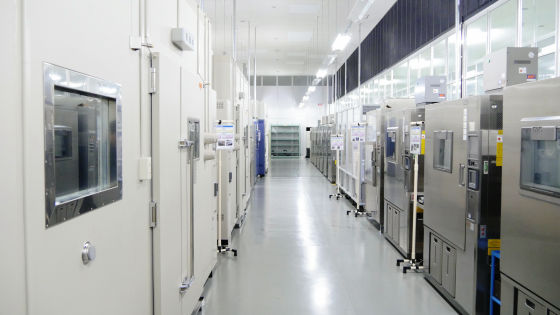
温度を設定した設備内にPCや部品を入れて、高温や低温の環境でも問題がないかを試験するマシン。
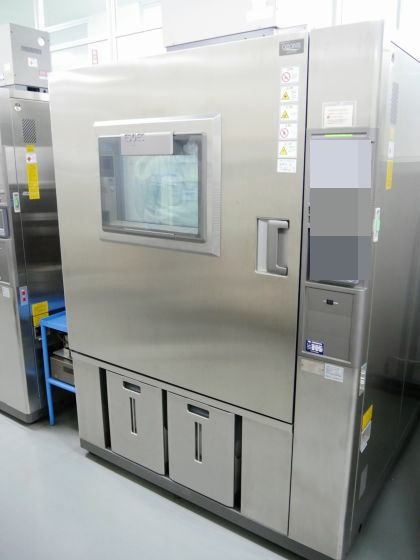
こちらは恒温槽と呼ばれる設備で、PCを内部に並べて温度を一定に保ちながら、PCが動作するかをテストします。先に登場したものよりもかなり大きいサイズです。
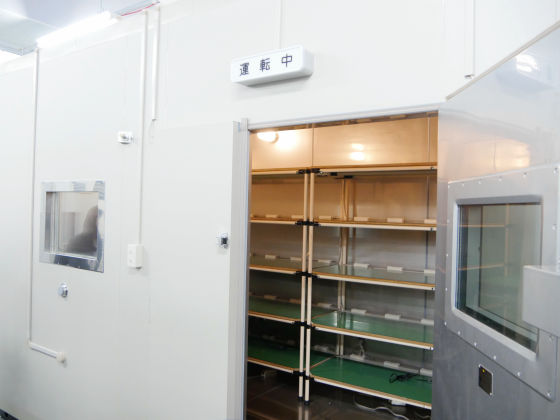
防水試験機はIPX4レベルの防水試験を行い、毎分1.8リットルの水を360度から散水する設備。回転しながらこれでもかと言わんばかりに水をPCにかけまくる姿には驚きを隠せませんでした。
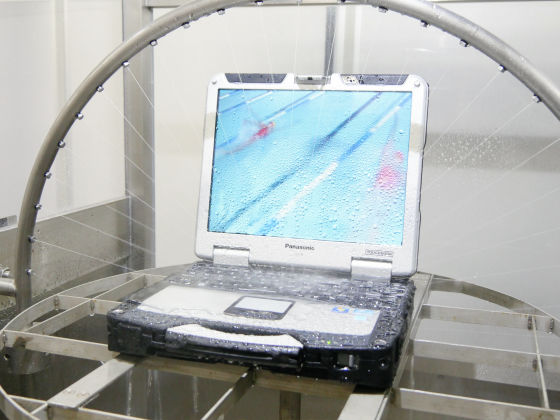
防水試験機がタフブックに散水している様子は下記のムービーから確認できます。
防水試験機でタフブックが水をかけられまくっている様子 - YouTube
防水試験器は他にもあり、下記の画像はIPX5レベルの試験を行っているところで、約3mの距離から毎分12.5リットルの水を3分以上かけます。ここまでPCがビショビショになっているところは見たことがありません。
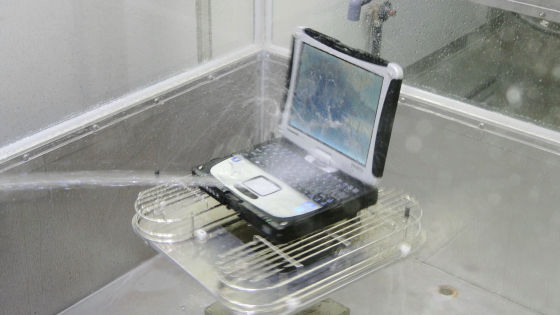
毎分12.5リットルの水をタフブックにかけているところは下記のムービーから確認できます。
毎分12.5リットルの水をタフブックにかけている様子 - YouTube
こちらは熱衝撃試験機というもので、高温と低温の衝撃を繰り返し与えることにより、PCの基板がどれくらいの年数もつのかを試験する機械です。さまざまな種類の試験器は全てパナソニックが開発したもので、不具合が発生した場合などにも迅速に対応できるようになっています。
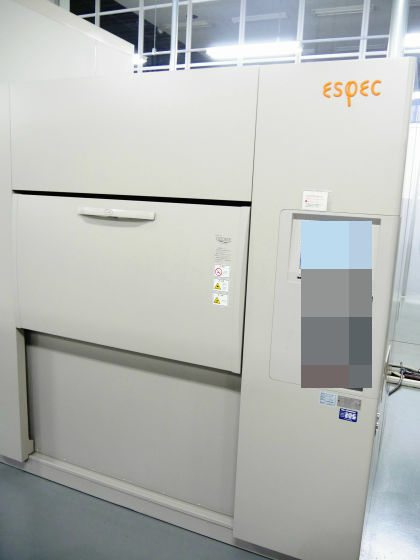
いったん外に出て案内されたのは「10m電波暗室」という名前の大きな建物。
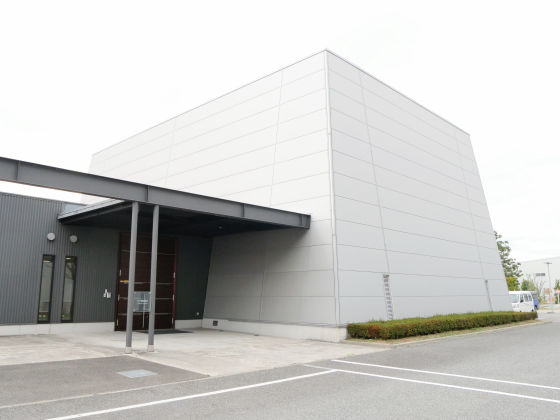
ものすごく頑丈そうな青色の扉を開けて中に入ります。
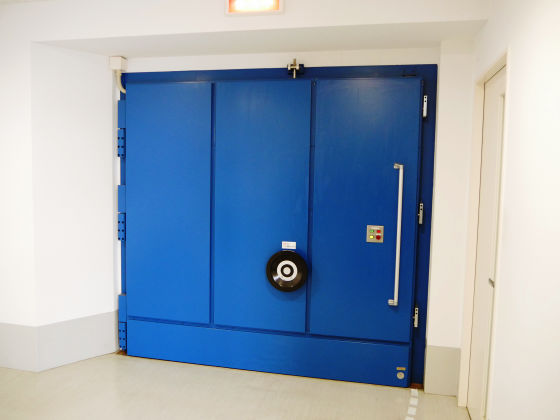
開くとわかる扉の分厚さ。
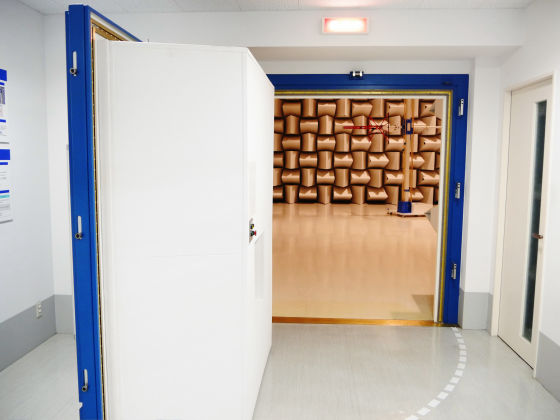
扉の厚さは人間2人分はゆうにあります。
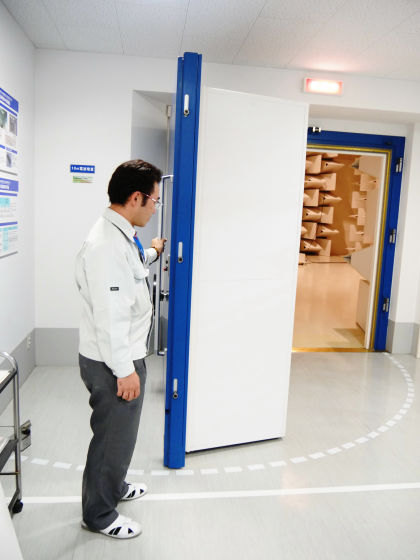
部屋に入ると、突起物がつけられた壁にビックリ。天井にもびっしりとつけられています。10m電波暗室は世界各国の電磁波規制に対する適合確認を実施する設備。電磁波の適合確認をする際には「PCと測定器を10m離して行う」というのがで決められているので、ここまで大きな部屋を用意する必要があるとのこと。
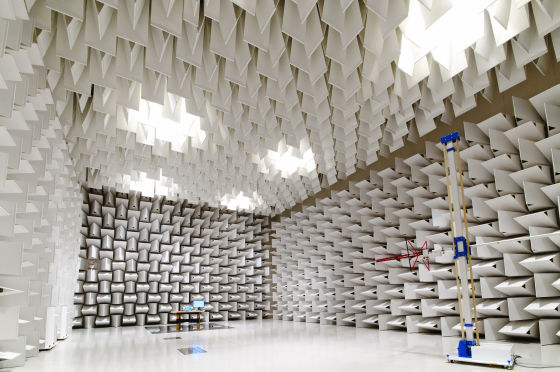
10m電波暗室の壁にびっしりと取り付けられているモノの正体は中空楔形電波吸収体です。
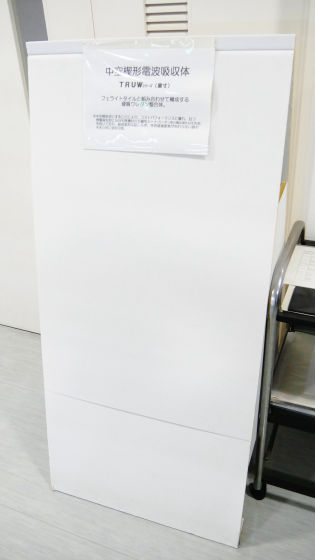
こちらが電磁波の測定器。
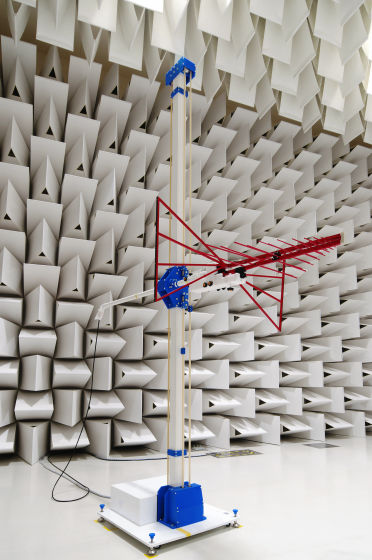
画像の手前にあるのが電磁波を発するPCで、10m離れて測定器が設置されています。
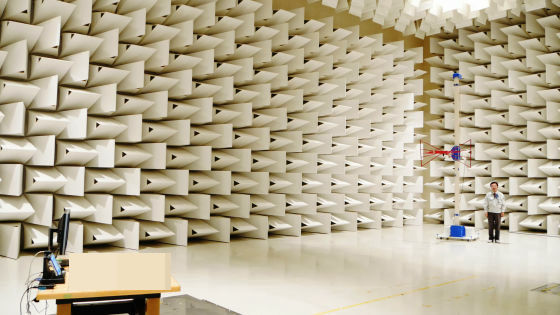
10m電波暗室は携帯電話やスマートフォンの電波が一切遮断されてしまうため、閉じ込められてしまうと外部と連絡をとることができなくなります。そのため、扉の内側には黒い円形のハンドルがつけられていて、いざとなると脱出できるようになっています。なお、取材時までに人が閉じ込められるようなことは一度も発生していないとのこと。
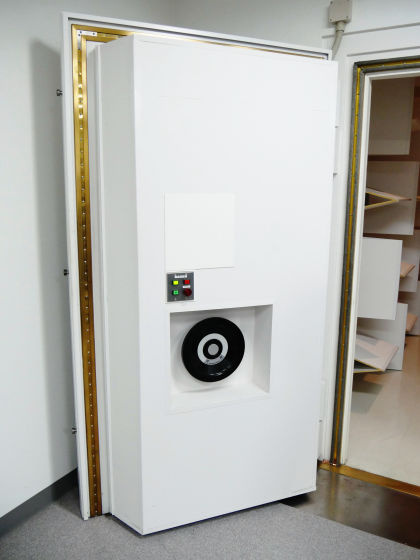
衝撃の10m電波暗室を後にして、再び工場内部へ。案内してもらったのは落下試験室です。
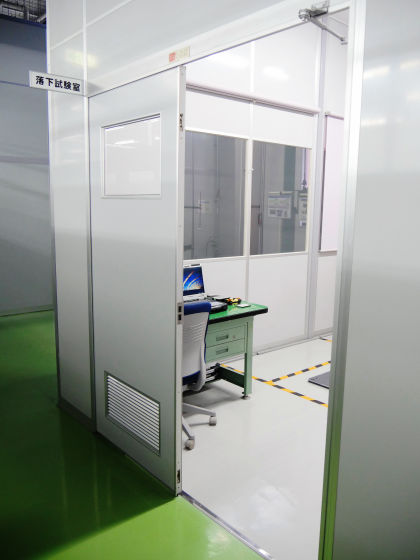
PCは6面・8角・12稜あり、その全方向である26方向から落として耐久性をテストするのが落下試験になります。ということは1つのモデルに対して26回の試験を行うということ。
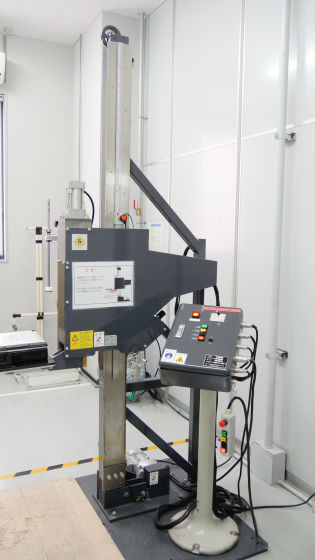
実際に落下試験を行っている様子は下記のムービーから確認可能です。
自由落下試験の様子
下記の画像のようにPCを斜め向きであったり、さまざま方向から落下させまくるわけです。
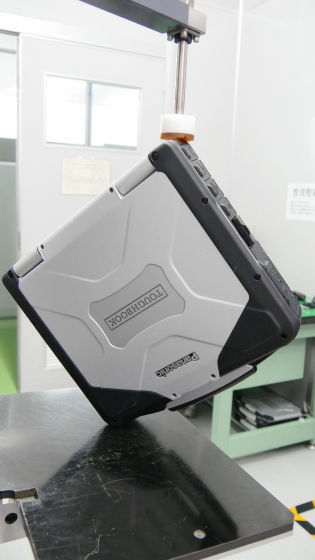
1階にはコールセンターと……
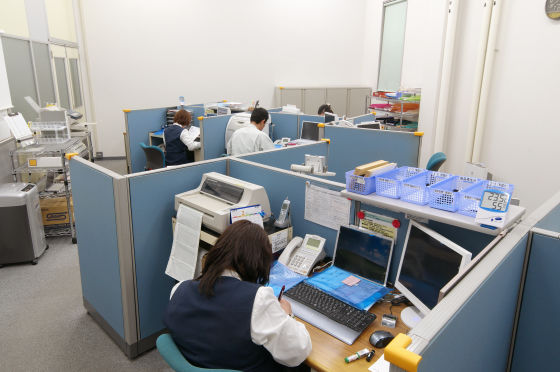
修理センターもあります。コールセンターはweb販売を中心としたユーザーからの問い合わせに直接対応。修理センターと隣接させることで、ユーザーの要望を迅速に反映させたり、修理時間を最大限短縮化したり、さまざまな利点が産まれるとのことです。

1階の見学を終えて、続いては2階の生産エリアの見学。生産エリアでは実装・ボード組立・完成組立・検査・カスタマイズの工程が行われています。
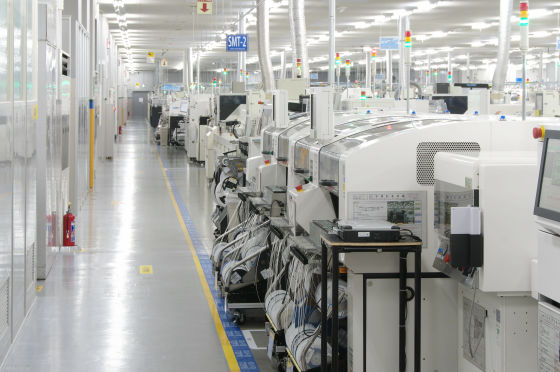
生産エリアは基板の実装からスタート。実装は基板に、どの基板がいつ作られたものなのかを確認するQRコードを印字し、クリームはんだを載せていくところから始まります。
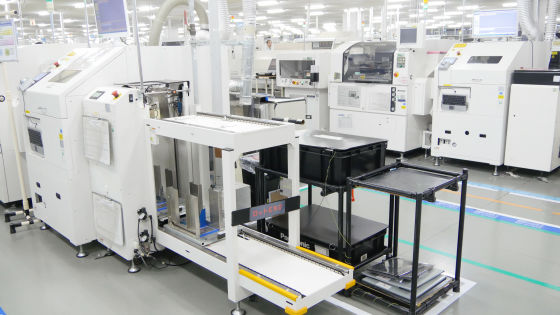
左が実装前、右が実装後の基板。8~10層の基板に約1500~1600個の部品がつけられています。
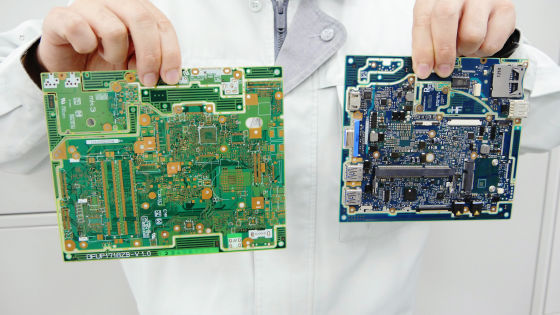
クリームはんだを載せた後は、電子部品実装機で部品を装着。
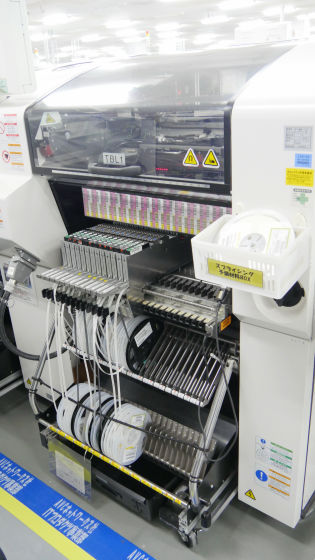
電子部品実装機は手前へ奥へと激しく動きながら、小さい部品からだんだんと大きい部品を基板につけていきます。1つのマシンで同時に4枚の基板を処理可能。
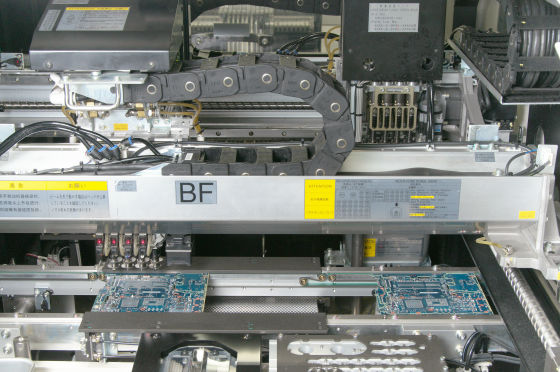
電子部品実装機が基板の上に部品をつけている様子は下記のムービーから確認可能です。
電子部品実装機で部品を基板につけている様子 - YouTube
電子部品実装機の下側にはテープのようなものに部品がびっしりと並んでいました。
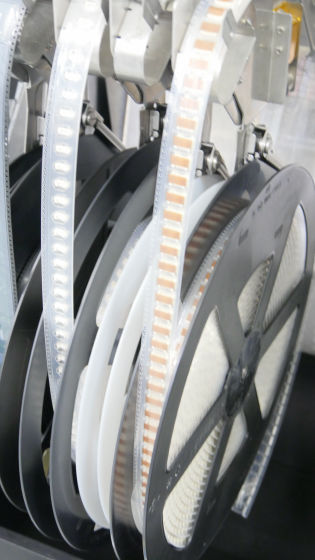
電子部品実装機でクリームはんだの上に部品を置いた後は、180℃から270℃まで段階的に熱してはんだを溶かし、続いて冷やして固めます。実装が終わるとパーツが正しく置かれているかどうかをチェック。マスターを写真撮影しておき、それと比較しておかしい部分があったらはじきます。はじかれたら1つ前の工程に問題があるのか、それとももっと大きな問題なのかを確認。この段階では片面が終わっただけなので、再度同じ処理を行い、もう片方の面の実装を行います。
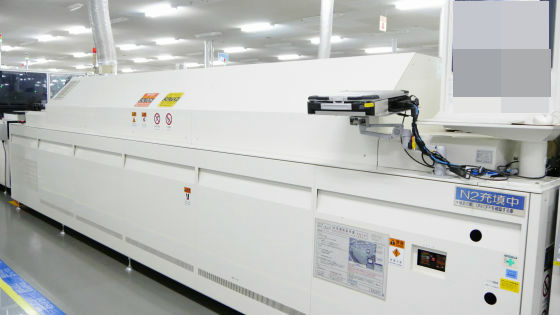
実装が終わったら、ロボットによる基板テスト。基板テストではロボットが3枚の基板を時間差でチェックしていきます。
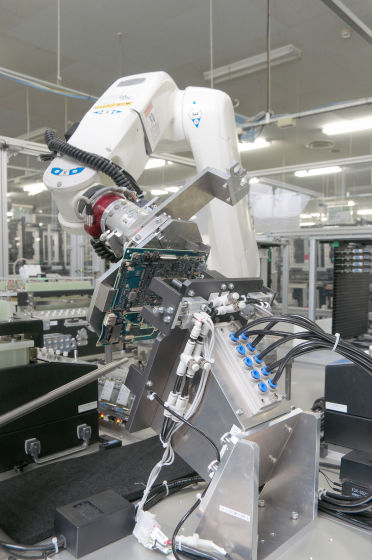
ロボットにとって難易度が高いのはテスト用の拡張メモリを挿す作業。人間なら感覚で調整可能ですが、ロボットはすべてプログラムする必要があるからとのことです。
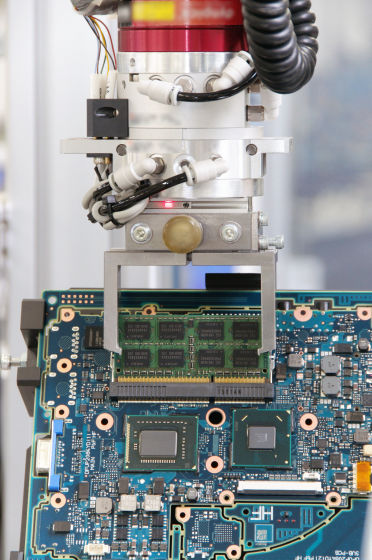
基板の実装の後は組立の工程です。実装はライン的にロボットが作業をしていますが、組立は1つ1つ手作業で行われています。どうしてかというと、人の方がロボットより強いため。作業工程が変更されても人ならすぐ対応でき、作業時間が早くなるからとのこと。
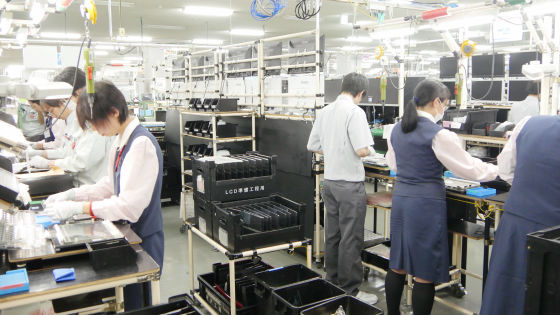
工場内は「共用通路/共用スペース」と、パナソニックエクセルスタッフ/日本ケイテムといったパートナー会社ごとのエリアに分かれており、パートナー会社のスペースにはパナソニックの社員でも入ることができませんが、今回は特別に作業エリアを見学させてもらいました。
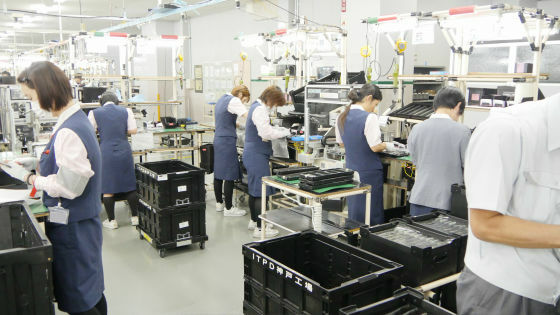
レッツノートのRZ4シリーズを組み立てているところ。組立は丁寧すぎるほど1つ1つ入念に行われます。
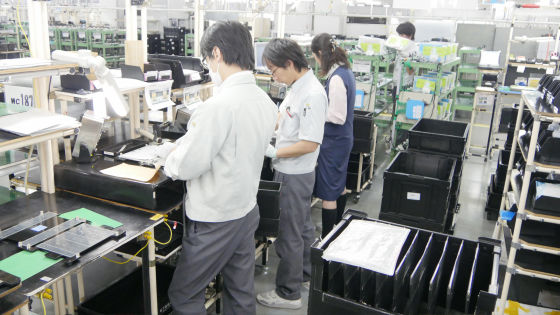
組立が完了したら専門のスタッフが1台1台チェック。
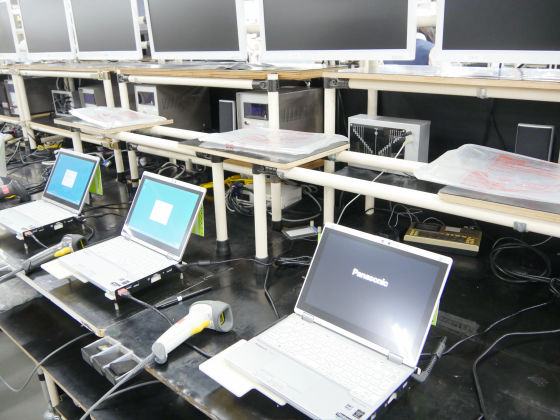
こういった工程を経て出荷されるわけです。
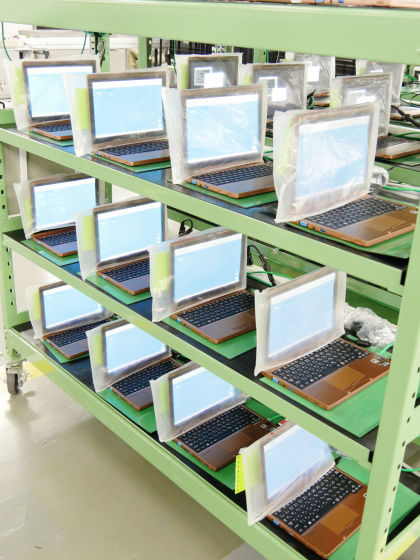
生産エリアの一番奥にはパナソニックのショッピングサイト「Panasonic Store」で注文されたPCを取り扱うスペースがありました。こちらではHDD・メモリ・カラー天板など、約2000種類にもなるカスタマイズを行います。
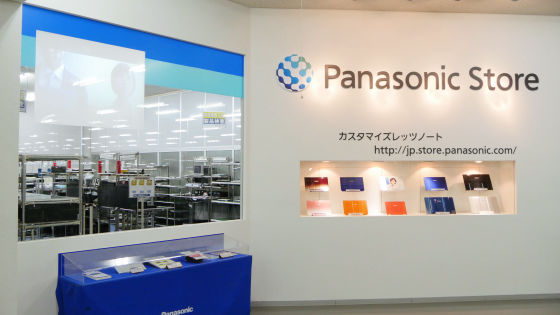
最後は再び1階に戻ってコンフィグセンターを見せてもらいました。
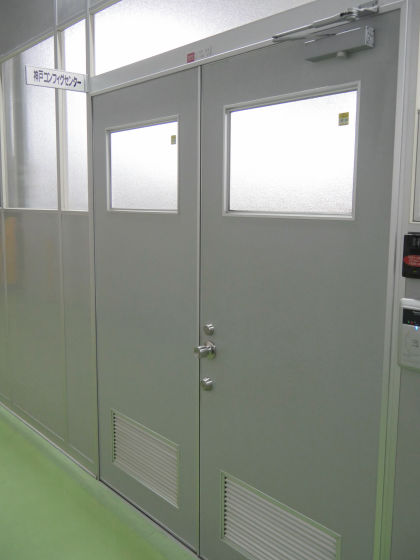
コンフィグセンターでは、オプションの設定やソフトのインストールなど各企業・大学ごとに要望があるものに対応。昨年度は約9万台ものPCがこちらでカスタマイズされました。
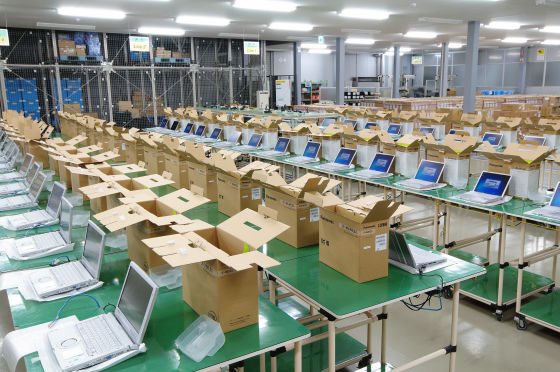
これにて全ての見学は終了。見学後は「何か改善できる点はないか」「普段の使用で不便に思っていることはないか」など、レッツノートを日頃より使用している編集部員に対するフィードバックが行われました。いろいろ要望を言ってみたので、もしかすると反映されるかもしれません。ユーザーとの連携を強固に保ち、要望を可能なかぎり反映するのがパナソニックが国内生産にこだわり続ける理由の1つです。また、開発を日本で、組立を中国で行うのではなく、開発・実装・組立までを全て国内で行うことで、一貫した品質と生産性を保っているのを神戸工場で実感しました。
・関連記事
「新・レッツノート発表会」まとめ、新機種はこんな感じ - GIGAZINE
新・レッツノート「RZシリーズ」実機を速攻フォトレビュー - GIGAZINE
レッツノートにカフェオレがこぼれて壊れたのでパナソニックに修理を依頼してみた - GIGAZINE
天板が割れたレッツノートの修理をパナソニックに依頼してみたよレポート - GIGAZINE
タフボディで重量約1.1キロ、8時間駆動の新型「レッツノート」実機レビュー - GIGAZINE
・関連コンテンツ
in 取材, ハードウェア, 動画, Posted by darkhorse_log
You can read the machine translated English article Why Panasonic sticks to "Made in Japan",….