An open source air quality monitor maker talks about the process of contracting with a Chinese mold maker and manufacturing parts.
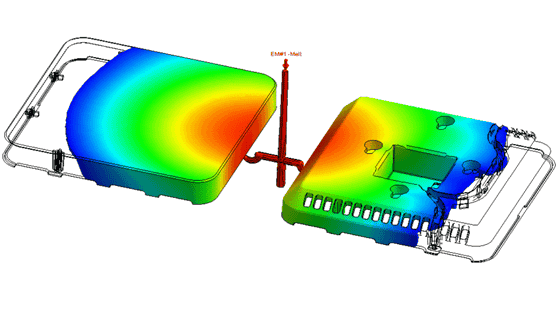
Air Gradient, an open source developer of air quality monitors that measure the air environment, such as temperature, humidity, atmospheric pressure, gas concentration in the air, and concentration of particles such as PM2.5, is developing its product in China. I am publishing the story of my business negotiation with a mold manufacturer.
Our Journey of Making a Plastic Injection Mold with a Chinese Mold Maker
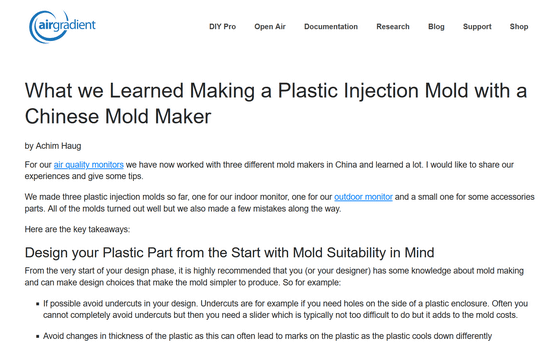
Air Gradient, which sells open source air quality monitors that you can assemble yourself, has so far created three types of plastic injection molds for air quality monitors, all of which they ordered designs from different mold manufacturers in China. is.
Air Gradient points out the following four points regarding the knowledge required at the beginning of the design stage.
Avoid undercuts in your design
Injection molding involves injecting heated and melted plastic into a mold. For example, if you make a dent in the part, as shown on the left in the figure below, the molded product will get caught in the mold and cannot be removed from the mold. This type of design that cannot be removed from the mold using normal methods is called an 'undercut.'
by
It's difficult to completely eliminate undercuts from product design, but they do add cost, so it's best to avoid them if possible.
・Keep the thickness of the plastic as constant as possible
If you vary the thickness of the plastic in different locations, the time it takes for the plastic to cool down will vary depending on the location, increasing the chance of marking the plastic.
・Think about the parting line
The mold has a male and female part, and plastic is injected and molded between them. As a result, the molded product has a thin line called a 'parting line' where the male and female parts meet. These thin lines cannot be avoided when molding is used, so they must be incorporated into the product design.
-Avoid designs that use right angles
A slight angle is required to eject the part from the mold. This is why plastic buckets are designed to open gradually from the bottom to the top. If a right-angled design is incorporated into the molded product, the molded product cannot be ejected from the mold using normal methods, which increases costs.
Below is a plastic case for an indoor air quality monitor designed by Air Gradient based on the above four points.
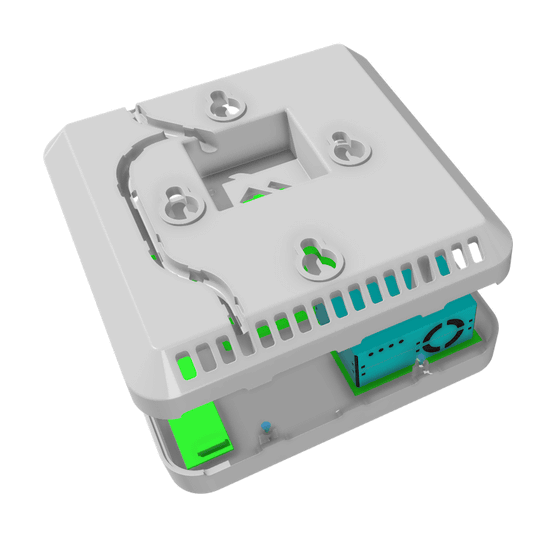
After designing the product design, it's time to select a mold manufacturer. Air Gradient hired an engineer with many years of mold manufacturing experience as a consultant, asking him to design a simpler and cheaper mold, comment on the mold manufacturer's estimate, and check the mold and molded product. is.
Chinese mold manufacturers are responsible for both manufacturing molds and molding plastic parts. In many cases, the contract includes a warranty on the mold, so if a problem occurs, they will repair it free of charge. Therefore, first of all, it is necessary to check the price for each quantity of parts manufactured.
Additionally, since the ownership of manufactured molds is often unclear, it is important to clarify who owns the molds at the time of contract. At Air Gradient, we work with mold manufacturers to determine the ownership of the mold and the number of plastic parts to be produced, and if we wish to transfer the mold to another production line, we make sure at the time of the contract how much to purchase the mold. I think it should be made clear.
Pour melted plastic into the mold. Therefore, it is necessary to simulate the route through which the plastic will flow, and to check that there will be no unevenness or warping in the molded product.
Once everything is checked, the mold maker will create a 3D drawing of the mold. This includes not only the mold, but also all parts such as the cooling system and extrusion pins. Mold manufacturers sometimes try to save costs here, but skipping this step can easily cause problems, and trying to change it later is extremely difficult and costly. It is very important to carefully review this 3D drawing with your consultant. Air Gradient says, 'Spend time and resources reviewing 3D drawings of your mold.'
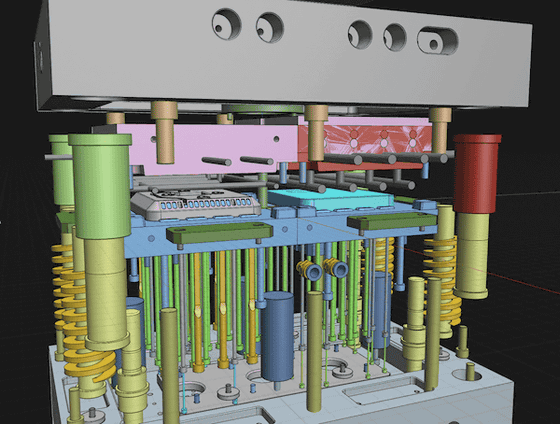
According to Air Gradient, it took about a month to actually complete the mold after checking the 3D drawing above and getting the OK. The first sample to be molded after completion has no surface treatment and is called a 'T0 sample.'
This T0 sample is thoroughly checked to ensure that the dimensions are correct, the parts fit together securely, the screws turn, there are no cracks, and there are no sink marks . Continue checking this T0 sample until there are no issues.
Next, we will create a 'T1 sample' that is compatible with the production environment, including surface treatment. Check here that the surface treatment is applied evenly and that the color matches your requirements. After checking the T1 sample, we can finally start producing plastic parts.
In conclusion, Air Gradient says, ``I think we have had a very good experience with Chinese mold manufacturers, and we are very satisfied with the quality of the molded products.One of the important factors for success is 'You'll have experts on hand who can give you an independent opinion should you need to make a decision.'
Related Posts:
in Hardware, Posted by log1i_yk