We sneak into the Taiwanese factory of major semiconductor company Micron and discover the manufacturing process of one of the world's largest semiconductor manufacturers.
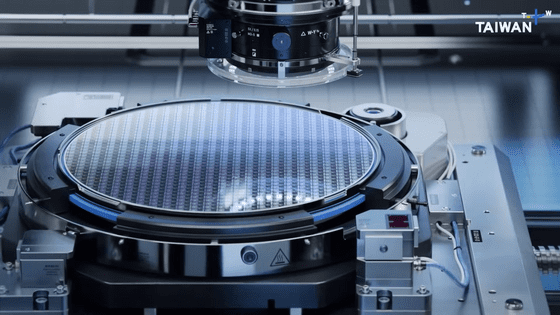
Inside Micron Taiwan's Semiconductor Factory | Taiwan's Mega Factories EP1 - YouTube
Taiwan, home to the world's largest semiconductor manufacturing companies, has three science parks in the north, central and southern parts of the country, with facilities for every stage of semiconductor production. For nearly 30 years, Micron has been producing semiconductors for memory used in computers, smartphones, medical devices and more in Taiwan. The number of employees working at the company's vast 1 million square meter site accounts for 25% of Micron's total workforce.
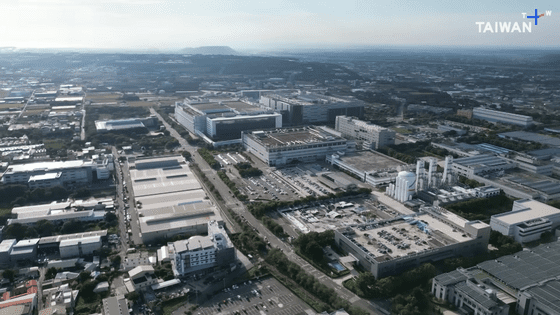
Micron's energy center, Starship, is the factory's brain, controlling the power system, water system, air conditioning, and chemical management. Monday mornings, when power and water usage is at its peak, are Starship's busiest hours, and Starship manager Rex Lai said, 'We have a great responsibility to ensure the stability and reliability of Micron's product supply.'
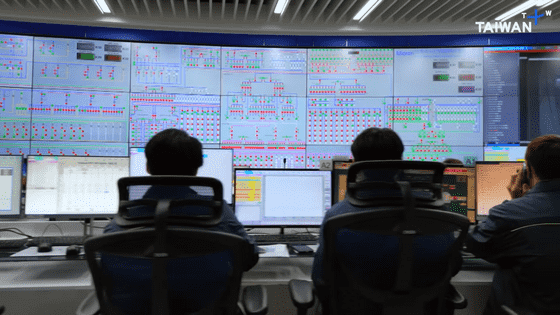
Micron's semiconductor manufacturing involves more than 1,000 steps, and everything from design to manufacturing, assembly, and testing is completed within the factory. The 'R&D Hub' in the factory is responsible for semiconductor design, and detailed development is carried out to embed billions of transistors on a small substrate.
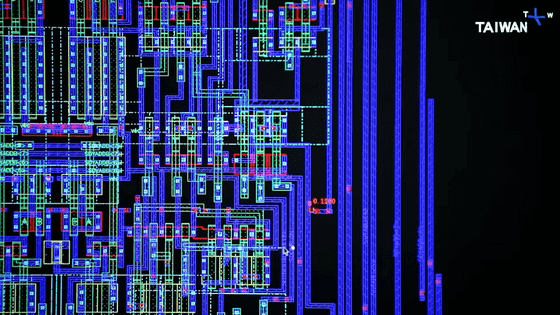
In actual semiconductor manufacturing facilities, thorough management is carried out to prevent the intrusion of dust and dirt. Employees involved in manufacturing wear protective clothing that covers almost all of their skin, and undergo an air shower to remove further dust and dirt before entering the clean room.
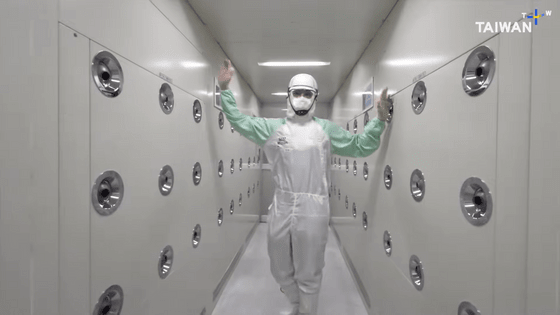
The first process in semiconductor manufacturing is silicon wafer preparation: a robot places a 12-inch silicon wafer in place.
Next, a UV photosensitive liquid is dropped onto a rapidly rotating silicon wafer, coating it evenly.
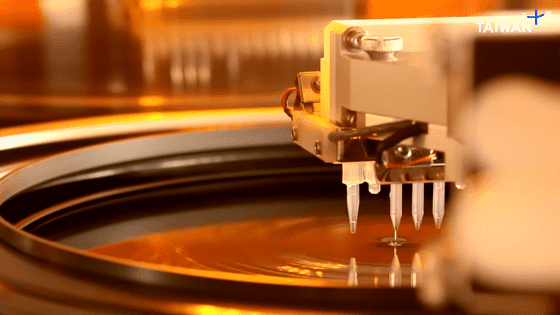
The silicon wafers coated with the UV photosensitive liquid are then fed into high-precision photolithography machines, each of which costs $100 million (approximately 15 billion yen).
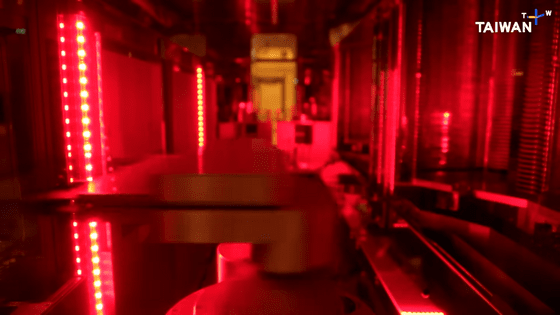
Inside the device, a pre-created circuit design is projected onto a silicon wafer using UV light.
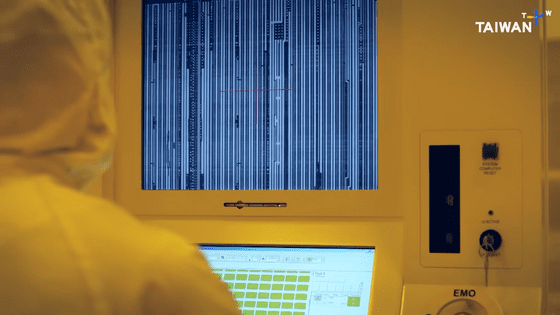
The areas exposed to the UV light will harden while the unexposed areas will be etched away.
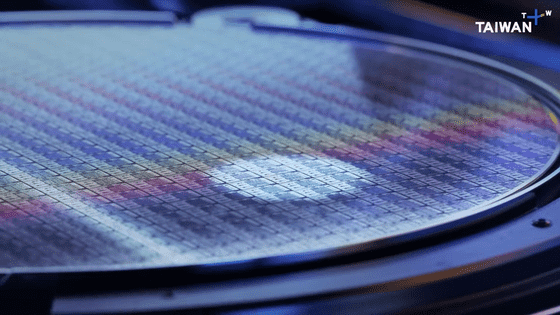
Because the circuits are multi-layered, the photolithography process must be repeated many times, and because the paths in the circuits are so fine, measuring just a few nanometers, even the slightest bit of contamination from dust or dirt can completely stop the production line.
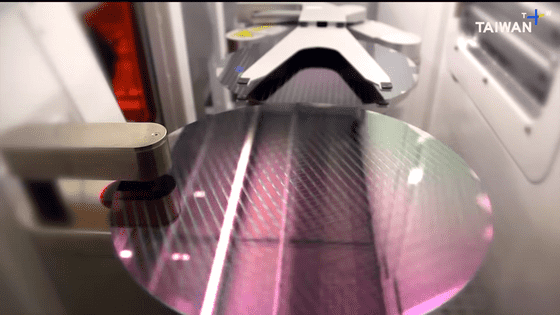
To minimize the risk of contamination, the movement of silicon wafers within the factory is automated. The wafers are automatically loaded into special containers and then loaded onto small buggies that run along overhead rails. The wafers are then automatically fed into the machines that carry out each process.
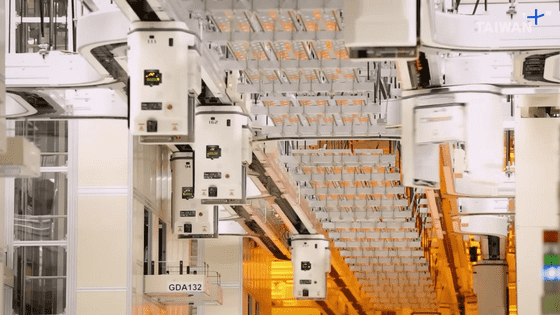
Countless buggies move at high speeds inside Micron's factories, and these buggies are equipped with sensors to avoid collisions.
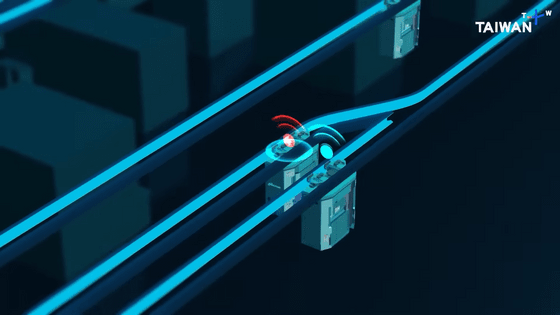
The factory is home to thousands of large, reliable machines that require constant human supervision, monitored remotely by a small crew located on the other side of the factory to prevent contamination.
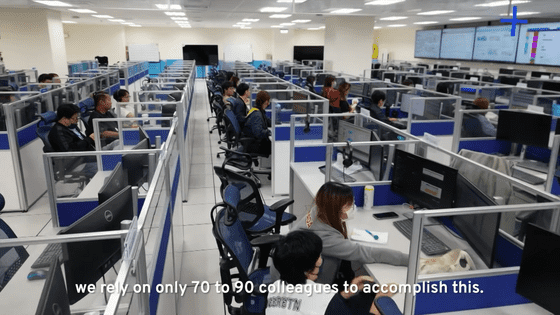
These crews analyze massive amounts of data from more than 50,000 sensors and 250 million control points - Micron's Taiwan factories generate 30 petabytes of data every day - and streamline that data to display key metrics on screens to quickly understand any issues occurring within the factory.
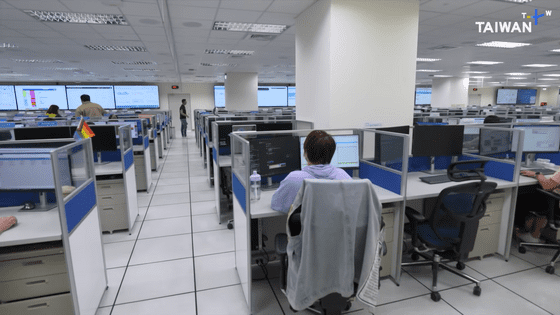
Each silicon wafer is then checked for quality and separated into individual chips using a diamond blade.
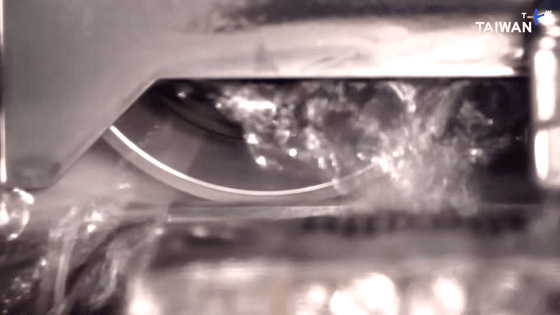
The divided chips are placed one by one on the circuit board.
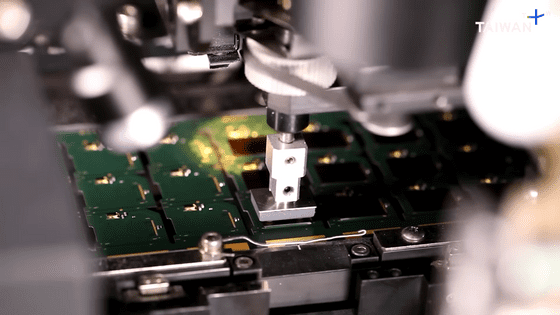
Next, connect the integrated circuits to communicate with other components.
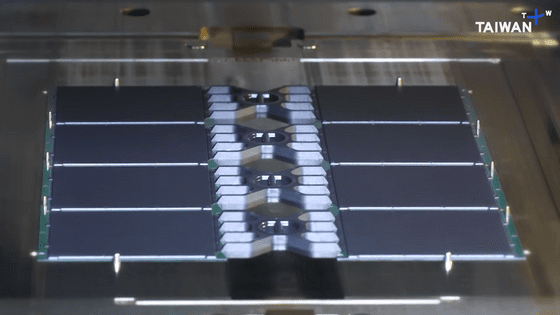
Semiconductors are very delicate and fragile, so each chip is placed in a black case and then encapsulated to protect it from moisture and corrosion.
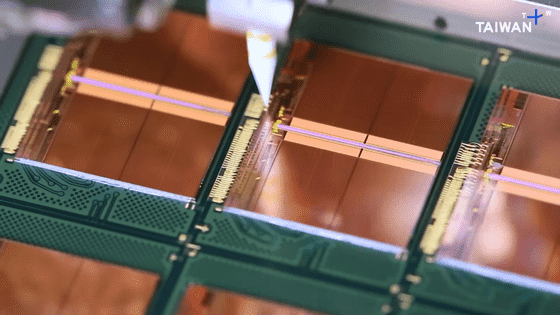
The encapsulated chips undergo a final test during which those that do not meet the standards are automatically rejected.
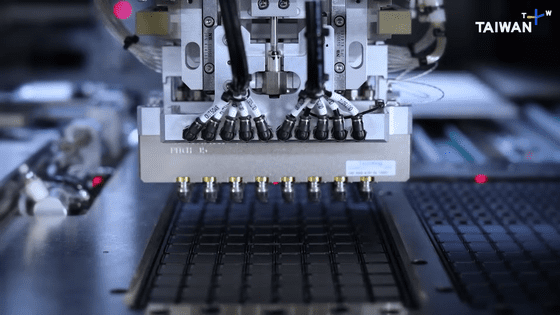
Chips that pass the test are laser marked with an identification tag.
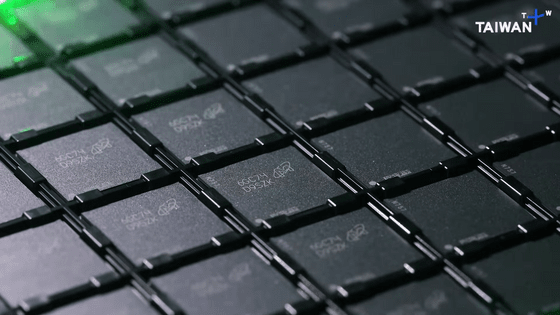
The completed chips are then packaged and shipped all over the world.
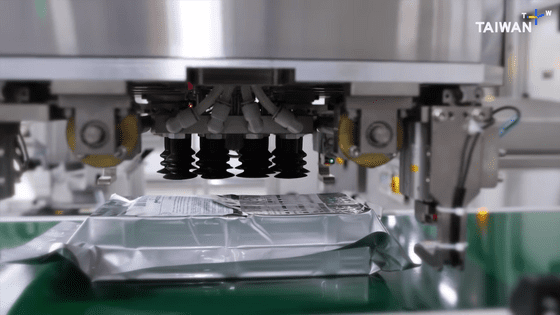
Because the semiconductor manufacturing process consumes large amounts of water and electricity, Micron Taiwan factories are taking various steps to reduce their environmental impact. For example, Micron has introduced the world's first chemical concentration system that converts used
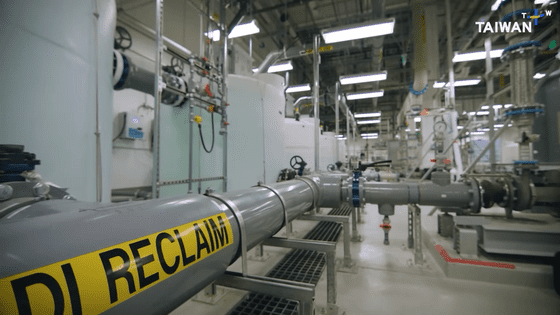
In addition, Micron's Taiwan factory is planting plants on the walls and creating green areas to improve the environment.
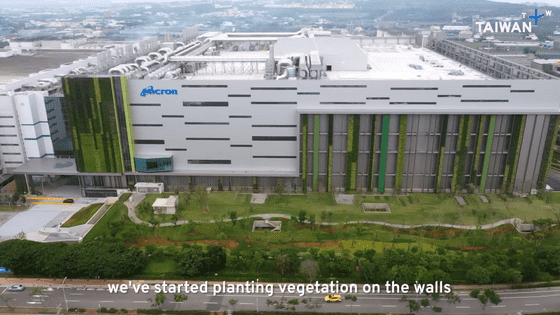
Related Posts: