A state-of-the-art semiconductor factory that makes full use of artificial intelligence and AR technology is about to start operation, and a '360-degree movie overlooking the factory' is also on sale
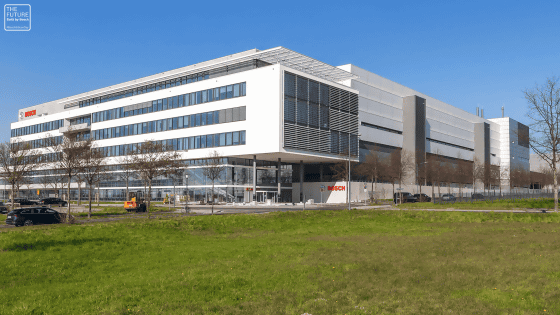
Bosch chip factory Dresden | Bosch Global
https://www.bosch.com/stories/bosch-chip-factory-dresden/
Bosch opens wafer fab of the future in Dresden --Bosch Media Service
https://www.bosch-presse.de/pressportal/de/en/bosch-opens-wafer-fab-of-the-future-in-dresden-230080.html
Bosch reaches milestone on the way to opening new wafer fab in Dresden --Bosch Media Service
https://www.bosch-presse.de/pressportal/de/en/bosch-reaches-milestone-on-the-way-to-opening-new-wafer-fab-in-dresden-225600.html
Concept of total floor area of 72,000 square meters of Bosch of the new plant is in 2017 and rose over 1 billion euros, including a grant from the German government and the European Union (approximately 130 billion yen), 2018 Construction started in June of the year. 700 people will work as employees in the factory, using the latest AI, IoT, and state-of-the-art technology that makes full use of augmented reality (AR) to analyze the manufacturing process in real time and perform machine maintenance remotely. It is said that work is possible.
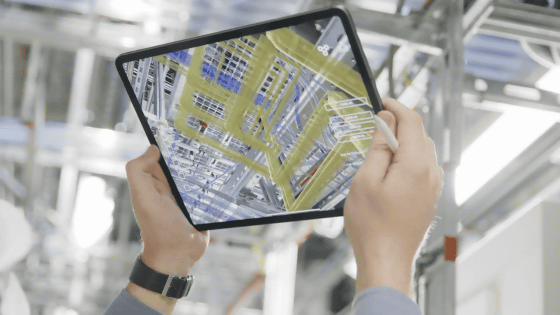
In the following movie released by Bosch, you can get a 360-degree view of the inside of the factory. If you use a smartphone or VR device, you can tour the factory from home.
Employees change clothes and move into a completely clean factory to handle semiconductors that are one-fiftieth as thick as human hair.
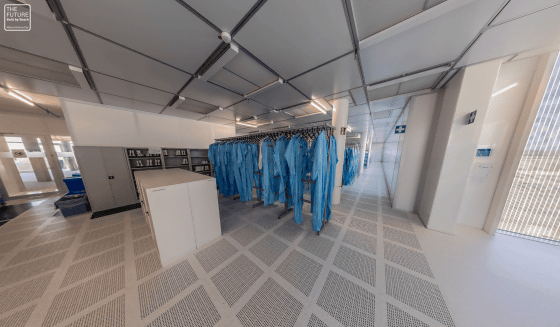
The inside of the factory looks like this. It is said that it is illuminated with yellow light in order for the
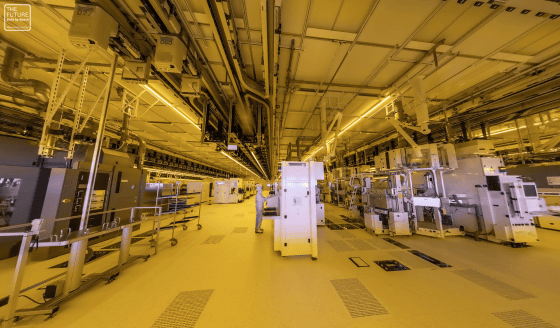
Since it is necessary to supply materials to the wafer day and night, it is said that the
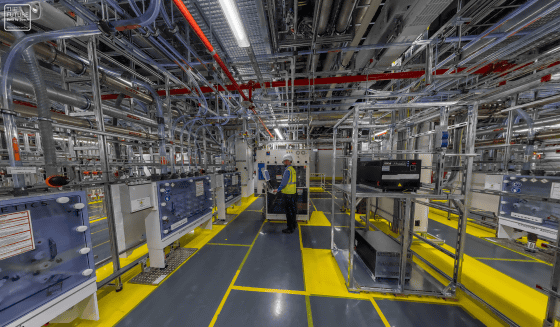
There is also a tank that stores water, which is indispensable for semiconductor manufacturing. It is said that 1200 cubic meters of water is used every day.
Wafers begin with the work
Semiconductor production process explained --YouTube
Bosch carried out the first wafer manufacturing process in January 2021 for a full-scale mass production system, from July 2021 to chips for power tools, and from September to the operation of mainly automobile automatic braking systems. We plan to manufacture a dedicated power management chip designed to perform only a single task and an application specific integrated circuit (ASIC) that acts as the brain of the vehicle. However, Reuters reports that microcontrollers and other devices that are in short supply worldwide will not be manufactured.
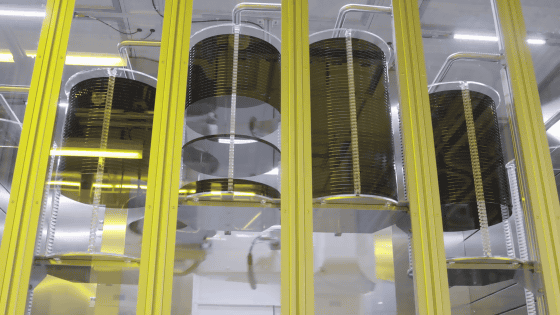
'Why does Bosch manufacture semiconductors for automobiles?' Is explained in the following video.
Travel back in time: Semiconductor development history at Bosch --YouTube
Bosch, which began researching semiconductor technology in the 1950s, set up the world's first mass production system for automotive integrated circuits in 1970. Bosch's integrated circuits, which developed a technology called Jetronic and provided ABS , which had been researched for a long time, were first installed in the Mercedes-Benz S-Class as part of ABS in 1978.
Demand for semiconductors installed in automobiles is increasing due to advances in electric vehicles and autonomous driving technology, and Bosch is appealing that semiconductors that bring various uses will be a key technology in the IoT society. Bosch CEO Volkmar Denner said, 'Semiconductors are a core technology for Bosch, and it is strategically important to develop and manufacture them in-house. The factory built in Dresden will manufacture semiconductors with the help of artificial intelligence. We will take it to the next level. '
Related Posts: