What does it look like inside a rocket engine that starts in just a few seconds?
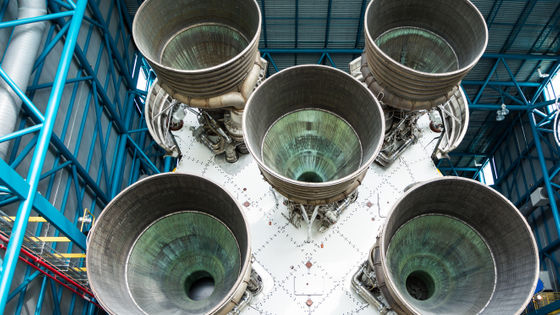
The H3 rocket test machine No. 1, which was launched from the Tanegashima Space Center on March 7, 2023, had a problem with the ignition of the second stage engine, and a command destruction signal was sent out, leading to a successful launch.
How To Start A Rocket Engine | Everyday Astronaut
https://everydayastronaut.com/how-to-start-a-rocket-engine/
A liquid fuel rocket is a mechanism in which fuel and oxidizer are sent into the combustion chamber at high pressure and ejected from the nozzle at high speed to obtain thrust. In order to start the liquid fuel rocket engine, it is necessary to control the pressure and temperature very complicatedly with the valves and pumps in the engine, and even a slight mistake will cause the engine to break down.
When the fuel is ignited, a cooling propellant flows through the walls and pumps so that the heat generated does not melt the engine or combustion chamber. At this time, thousands of liters of propellant per second flow, so the metal, valves, and bearings become brittle and prone to failure. This seems to be remarkable in engines that run on a propellant called 'kerolox' that uses kerosene and liquid oxygen, hydrolox that uses liquid hydrogen and oxygen, and metalox that uses liquid methane and oxygen. The majority of liquid-fueled rockets use these propellants and are used in various engines such as SpaceX's Merlin , Saturn V engines, and Atlas V 's RD-180 .
In any case, the first thing to do when igniting the fuel is the work of cooling. Cooling the engine is not only to protect the engine from cold propellant, but also to protect the propellant from warm engine.
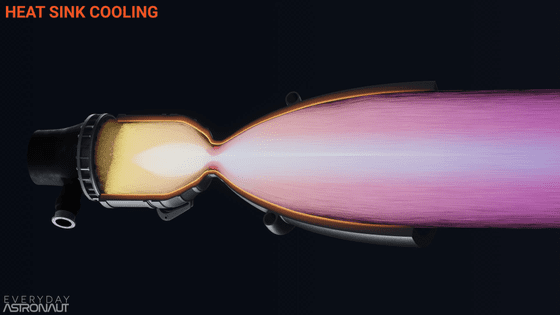
If the propellant boils before it reaches the pump tube, a phenomenon called cavitation can occur, in which small bubbles are formed in the liquid. These bubbles can abrade the pump material and damage the blades. Foaming can also disrupt the amount of propellant being sent to the combustion chamber, which can damage or destroy the engine by, for example, not getting enough air for combustion. It seems that there is something to do with it.
Once the engine is ready to start, the next goal is to get the pump spinning. The operation method called
Therefore, a high-power, high-pressure engine with a turbopump is required. Most engines produce hundreds of thousands of horsepower from just one turbine. High pressure helium or nitrogen must be pumped into the gas generator and preburner to spin the turbine at high speed. However, the specific impulse of these systems is weak, so they are only used to keep the engine burning so as not to overwork the engine.
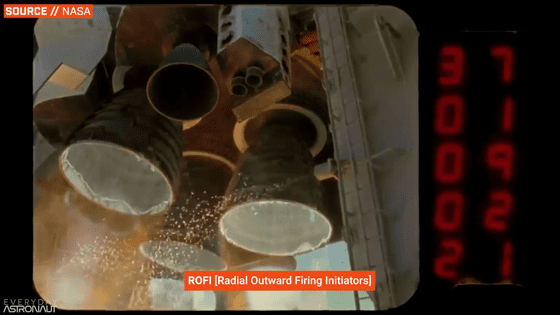
When the conditions for launch are ready, propellant begins to flow into the engine. But even the slightest error in this process can lead to mistakes, and if the propellant flows in the wrong proportions, or burns at the wrong time or in the wrong place, the engine will over-pressurize and explode. There is also a possibility that it will be lost.
There are several methods of igniting an engine, such as igniting a large piece of wood with
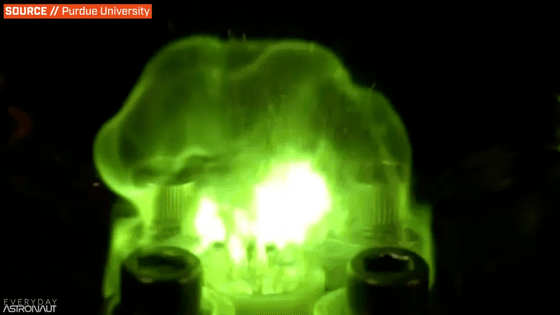
Up to this point, it is a method of igniting on the earth, but there are cases where it is ignited in outer space when the rocket is sailing. On Earth, where gravity is in effect, we know for sure that the liquid propellant is at the bottom of the tank and the gas is at the top of the tank, but this is not the case in space. Therefore, in outer space, it is first necessary to confirm where the propellant is in the tank.
What is used in this case is called '
SATURN IB S-IVB Staging-AS-202-Realtime, Dual Camera View (1966)-YouTube
After cooling and ignition of the engine, the next step is to enter the 'preparation stage for starting' in which moisture is removed from the inside. To do so, open the main fuel pre-valve and let liquid hydrogen flow from the fuel pump into the main fuel valve. Some of this propellant is recycled, dumping some of the hydrogen overboard and back to the fuel filler. Once the water in the engine is gone, we prepare the thermal conditions for launch.
Three seconds before starting the engine, the oxygen and hydrogen line bleed valves are closed and the engine waits for the start command. When this command is received, the main fuel valve is fully opened first. The time it takes for this valve to fully open is approximately two-thirds of a second.
At this point the pump is spinning quickly and 1.25 seconds after engine ignition the computer does a fuel pump turbine speed check. After 1.4 seconds from the start of the ignition sequence, the fuel pre-burner starts when the pressure rises sharply after a large pressure drop.
0.2 seconds after starting the engine, the oxygen valve in the main fuel chamber begins to open, allowing oxygen to flow into the ignition system. The valve opens slowly to less than 60% opening, but by setting this delay, it is said that sufficient amount of oxygen will be supplied to the ignition device at the appropriate time.
This is the ignition device.
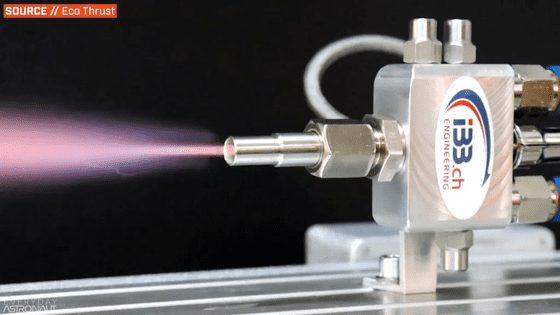
Also, just 1/10th of a second after ignition of the main fuel chamber, the oxygen preburner igniter activates and ignites. The flow of oxygen required for the sequence is always modest, carefully balanced to provide enough power to the engine, but not too much oxygen to reach high temperatures. I'm here. Through this process, the engine reaches the power required for operation in just five seconds after starting.
``It's very difficult to start a rocket engine. It is easy to imagine that when a company announces that it has successfully started a new engine, it deserves a huge round of applause and means that one of the major development hurdles has been overcome.” said.
Related Posts: