A brave man who created a 'field emission electric propulsion engine' that obtains thrust by injecting liquid metal ions appears
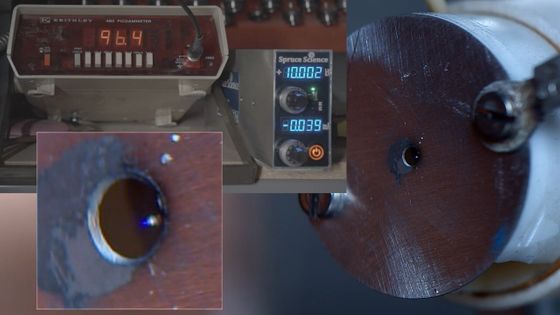
Accelerating Gallium Ions to 0.056% light speed - YouTube
To power a spacecraft, some sort of rocket engine is required. During launch, which requires a huge amount of energy, liquid or solid fuel is burned to eject high-temperature, high-pressure gas.
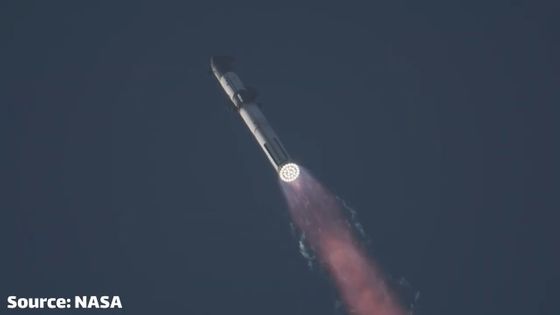
On the other hand, the thrust required for attitude control in space is significantly less, so ion thrusters that use metal ions as a propellant are also used. In either case, the mechanism is the same: some kind of mass is ejected in the opposite direction to the thrust.
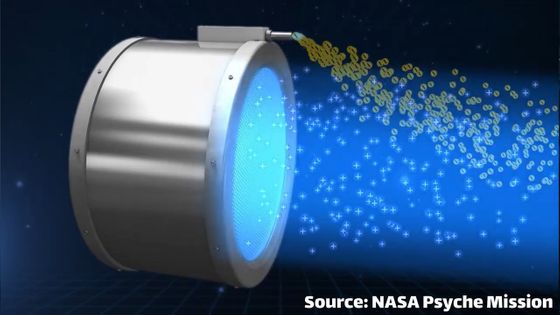
This time, Breaking Taps decided to build a homemade FEEP thruster. In principle, it is a very simple device, but it was quite difficult to implement, and over the course of about two months, they tried three different methods and built six or seven prototypes.
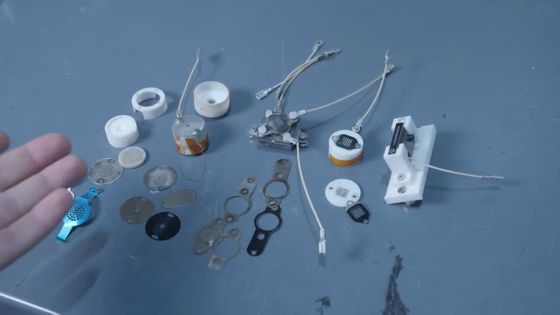
Basically, FEEP thrusters use
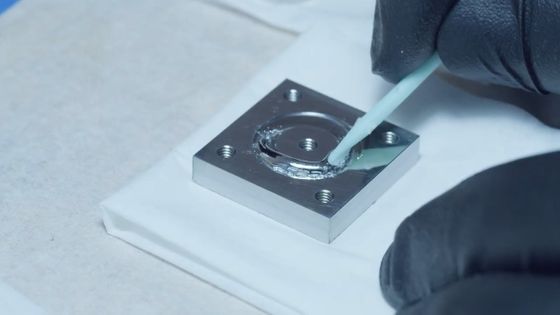
The tip is formed by capillary action in a strong electric field, usually 7,000 to 10,000 volts, and at the tip, the electric field pulls the metal away from the tip, forming a cone-shaped cone (Taylor cone), and the liquid metal that has begun to ionize is pulled away from the cone. The ions released in the vacuum can reach speeds of 20 to 40 km/s, which is the thrust of the FEEP thruster.
In the FEEP thruster, the liquid metal needs to reach the tip of the engine mechanism so that ions can be emitted from there. There are three main types of mechanisms for delivering liquid metal to the tip: 'Capillary Emitter', 'Externally Wetted Emitter' and 'Porous Wmitter'.
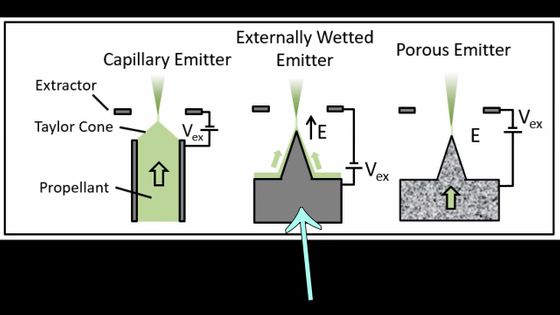
First, Breaking Taps built a prototype using a porous emitter array made from glass, which, when saturated, effectively wicks liquid metal up to the tip.
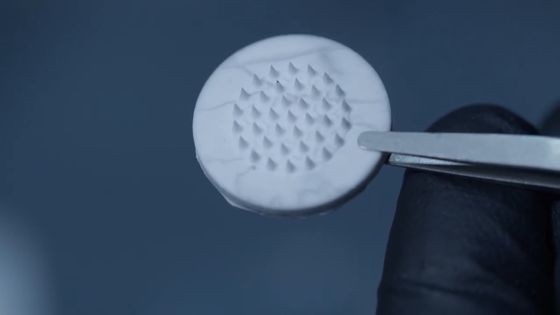
The liquid metal used in the experiment was
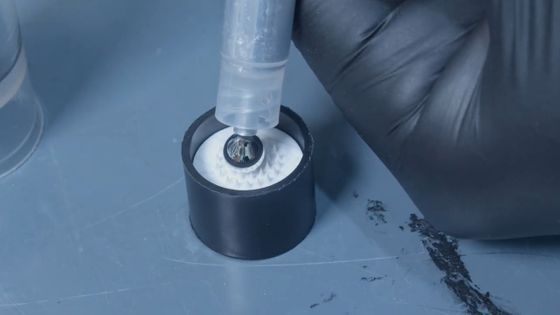
On the other hand, Galinstan forms an oxide coating on its surface, making it very difficult to penetrate Galinstan into a porous glass emitter.
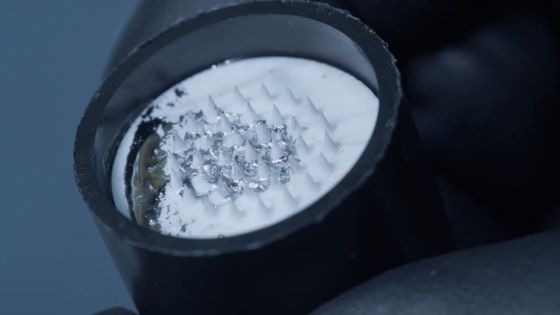
I finally had a prototype good enough to test, so I placed it in a vacuum chamber and applied voltage to it.
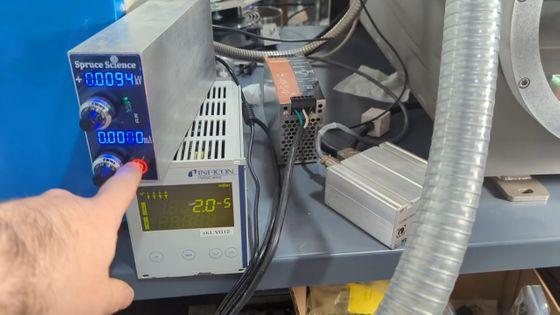
As the voltage increased, sparks appeared, then went quiet. Although the first prototypes showed promise, further iterations failed to improve the results, proving that porous emitters were not the best approach.
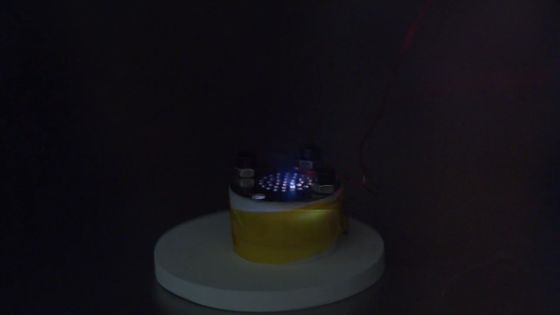
Breaking Taps then worked on a prototype capillary emitter, machining a piece of stainless steel to create an annular slot with two parts separated by a gap of 12
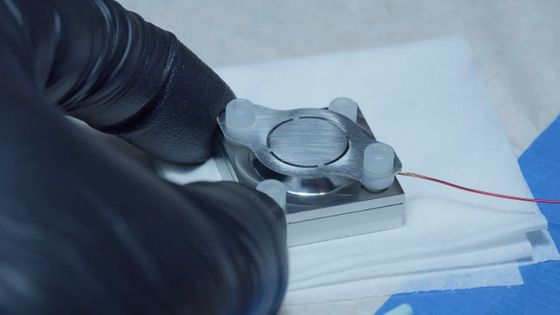
Experiment in a vacuum chamber.
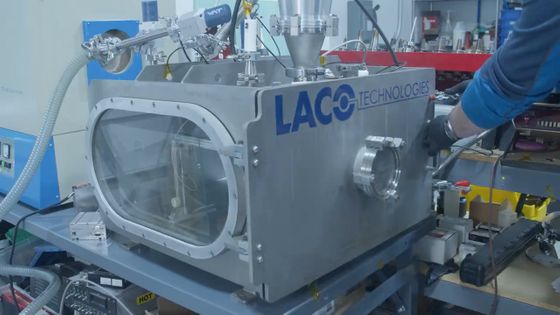
However, the footage of the first few experiments is no longer available because electromagnetic interference corrupted the video files on the camera's hard drive.
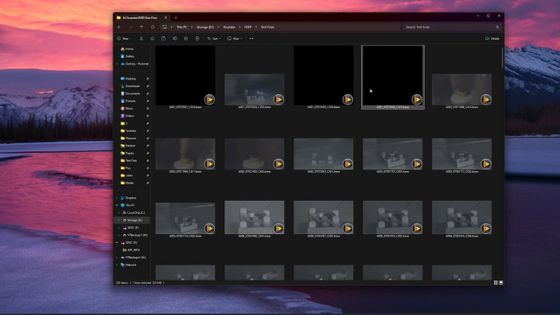
As a result of the experiments, they encountered problems such as gallium spraying out from the bridge section connecting the external and internal electrodes, and the droplets causing short circuits and
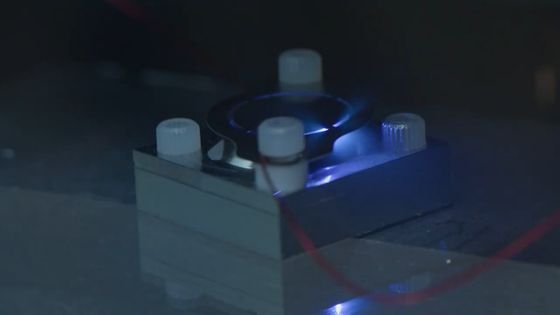
They also tried connecting the electrodes with long wires instead of a bridge, but this also failed.
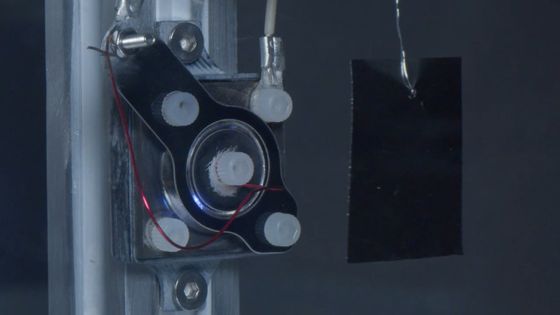
Breaking Taps has built a FEEP thruster with an external wet emitter, which uses a simpler method of applying gallium directly to an array of spikes.
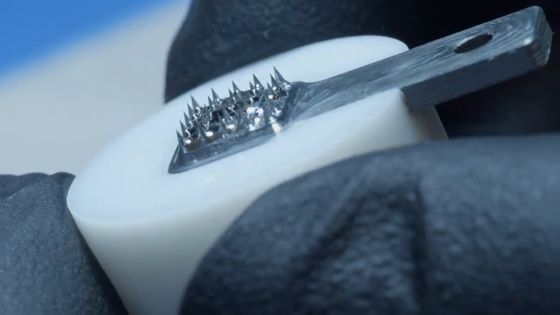
After the gallium covered the spikes, the cover was placed on top and secured in place with screws.
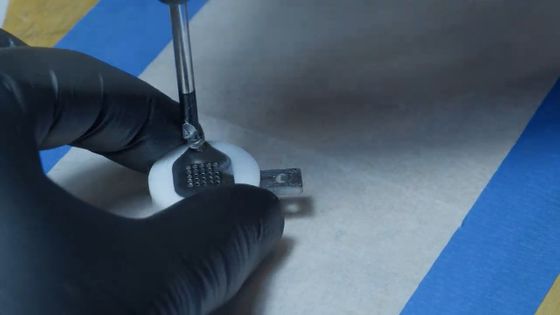
However, during testing, the reaction was unstable, and there were frequent incidents of droplets spraying out and short circuits. Various adjustments were made, but there was no improvement.
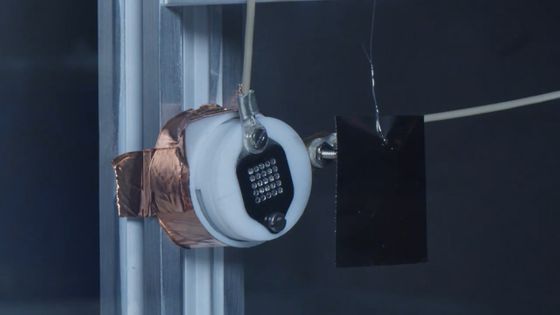
Breaking Taps then prototyped a capillary emitter that used a straight slot rather than a circular slot, which has the advantage that it is much easier to manufacture.
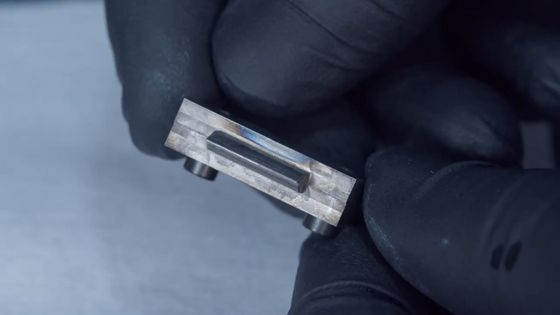
The slot gap looks like this.
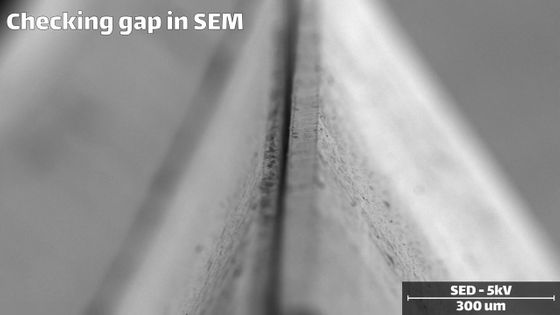
Modifications were made to control the occurrence of arcing outside the emitter, but arcing still occurred when the electrodes were too close.
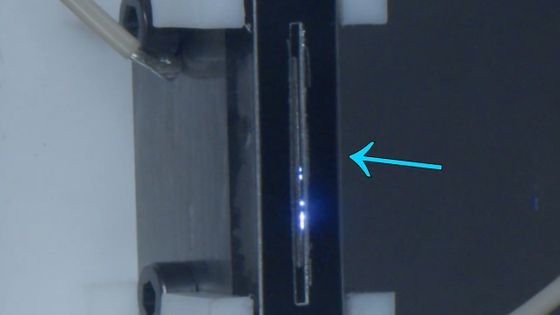
Breaking Taps then considered abandoning the project altogether, but built a prototype capillary emitter using a 'single tube.'
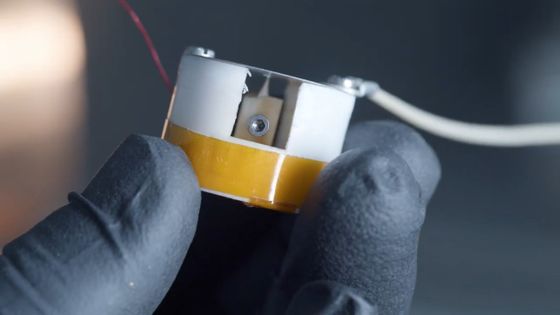
This is a glass micropipette.
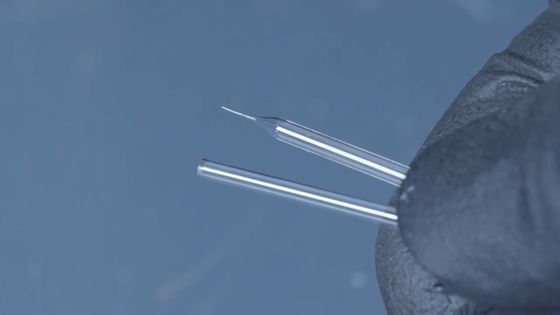
When gallium is filled inside, it is instantly sucked up to the tip, which is only 1 to 2 μm wide.
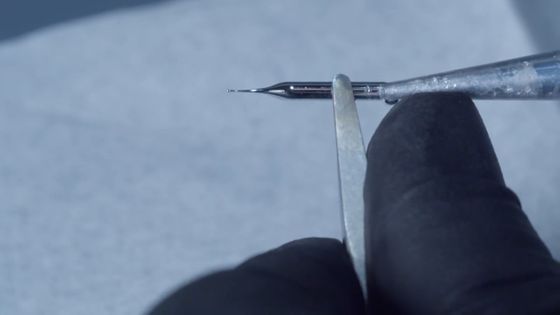
The advantage of using a single glass capillary emitter is that it can be completely insulated, theoretically preventing arcing and accidental shorts.
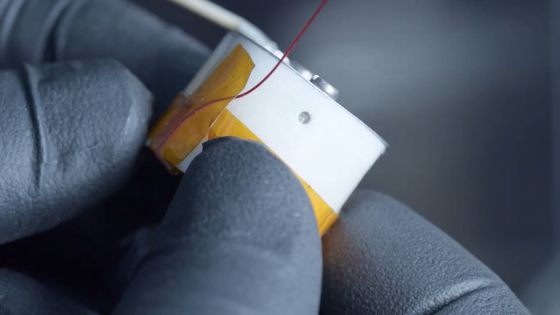
A close-up analysis of the experiment with a single capillary emitter revealed that a Taylor cone formed on the surface, igniting the plasma, and then releasing droplets instead of controlled ions.
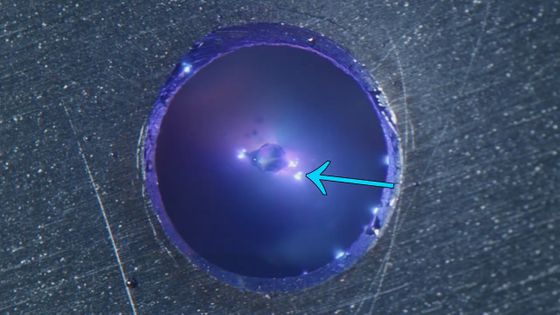
This is because the oxide film on the surface has a high surface tension, which means that a high voltage is required to form a Taylor cone. However, the fresh gallium that appears on the surface after the Taylor cone is formed does not have an oxide film, so if left alone, excessive voltage would be applied.
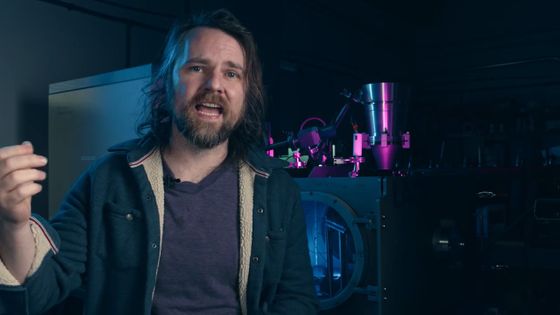
Breaking Taps then devised a way to suppress the arcing by controlling the voltage, and repeated the experiment using
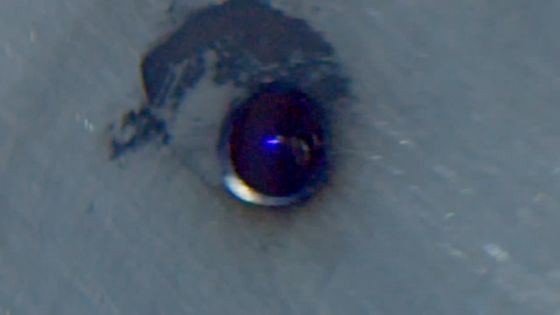
It was also discovered that embedding gallium in tungsten wire and heating it was effective in stably attaching gallium to the tungsten wire.
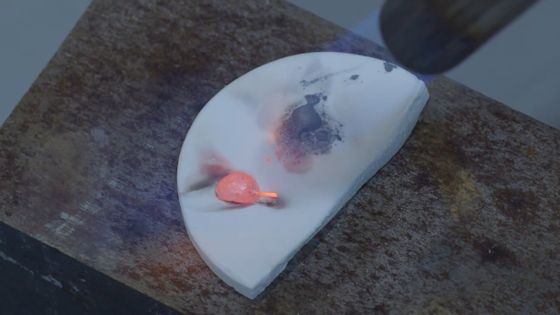
When we measured the thrust generated by this FEEP thruster, we found that it was approximately 11.80 μN (
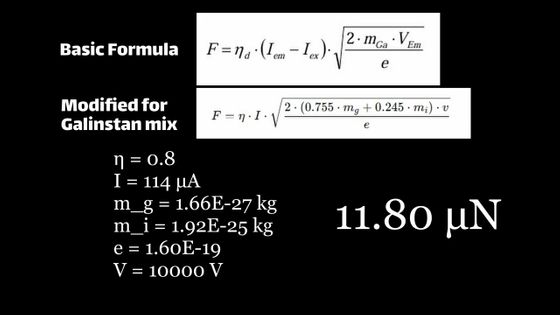
In addition, various prototypes were produced in this project, but many of the failures were due to lack of voltage adjustment, so if that was improved, some of the failed prototypes might have worked. Breaking Taps said.
Related Posts: