Pointed out that the explosion accident that occurred at the chemical factory was caused by the occurrence of 'popcorn polymer' due to lack of management
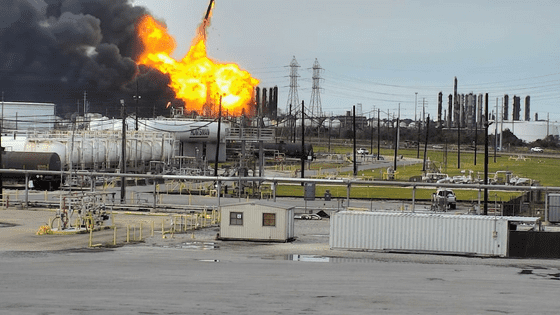
On November 27, 2019, two explosions
The Danger of Popcorn Polymer: Incident at the TPC Group Chemical Plant-YouTube
An explosion occurred in the early morning of November 27, 2019 at the chemical plant of the TPC Group , a specialty chemical manufacturer in Port Netize , Texas.
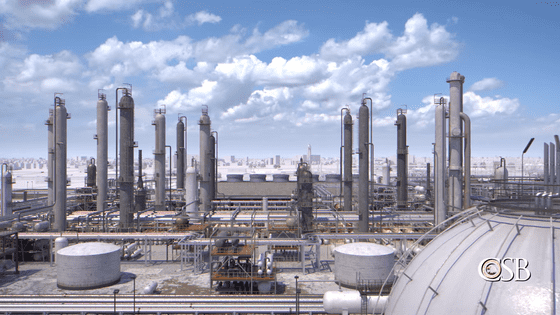
At the time of the accident, the TPC Group was manufacturing
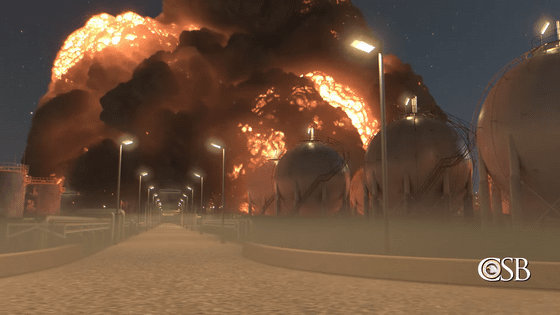
Butadiene is a very reactive chemical, and without proper controls it can react with oxygen to form a solid material called 'popcorn polymer'.
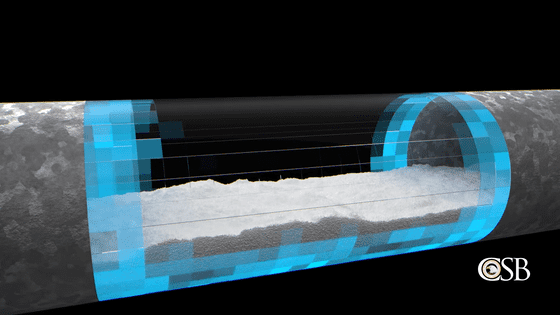
This popcorn polymer builds up inside the device, and when it grows, it creates a very high pressure, and it is said that the containment function of the piping is lost, and there is a danger that the device will eventually burst and explode.
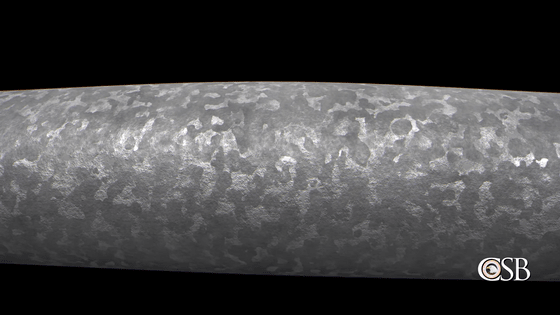
Regarding how the popcorn polymer was formed at the chemical plant, USCSB's Sylvia Johnson said, 'Workers shut down the primary pump of a butadiene production unit for repairs and used a spare pump to keep it running. It is thought that the reason is that the maintenance system was inadequate.'
A part without flow called '
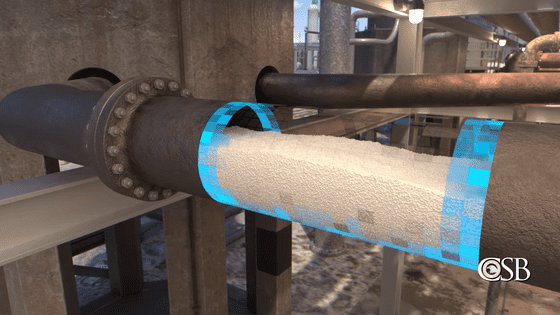
As a result, the piping of the butadiene manufacturing equipment burst, and about 6000 gallons (about 22,000 liters) of liquid based on butadiene was discharged.
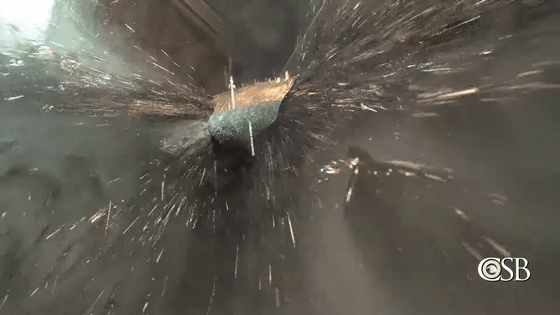
The ejected liquid quickly vaporized in the atmosphere and turned into a flammable gas.
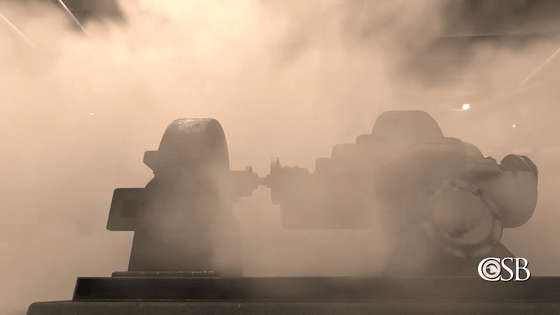
Two minutes after the pipe burst, butadiene ignited and an explosion occurred. A pressure wave destroyed part of the facility, injuring two employees and a security guard.
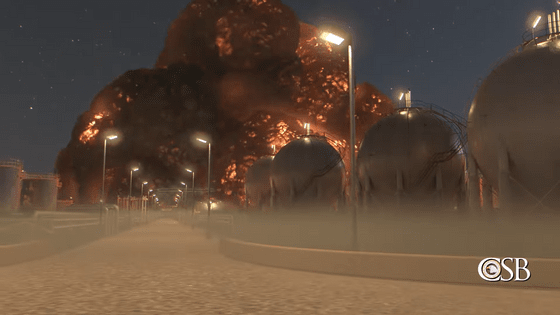
After that, the American Chemical Safety and Toxic Investigation Commission began an investigation into this accident and discovered a significant safety issue that led to the explosion accident. The plant had established operating procedures for the production of high-purity butadiene, intended to minimize the formation of popcorn polymer. No measures were indicated.
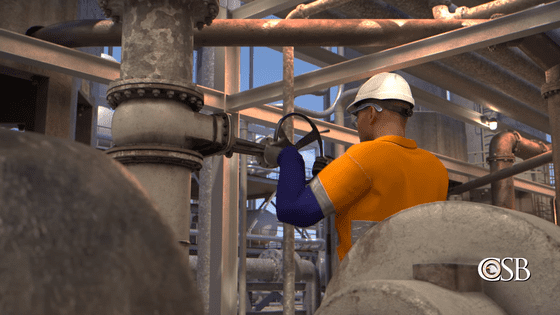
In response to this accident, the USCSB has recommended that
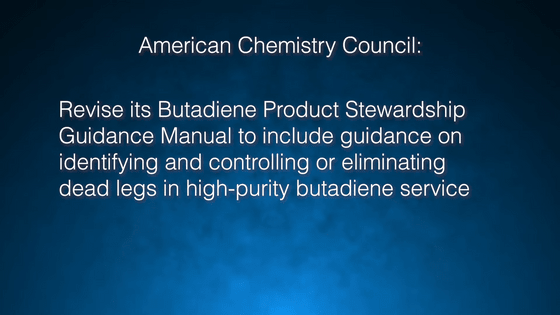
The second issue identified by the USCSB is that 'the maintenance regime was inadequate.' In 2016, the USCSB advised TPC Group to clean its production lines twice a month to reduce the risk of popcorn polymer buildup. However, it was noted that the TPC Group did not follow these recommendations and did not take steps to effectively control or prevent the formation of popcorn polymers.
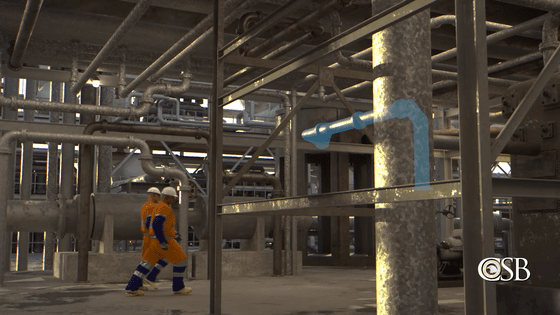
USCSB's Bach Griffin said the TPC group knew the popcorn polymer was building up and clogging equipment, but prioritized repairing primary pumps, shutting down lines for cleaning, and removing popcorn polymer. He said that he did not take drastic actions such as administration of inhibitors, but took ad hoc measures such as removing the clogging that was found. The resulting explosion is believed to have been caused by an unknown accumulation of popcorn polymer.
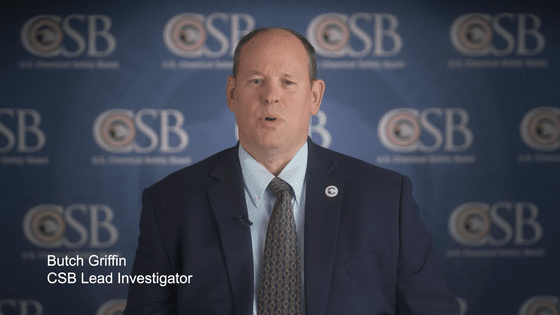
The USCSB also said, ``If popcorn polymer was confirmed in the piping of the manufacturing equipment, it should have stopped production and immediately investigated,'' pointing out that an appropriate investigation was not conducted within the TPC group. I'm here. The USCSB said, ``If the investigation policy had been clearly defined, such an accident could have been avoided,'' and requires compliance with the Butadiene Product Management Guidance Manual.
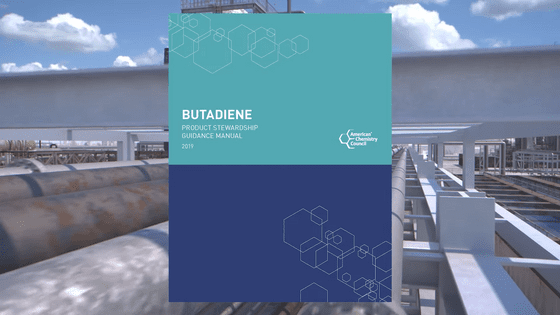
The USCSB also noted that there were no remote-operated emergency isolation valves in the plant. If a remote-operated emergency isolation valve was installed in the manufacturing process, it was possible to minimize the generation of steam and the scale of the explosion. The USCSB also said that the second explosion caused by the first explosion could have been prevented if a remote-operated emergency isolation valve had been installed, minimizing the damage caused by the accident. I am pointing out the possibility that
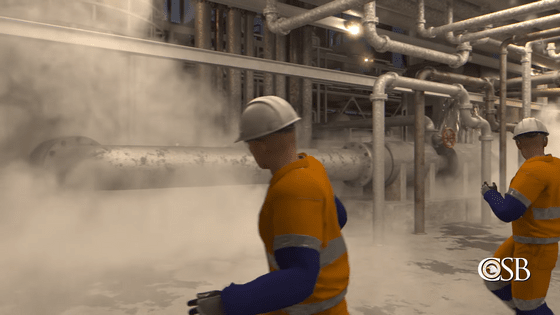
'Facilities that handle and store large quantities of high-purity butadiene must take appropriate control of popcorn polymer within the manufacturing process to prevent the recurrence of horrific incidents such as those at TPC Group's chemical plant,' the USCSB said. We are calling attention to this.
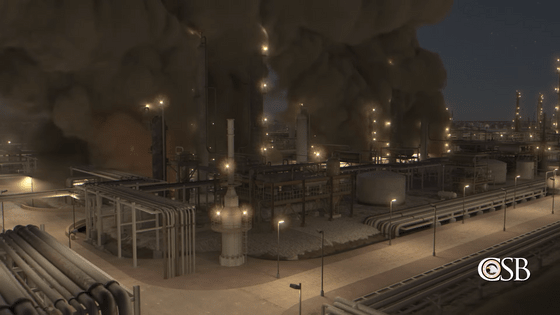
Related Posts: