How is a non-woven filter used for high-performance masks to catch viruses?
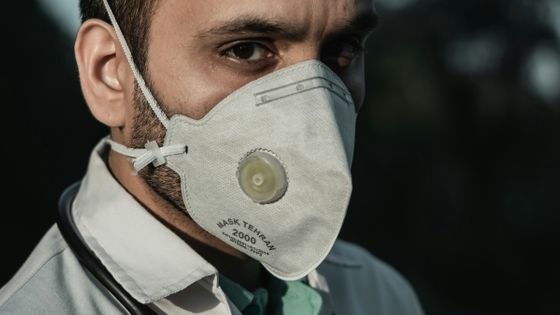
With the epidemic of the new coronavirus infectious disease (COVID-19), the demand for masks is increasing all over the world. Based in
Meltblown procedure: Producing coronavirus mask filter fleece | Science | In-depth reporting on science and technology | DW | 18.05.2020
https://www.dw.com/en/meltblown-procedure-producing-coronavirus-mask-filter-fleece/a-53480709
High-performance masks used by healthcare professionals must prevent all types of contaminants such as abrasives, dust, aerosols, and viruses, and non-woven fabrics used as filters must also have high performance. It seems that the filters used for such high-performance masks are made by a special manufacturing method called ' melt blown manufacturing method ', and the machine developed by Reicofil can produce high-performance mask filters using the melt blown manufacturing method. thing.
Reicofil's research facilities are equipped with research equipment that can actually reproduce the manufacturing process to assist non-woven manufacturing companies in product development. In response to the global demand for masks due to the COVID-19 pandemic, Reicofil has begun manufacturing filters for masks using research facilities.
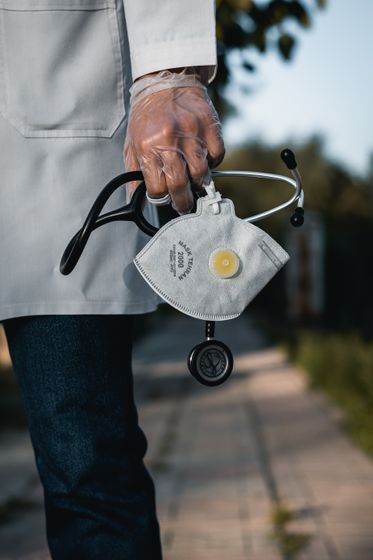
The raw material for the non-woven fabric is
However, polypropylene, which is simply made into a fine thread through a thin nozzle, seems too thick to function as a non-woven filter. Therefore, in the melt blown method, polypropylene yarn is blown with extremely hot air to make it thinner. 'The polypropylene we use has a melting point of 160 degrees Celsius and the hot air that blows on the yarn is 250 degrees,' said Detlef Frey, head of research and development.
The hot air blows the polypropylene thread at a momentum of about 300 meters per second, but by hitting this hot air around the thread from two directions, a random air vortex is formed in a narrow range. This vortex further accelerates the flow of air that hits the thread, and the thread released by the hot air becomes thinner. 'It is necessary to apply hot air to make the yarn thinner and at the same time prevent the yarn from breaking,' Frey commented that making a non-woven fabric while maintaining high quality is a difficult and attractive process.
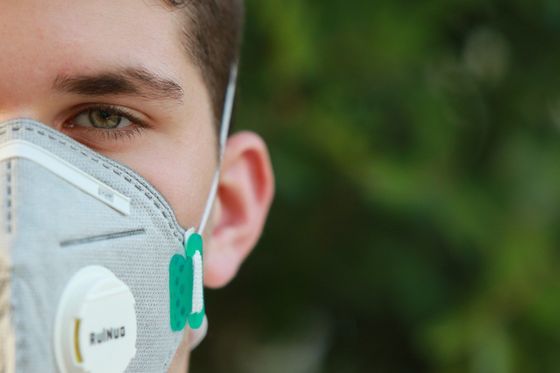
Development engineer Alexander Klein said, 'We need to adjust the settings to obtain a non-woven fabric that is free of yarn breaks and breaks and that is problem-free, which results in a product with even fiber fineness. Control of the manufacturing process will be extremely important in the production of non-woven fabrics. The manufacturing machine developed by Reicofil is equipped with a system that optically detects product defects and also has a sensor that automatically measures the air permeability of the finished filter. In this way, some problems are automatically checked, but periodic filter samples are taken to measure the air permeability and the separation rate as a filter, and whether the filter classification meets the required specifications. It is necessary to check whether it is.
'Testing can detect changes in a process that indicate something isn't working,' Klein said. The reason why such a strict check system is required is because the melted polypropylene, which is the raw material of the nonwoven fabric, is fluid and has a tackiness.
Frey says, “The random movement of polypropylene threads helps create the intertwined mesh that forms the filter net. The physical pore size in the filter net is about 10
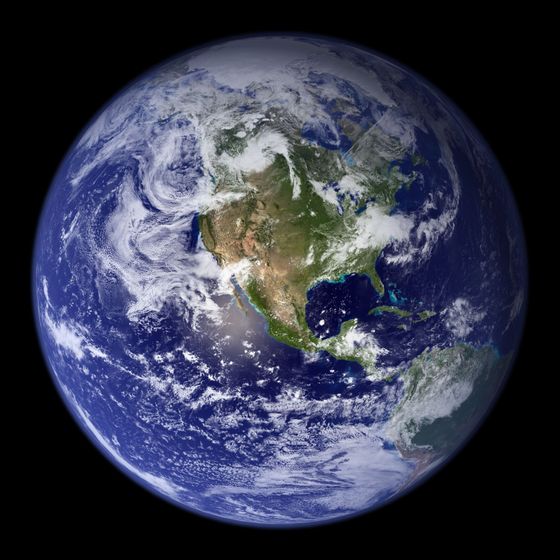
Although the non-woven filter is very fine, it is said that the size of the new coronavirus is about 0.1 to 0.2 micrometers, which is far smaller than the filter hole. Therefore, engineers are making various efforts to catch viruses that are smaller than the holes in the filter.
'One is
In addition, some viruses, including the new coronavirus, are covered with a lipophilic membrane ( envelope ), which makes them easier to stick to lipophilic polypropylene, which also improves the effectiveness of the mask. In addition to this, in Reicofil, the finished non-woven fabric is moved on rollers and at the same time charged with a high voltage electrode to make the filter electrostatically charged. This electrostatic force also plays an important role in catching viruses, Frey said.
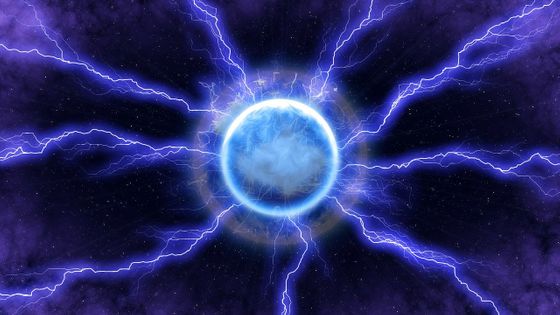
Related Posts:
in Science, Posted by log1h_ik